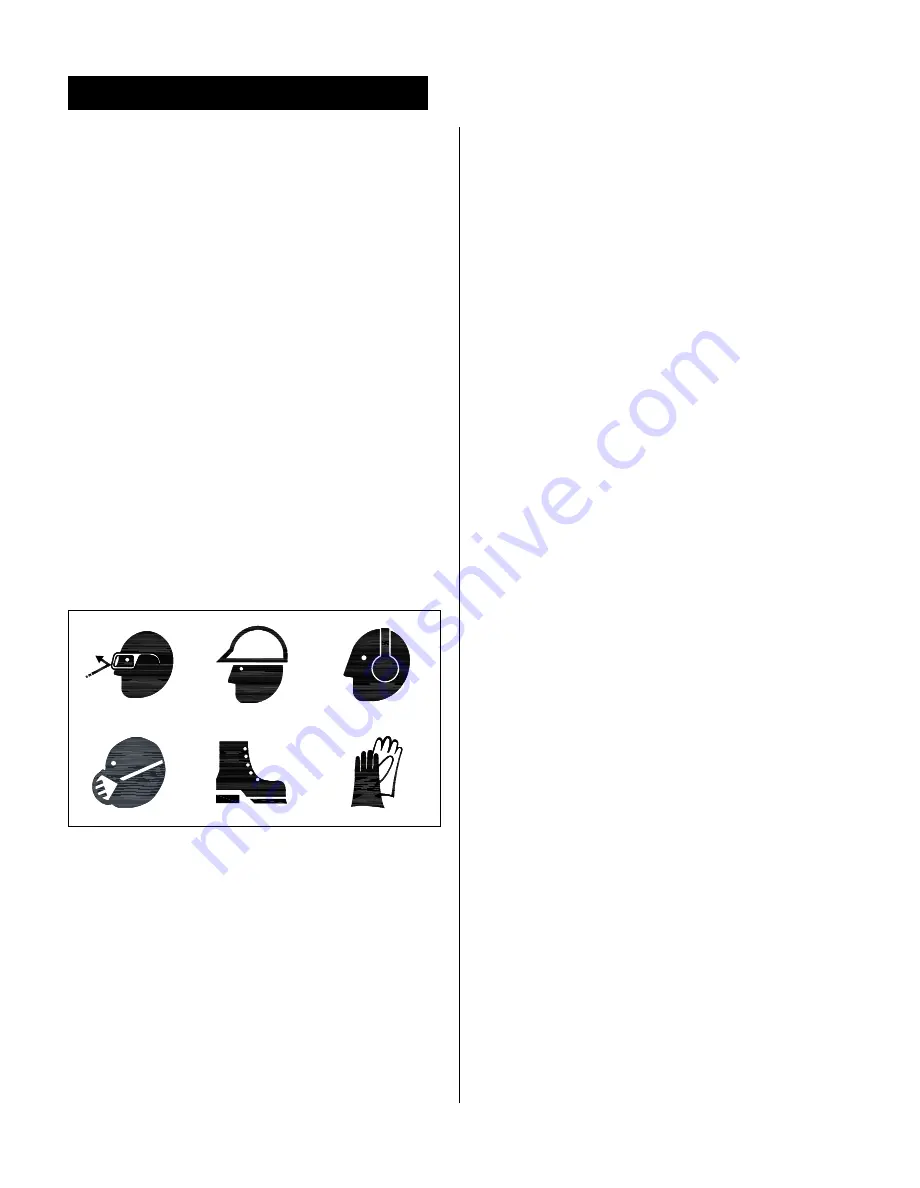
Allied Construction Products, LLC www.alliedcp.com
TM576981_HP700B_18feb
vii
Safety Information – [cont’d]
Operational Safety Program
The safe and efficient use of the Allied equipment
depends upon proper installation, operation,
maintenance and repair. Operational safety programs
must encompass all of these elements.
Accident prevention through operational safety
programs are most effective when the equipment
owner further develops the program by taking into
account his own experience in using and maintaining
equipment.
Developing such programs will help minimize
equipment downtime, while maximizing service life
and performance. Most importantly, it will minimize
the risk of personal injuries.
Personal Protective Equipment (PPE)
Personal protection equipment (PPE) must be
available to any personnel operating or nearby the
equipment that may be exposed to hazards such as
falling, flying and splashing objects, or harmful dusts,
fumes, mists, vapors, or gases. Approved PPE, when
used correctly, helps protect against certain harmful
effects from exposure with the identified hazard.
Examples of PPE include safety eyewear, safety hat,
hearing protection, dust mask, safety footwear, and
gloves. (Shown Pictograms of PPE is not all-
inclusive).
Those responsible for administering PPE shall train
personnel with the proper selection and use of PPE
to protect against misuse.
Safety Guards and Protective Barriers
A safety guard is a physical barrier designed to
prevent access to danger areas. Guards are fitted to
the Allied equipment to protect against unsafe
situations that could not be eliminated through design
measures. Guards are only effective when properly
installed and in place. Guards shall not be removed
unless for the purpose of inspection and service of
components. Reinstall all guards after service or
adjustments are completed.
Where it was not possible to prevent an unsafe
situation by means of a guard, safety messages
appear on the equipment, warning personnel of a
recognized hazard.
Additional guarding, not included with the Allied
equipment, is necessary at the operator’s station to
protect the operator and other nearby personnel
against flying debris from material being cut or
demolished. Do not handle, demolish or cut material
overhead without proper guards installed.
The control switch shall be located in a protected
area that is guarded against accidental operation of
the Allied work tool.
Unapproved Use or Modifications
In order to provide and maintain efficient operation
with reliable service, while ensuring operator safety,
the Allied equipment may not be used for any
purpose other than, for which it was intended. Use of
the Allied equipment, other than those cited in this
manual, may place personnel at risk of injury and/or
may subject the equipment to damage.
When making repairs, use only the manufacturer's
genuine parts. Substitute parts may not meet the
required standards for fit and quality, or may impair
function, safety and performance. The Allied
equipment shall not be modified or used in
unapproved applications unless written consent is
received from the Allied Engineering Department.