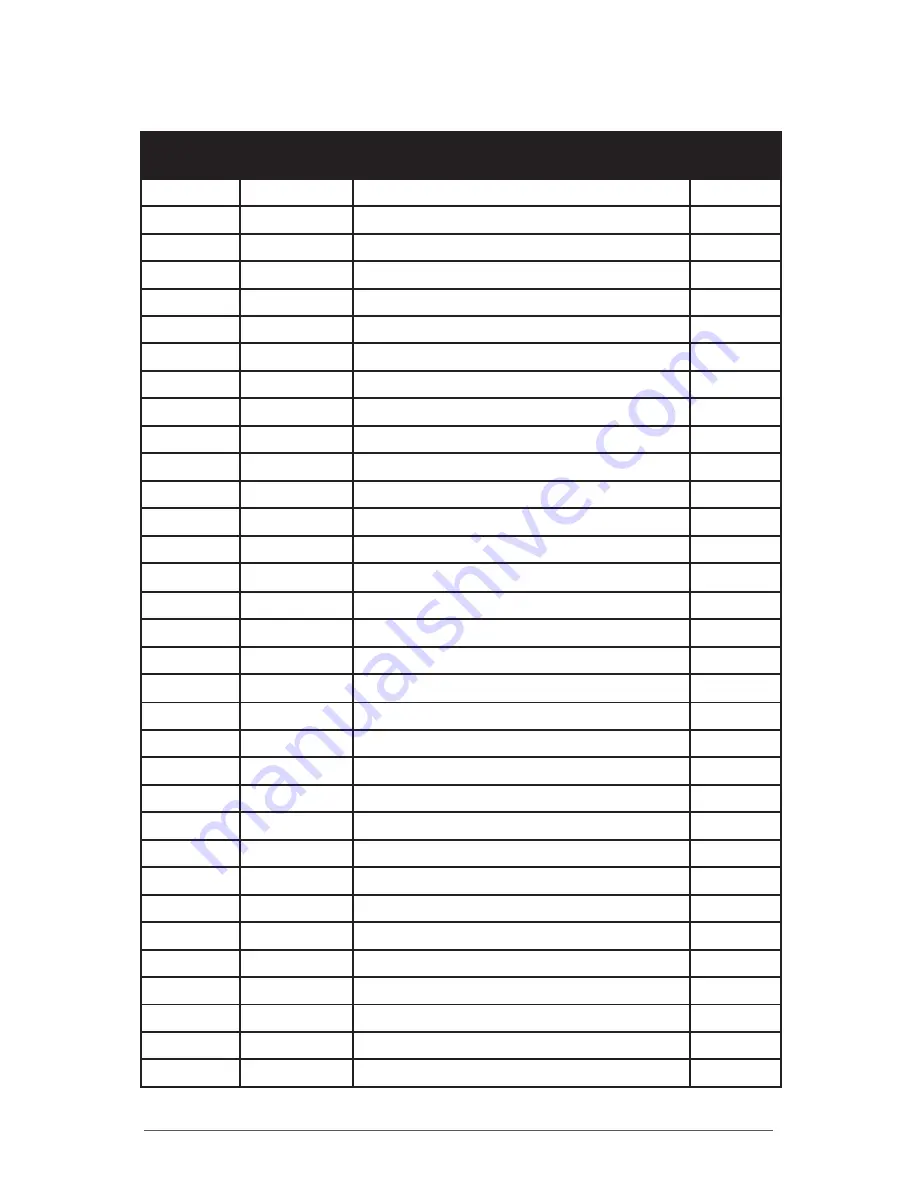
37
ALPHA
®
ECOGRINDER PARTS LIST (ECG-125)
DRAWING
NO.
PART
NO.
DESCRIPTION
QUANTITY
1
801373/801374
Breaker Assembly (w/case) 110V/220V
1
2
801324/801350
Power Cord 110V/220V
1
3
801359
Screw M8 x 15
4
4
801360
Lock Washer M8
4
5
801355
Handle Bracket -Left
1
6
801358
Handle Cover
1
8
801356
Handle Bracket -Right
1
9
801357
Handle Tube
1
10
133028
Bearing Sleeve
1
11
133025
Bearing 608-2RZ
1
12
133024
Insulation Disc
1
13
801321/801014
Armature Assembly 110V/220V
1
15
133050
Woodruff Key
1
16
801022
Armature Retainer Plate
1
17
133053
Bearing 6201-2RS
2
18
801064
Gear (small)
1
19
801384/801635
Soft Starter Assembly 110V/220V
1
20
133047
Cable Sleeve
1
21
130031
Self-Tapping Screw 3.9 x 19
6
22
133086
Cable Clamp
1
23
801116
Handle-Right
1
24
801038
Switch w/ screws
1
25
801003
Motor Housing
1
26
801030
Carbon Brush Spring
2
28
801594
Carbon Brush (2 pc set)
2
29
801318/801004
Field Coil 110V/220V
1
30
801029
Carbon Brush Holder
2
31
801080
Self-Tapping Screw 1.9 x 5
2
32
801117
Handle-Left
1
33
801033
Wire (Coil to CB holder)
2
34
801362
Alpha
®
Name Plate
2
35
801361
Builders Plate 110V
1
36
801032
Wire (Coil to Switch)
1
02/05/2013