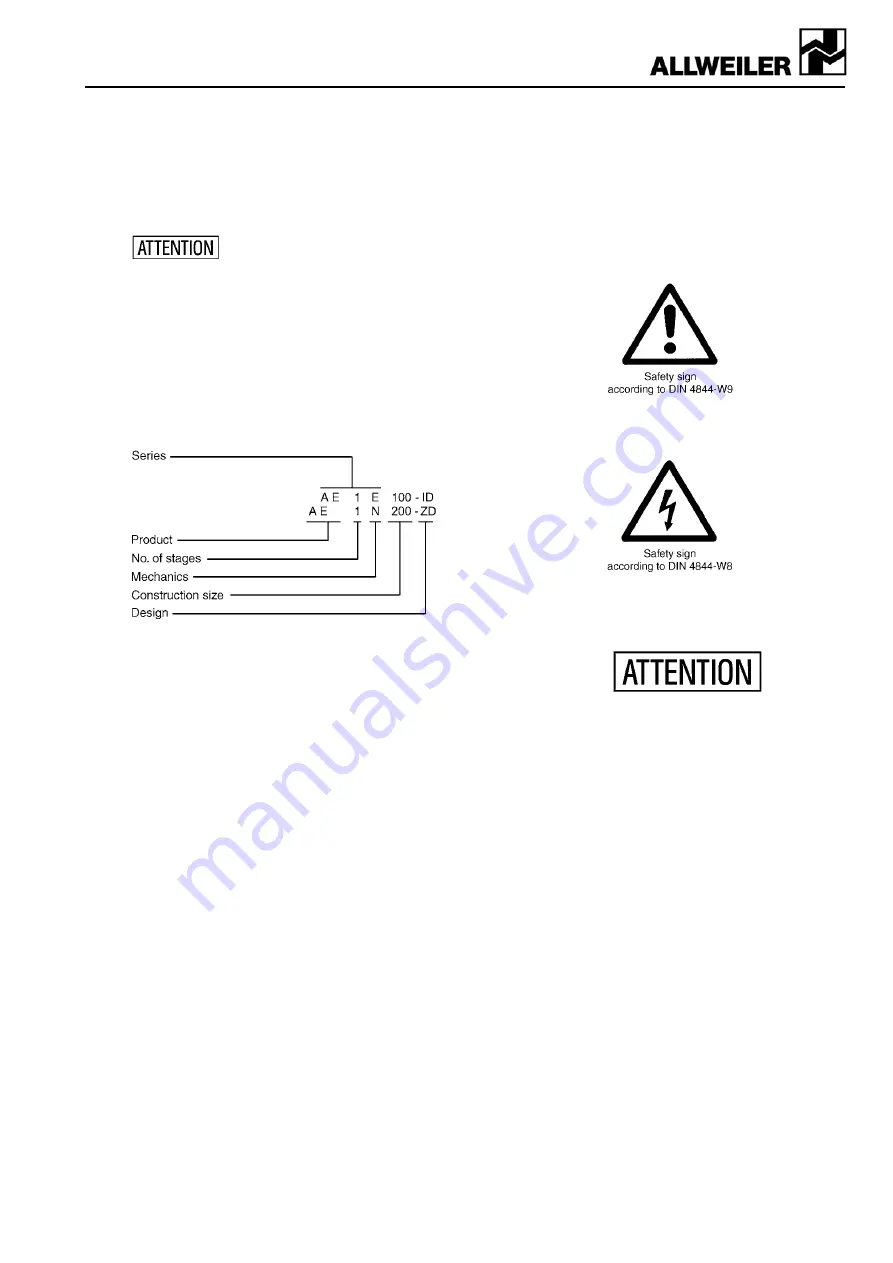
3
Series AE1L, AE.E, AE.N, AE.H, AE.V, AED1E, AED2N
Design ID, ZD
1.
General
1.1
Application and range of utilization
The eccentric screw pumps are self-priming, rotary
positive-displacement pumps for handling and dosing
low to high-viscosity, neutral or aggressive, pure or
abrasive, gaseous liquids or liquids which tend to
froth, even with fibre and solids contents.
The range of utilization is to be
taken from the order data sheet.
1.2 Performance
data
The exact performance data applying to the pump
are to be taken from the order data sheet and are
engraved on the name plate.
1.3 Abbreviation
The abbreviation of the eccentric screw pumps is set
up according to the following scheme:
Example:
This abbreviation is embossed on the type plate.
1.4 Warranty
Our liability for shortcomings in the supply is laid down
in our delivery conditions. No liability will be under-
taken for any damages caused by non-compliance
with the operating instructions and service conditions.
If at any later date the operating conditions happen to
change (e.g. different liquid pumped, speed, viscosity,
temperature or pressure conditions), it must be
checked by us from case to case and confirmed, if
necessary, whether the pump is suited for these pur-
poses. In case no special agreements were made,
pumps supplied by us may, during the warranty pe-
riod, be opened or varied only by us or our authorized
contractual service stations; otherwise, our liability for
any defects will cease.
1.5 Testing
Prior to leaving our factory, all pumps are subjected to
a leakage and performance test. Only properly oper-
ating pumps leave the factory achieving the perform-
ances assured by us. Thus, compliance with the fol-
lowing operating instructions ensures proper opera-
tion.
2.
Safety
These operating instructions contain basic hints to be
observed in case of installation, operation and main-
tenance. Therefore, prior to mounting and commis-
sioning, these operating instructions must by all
means be read by the fitter as well as the pertinent
expert personnel/customer and must always be avail-
able at the place of installation of the machine/ plant.
Not only are the general safety hints listed under this
main item „Safety“ to be observed, but also the spe-
cial safety hints such as for private use added to the
other main items.
2.1
Marking of hints in the operating instructions
The safety hints contained in these operating instruc-
tions which, in case of non-compliance, may cause
danger to personnel, are particularly marked with the
general danger symbol
in case of warning against electric voltage with
For safety hints, non-compliance with which may
cause dangers to the machine and its functions, the
word
is inserted.
Hints directly attached to the machine such as
!
directional marker
!
signs for fluid connections
must by all means be observed and maintained in
completely legible condition.
2.2
Personnel qualification and personnel training
The personnel for operation, maintenance, inspection
and mounting must have the corresponding qualifica-
tion for these operations. Range of liability, compe-
tence and the supervision of the personnel must be
exactly controlled by the customer. If the personnel do
not have the required knowledge, same must be
trained and instructed. If required, this may be ef-
fected by the manufacturer/ supplier on behalf of the
machine customer. In addition, it must be ensured by
the customer that the contents of the operating in-
structions are fully understood by the personnel.
2.3
Dangers in case of non-compliance with the safe-
ty hints
Non-compliance with the safety hints may result in
danger not only to persons, but also to environment
and machine. Non-compliance with the safety hints
may lead to the loss of any claims for damages. In
detail, non-compliance may,
for example
, entail the
following dangers: