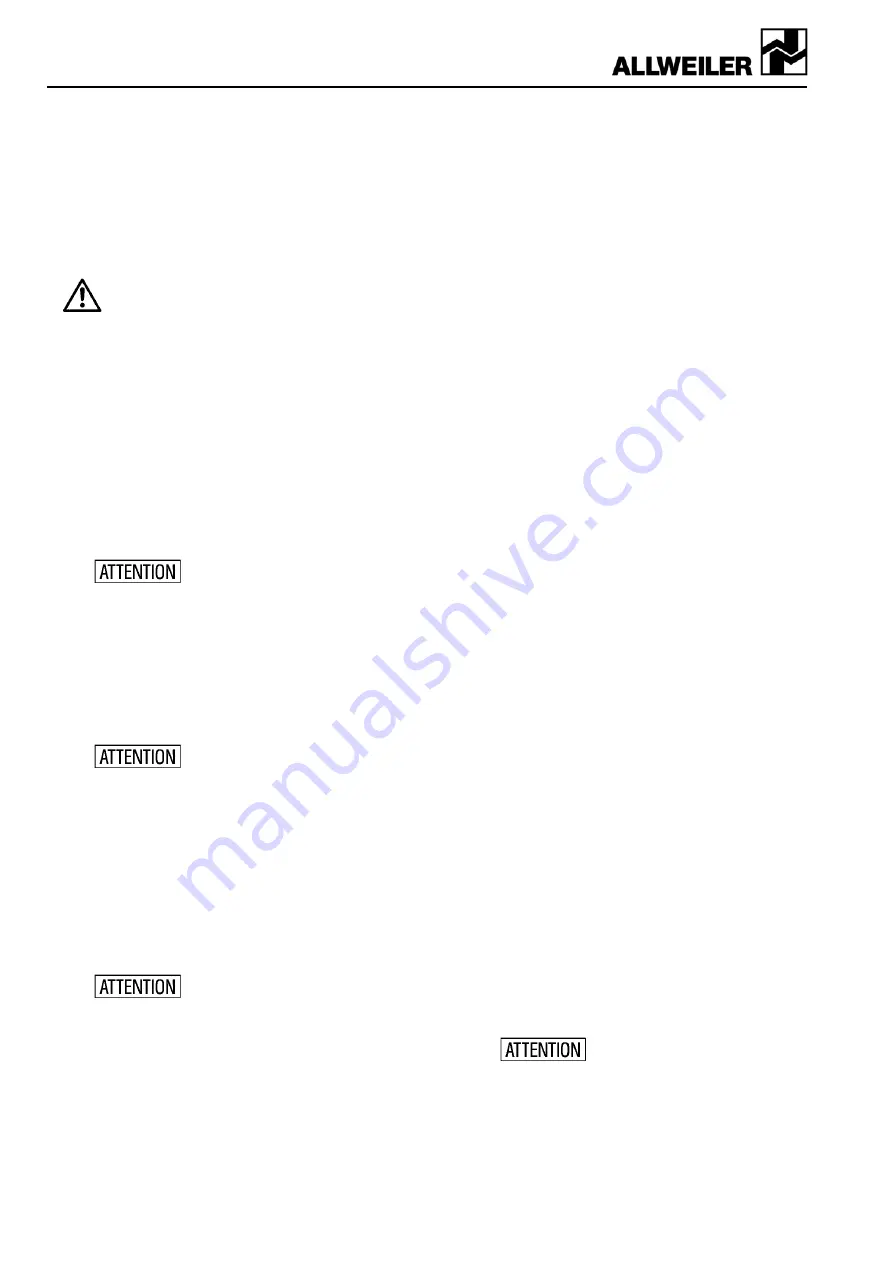
8
Series AE1L, AE.E, AE.N, AE.H, AE.V, AED1E, AED2N
Design ID, ZD
6.1.4 Turning on the additional facility for heating or
cooling the stuffing box casing and/or the suction
casing (double-jacket casing)
If the pumps are equipped with these additional fea-
tures, all shut-off devices for heating or cooling sys-
tems must be opened. The following pressure and
temperature limits must be observed.
!
Supply of the cooled or heated stuffing box
and/or suction casing (double-jacket casing)
with suitable liquid media
Only liquid media
may be used as heating or
cooling liquid under consideration of the corrosion
resistance of all touching parts.
