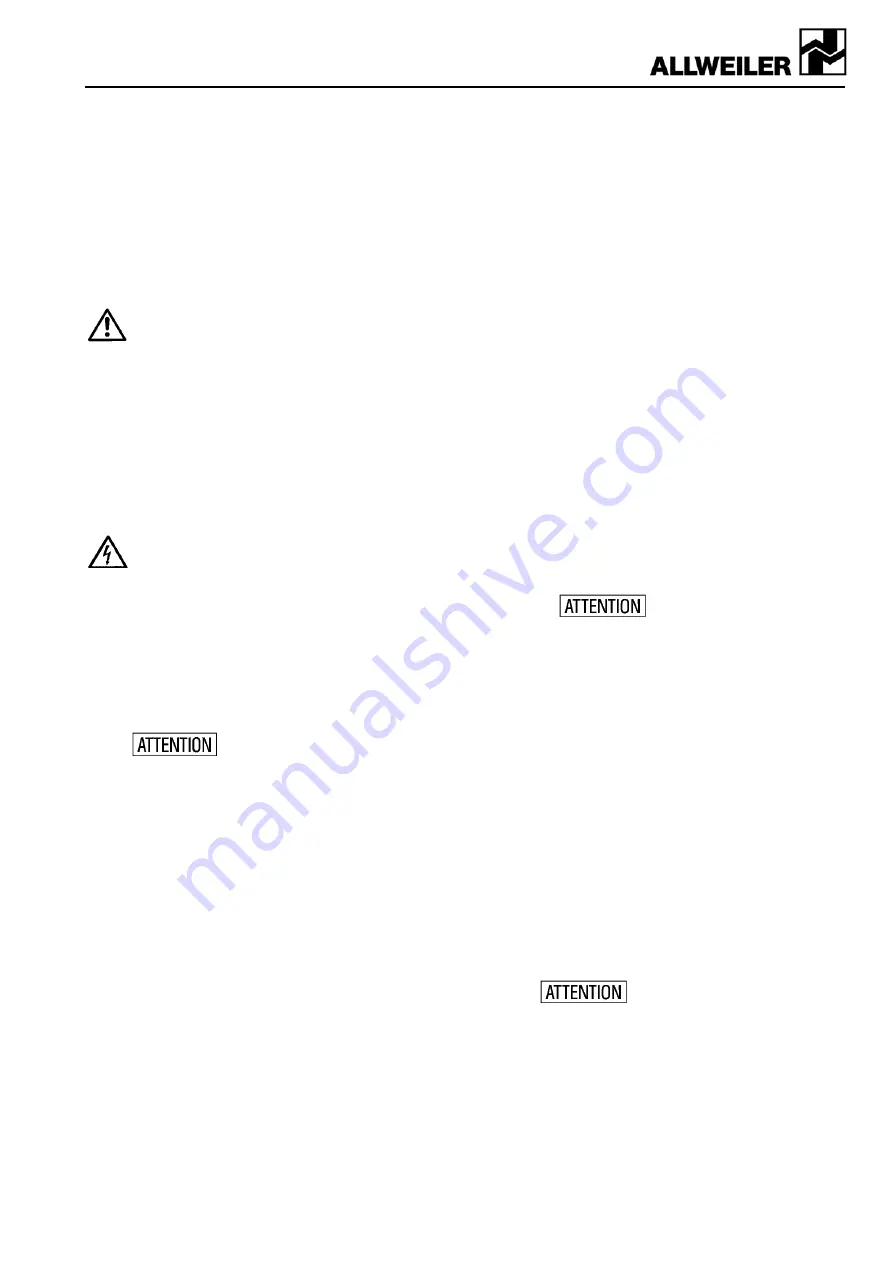
7
Series AE1L, AE.E, AE.N, AE.H, AE.V, AED1E, AED2N
Design ID, ZD
5.10
Safety and control facilities
5.10.1 Manometer and vacuumeter
A manometer and vacuumeter have to be connected
to the pressure and suction pipe.
5.10.2 Safety installation in the pressure pipeline
As soon as a stop valve is arranged in the pressure
pipeline or if it is possible that the pressure pipeline
will be clogged, a safety element must be provided,
e.g.: by-pass line with installed excess pressure
valve, bursting diaphragm, protective motor switch
etc.
