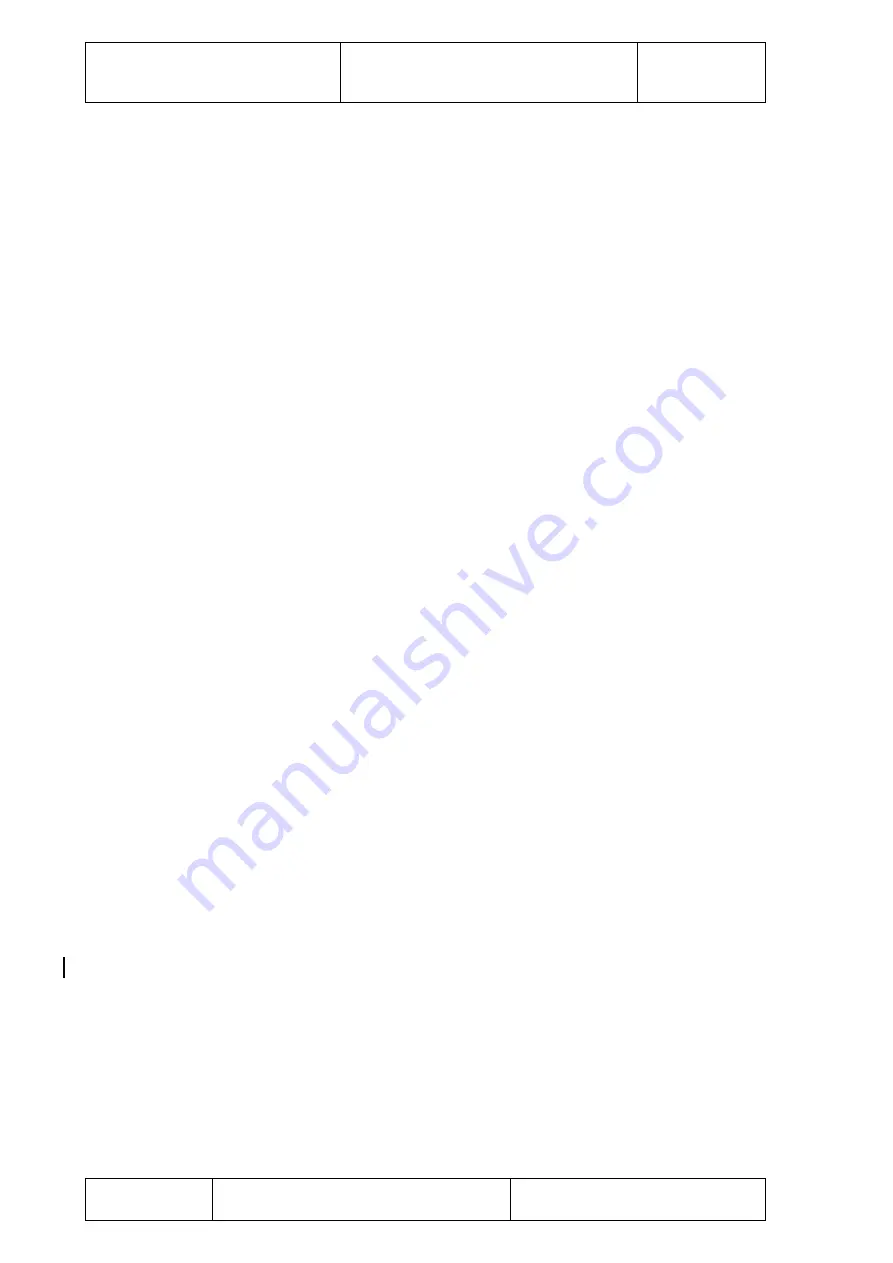
SECTION 17.
SAILPLANE REPAIRS
TECHNICAL SERVICE MANUAL
SZD-54-2
„Perkoz”
page 17.24
Allstar PZL Glider Sp. z o.o.
Doc No. 542.4.02
Issue II
April 2014
Revision No. 2
May 2017
corrected
17.6. Non-composite parts repair
17.6.1.
Metal parts repair
All damaged metal parts repairs are possible only with approval of authority
and after obtaining Type Certification Holder opinion.
Possible welding works could be made only by aviation welders at inert gas
shield. Before starting repairs, information about heat treatment of repaired element
should be absolutely obtained.
Damages to protective galvanic (anodizing, zinc plating) or paint coverings,
providing that damage has not caused a corrosion weakening material strength, can
be repaired by grinding to bare metal, degreasing, covering with protective prime
coat and outer enamel. There can be applied paint products used in aviation or for
repairing automotive paint damages, following the instructions specified by paint
products manufacturer.
17.6.2.
Rudder control system cables replacement
In rudder control system (ref. Fig. 2
‒11.) following cables are used:
1 - Cable (item 16)
2,5 mm
(0,098”), 7 x 7 acc. to PN-M-80235:1991, terminated
at both ends with a thimble C 3 (material PA6N) acc. to BN-78/3813-45.
2 - Cables (items 17, 18, 19)
3,2 mm
(0.0126”), 7 x 19 acc. to PN-M-80235:1991,
terminated at both ends with a thimble C 3,5 (material PA6N) acc. to
BN-78/3813-45.
Nominal cable tensile breaking force:
- for cable
2,5 mm
1124 lbf
- for cable
3,2 mm
1686 lbf
In case of cable replacement, it should be first tensed with force being equal to
0,5 to 0,6 of nominal tensile breaking force in time of minimum 3 minutes. Thimbles
are to be fixed to cable by plaiting or clamping. When thimbles are to be clamped,
only tools with authority permit may be used in the process. Sequence of actions
‒
threading and clamping
‒ comes from rudder control system design (ref. Fig. 2‒11.).
In case of using bushing in accordance with ZN-73/L-383320 clamping should
be done on whole length of bushing, diameter w/o fin should be: for 2,5 mm cable
–
0,22+0,01
”, and for 3,2 mm cable ‒ 0,27+0,01”.
2