The maximum heating or cooling liquid pressure
is 6 bar. The maximum heating temperature may
not exceed 150°C and the cooling temperature
may not be below -40°C.
Note
: The design temperature is listed in the or-
der data sheet.
6.1.5
Breaking away of the pump
When initially starting the pump or after longer periods
of standstill, you have to make sure that the drive en-
gine turns the pump effortlessly. Should this not be
easily possible due to the high adhesion between the
rotor and the stator in new state, use suitable tools on
the feather key section of the drive shaft to free the
pump.
The drive shaft may not be
damaged here!
6.1.6 Control
of
the sence of rotation
The normal rotation direction of the pump seen from
the drive against the drive shaft is to the left. Here the
suction connection is located on the side of the shaft
seal so that the shaft seal is relieved. In special
cases, e.g. when sucking from a vacuum or convey-
ing media that do not tolerate gas cavities, the pump
rotates to the right. This switches the suction and the
outlet side around.
The rotation direction of the pump
must correspond to the rotation
direction arrow "n" on the pump's type plate. A wrong
rotation direction may cause damages to the pump. In
order to control the rotation direction, briefly press the
on/off switch of the engine.
6.2
Start-up
6.2.1 Start-up
Prior to starting the pump, all shut-off devices on the
suction and outlet side have to be opened.
6.2.2 Drive
Turn the motor on.
Observe the product-specific peculi-
arities of the drive.
See operating
instructions of the drive manufacturer.
6.2.3 Checking
the delivery values
Once the drive has reached its operating speed,
check the intake pressure and the pump end pres-
sure via the vacuometer and the manometer.
The motor may not be overloaded. The power intake
can be monitored with an ammeter. Check the tem-
perature and the viscosity of the conveyor liquid in this
context. The resulting values must be compared with
the order data sheet respectively acceptance proto-
col.
6.2.4
Protection against running dry
When no more conveyor media is sucked in by the
pump, the thermal energy emerging in the conveyor
elements of the eccentric screw pump through dry
friction and milling work is no longer carried off in a
sufficient quantity, which thermally destroys the stator
elastomer after a short time already. There are differ-
ent protectors against running dry for protecting the
conveyor elements that are adapted to the respective
operating conditions (consultation with the factory).
6.3
Shutdown
6.3.1 Shutoff
Turn the motor off.
6.3.2 Measures
in
case of longer periods of standstill
If longer operational breaks are intended and if there
is danger of frost, the pump must be emptied. To do
so, unscrew the screw plug (502) from the suction
casing (505) and afterwards conserve the pump (see
Chapter 3.3).
7.
Maintenance/Repair
7.1
Maintenance
!
For service and maintenance work, observe the
details in Chapter 2 “Safety”.
!
Regular monitoring and maintenance work on the
pump and the drive extends the service life.
7.1.1 General
monitoring
1. The pump may not run dry.
2. The drive engine may not be overloaded.
3. Check the suction and pressure pipes for tight-
ness.
4. An installed stuffing boxmust drip slightly during
operation. An installed mechanical seal may not
have any strong leaks.
5. Monitor pressure and temperature monitoring de-
vices and compare them with the order data sheet
respectively acceptance protocol.
6. Additional installations like flushing, sealing and
quenching of the shaft seal must be monitored if
provided.
7. Additional equipment for heating or cooling the
stuffing box casing and/or suction casing must be
monitored, if provided.
7.1.2
Maintenance of components
7.1.2.1 Joints of the joint shaft
The joints of the joint shaft are lubricated with
ALLWEILER special joint oil type B or oil ET1510 ISO
460 by Tribol Lubricants GmbH, Mönchengladbach, if
the pumps are deployed in the food industry, with
ALLWEILER special joint oil type BL or oil 1810/460
by Tribol Lubricants GmbH, Mönchengladbach.
Other lubricants were not tested by
us and can therefore not be recom-
mended!
The joints are lubricated for life. We do however rec-
ommend checking the joint collar for tightness when
opening the pump for other reasons and exchanging
the joint oil after 8,000 operating hours. The table in
Chapter 7.1.2.6 shows the allocation of the pump size
to the oil quantity in cubic centimeters. For changing