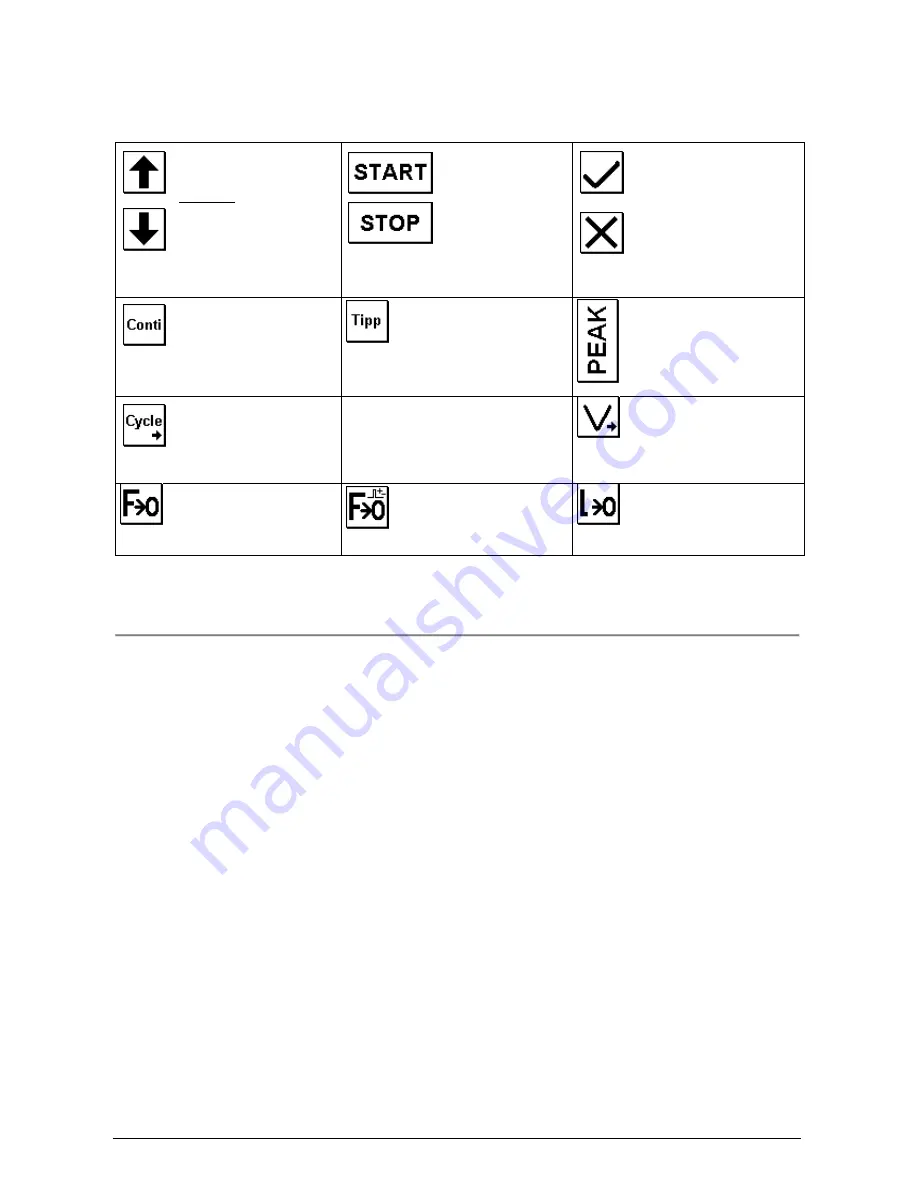
7
4.2.2. Handling arrows to control the test stand
Guide
To guide upwards or downwards
within the manual mode.
ATTENTION: The same arrows, at
the right boarder of the screen,
serve for the menu navigation.
Start
or
Stop
arrow
To initiate, abort or stopp
the test run within the
manual mode.
Acknowledgement key
By pressing this key you
acknowledge the indicated
process.
Abortion key
By pressing the abbortion key the
effection of the chosen process
gets distorted or aborted.
Conti-mode
Change from the Tipp to the
Conti mode
Tipp-mode
Change from the Conti to the Tipp
mode
Readout of the peak
values
By pressing the button the
currently in the force gauge saved
values of pressure and tensione
force values get indicated.
Next cycle
By pressing the next go of an
inspection process with various
cycles gets started.
Speed levels
Change between the 5 setted
speed levels within the manual
mode.
Zero setting force
Removing the measured force
value on 0
Cancel the paek values
Canceling the peak values within
the force gauge.
Zero setting path
Removing
the
measured
wegelinals on 0.
5.0 Mode of operation
5.1 Explanation of instrumentation
5.1.1 Force measurement
For the force measurement, high-precision measuring beam get used, their deflection during force
transmission gets recorded by a extension-measuring tape. The conversion of the analog signals into
digital form takes places within the load cell. The digital signals of the D/A – converter constitutes 1000
Hz., the transfer rate to the control unit 100 Hz.
The load cell gets imported and tared with every restart of the universal testing machine.
Contemporaerly a temperature compensation takes place. Fluctuation of temperature during the
operation of the test stand lead to errors of measurement (T
K
=0,02%K). If more intense changes of the
environmental conditions take place during a working day, it is recommendable to switch on and off
again the instrument to adjust the load cell to the compensation of the changed environmental
conditions.
The load cell should be checked at regular intervals. Accordant to DIN ISO 75000 a calibration is
necessary after 12 month, after repairation or after lager backfittings. A change of the load cell, if it has
been effected duly, does not demand a calibration or adjusting.
The calibration (adjusting) of the load cell is simple user effectable within the service- program (see
chapter 6.2.).