Eccentric screw pumps are positive-displace-
ment pumps and can theoretically generate an
infinitely high pressure.
In case of a closed pressure pipe, e.g. because of
clogging or accidental closing of the valve, the
pressure generated by the pump may reach a
multiple of the admissible plant pressure. This
may cause pipes to burst, which must be espe-
cially prevented when handling dangerous con-
veyor substances. Therefore, the corresponding
safety equipment (e.g. pressure switches) also
has be installed in the plant.
5.11
Electrical connections
Only an expert may attach the power cables of the
coupled drive engine in accordance with the circuit
diagram of the engine manufacturer. The valid guide-
lines of the Electrician's Association and the public
power companies have to be observed.
Danger by electrical energy must be excluded.
6.
Start-up/Shutdown
6.1
Preparations for start-up
6.1.1
Filling the pump with liquid
The pump may not run dry!
For
initial start-up and after longer peri-
ods of standstill, the pump must be filled with liquid.
Even a few rotations without liquid may damage the
stator. For that reason, the suction casing must be
filled with water or conveyor liquid prior to start-up for
lubricating the stator and rotor. After long periods of
standstill, meaning when it must be assumed that the
residual liquid in the pump has evaporated or after re-
pairs, you have to repeat the filling process.
After filling, the pump works in self-priming mode.
Deairing is not necessary, as the pump can convey a
liquid-gas mixture.
6.1.2
Turning on the additional facilities for shaft seals
(if provided)
If the pumps are charged with a flushing/sealing or
quenching liquid, the provided shut-off slides must be
opened before putting the pump into operation for the
first time and set to the following pressure values:
!
Supply of the stuffing box with flushing or
sealing liquid
(Design P02, P12, P03, P13, P04
and P14).
Note:
Stuffing box with flushing or sealing cham-
ber ring require a flushing respectively sealing liq-
uid for maintaining the function.
The required flushing respectively sealing liquid
pressure for pumps with stuffing box is
P02/P12 = 0.1 to 0.5 bar
(above inner pressure of the suction casing)
P03/P13 = 0.5 bar
(above inner pressure of the suction casing)
P04/P14 = 0 to 0.5 bar
(Flushing and sealing liquid see Chapter 6.1.3.).
!
Supply of single-acting, non-relieving me-
chanical seal with throttle ring
(Design G0S/
G1S and G0T/G1T)
Note:
These mechanical seals require a flushing
liquid in order to maintain their function, which car-
ries off the emerging friction heat and limits the
penetration of the conveyor liquid into the sealing
chamber.
The required flushing liquid pressure is 0.1 to 0.5
bar above the inner pressure of the suction cas-
ing. The required flushing liquid flow for carrying
off the dissipation of the mechanical seal is listed
in the table in Chapter 7.1.2.6 (flushing liquid see
Chapter 6.1.3).
!
Supply of double-acting, non-relieving me-
chanical seal
(Design G0D/G1D)
Note:
These mechanical seals require a sealing
liquid in order to maintain their function, which car-
ries off the emerging friction heat and limits the
penetration of the conveyor liquid into the sealing
gap.
The circulation of the sealing
liquid must be secured prior to
each start-up.
The sealing liquid pressure must be approx. 1.5 to
2 bar above the pressure on the inside of the suc-
tion casing. The flowthrough quantity must be
regulated in such a way that the exit temperature
does not exceed approx. 60°C and is at least 30 K
below the boiling temperature at operating pres-
sure. The temperature difference between input
and output may amount to at most 15 K. (Sealing
liquid see Chapter 6.1.3).
!
Supply of the single-acting mechanical seal
with quench
(Design G0Q and G1Q)
The space between the mechanical seal counter-
ring and the shaft seal ring must be charged with
quenching liquid. The max. admissible pressure
difference between the quenching liquid pressure
and the pressure in the suction casing is p = 0,5
bar. The max. quenching liquid pressure is 3 bar.
(Quenching liquid see Chapter 6.1.3).
6.1.3 Quality
and
properties
of flushing/sealing and
quenching liquid
Any liquid may be used as
sealing/flushing or quenching liquid
under consideration of the corrosion resistance of all
touching parts and the compatibility with the medium
to be sealed. The liquid must be free from solid sub-
stances, may not be prone to deposits, should have a
high boiling point as well as a good heat conductivity
and low viscosity. Clean and soft water fulfils these
requirements to a high degree.