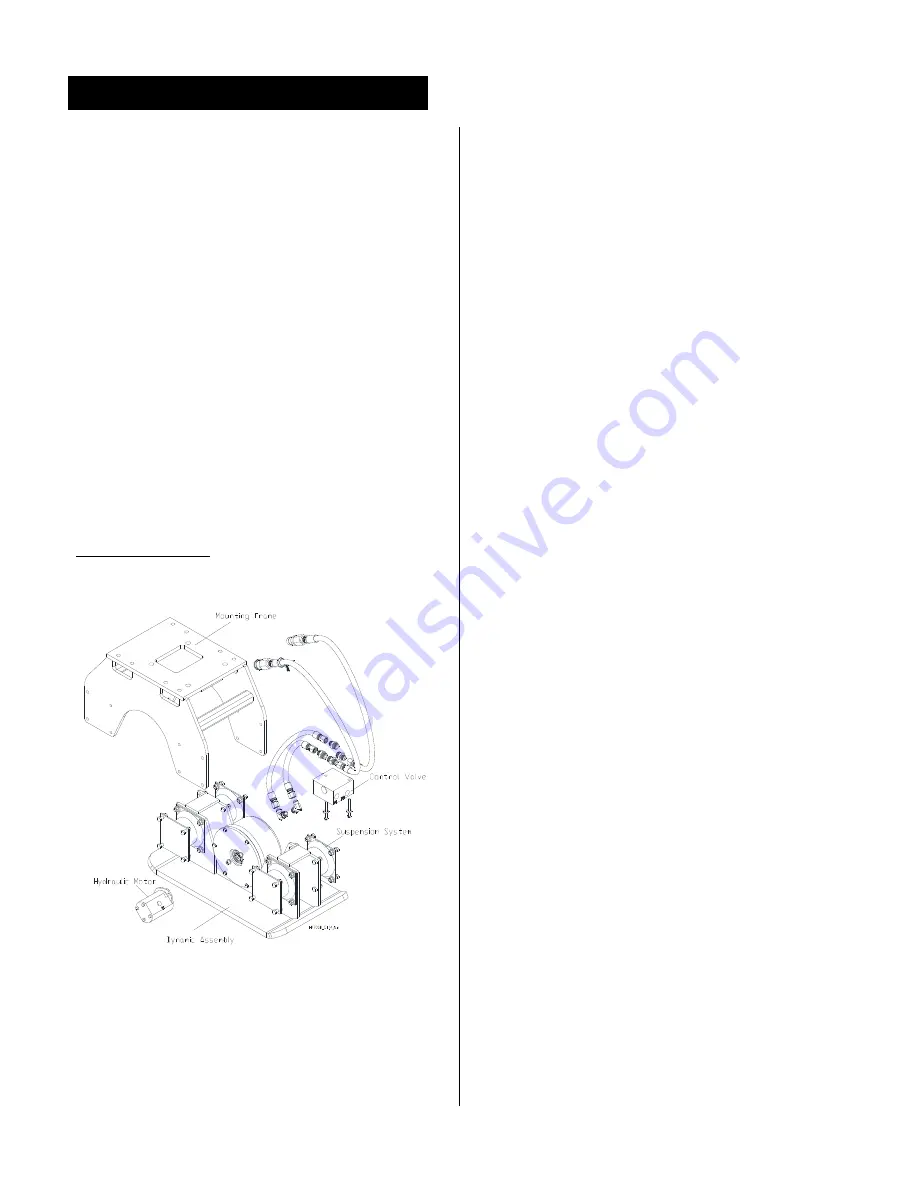
Allied Construction Products, LLC www.alliedcp.com
TM576981_HP700B_18feb
5
4.0 Product Information
4.1 Description and Application - Typical
The Allied Ho-Pac is a boom-mounted, hydraulic
powered, vibratory plate compactor and driver. It is
used for soil compaction and sheet/pile installation.
The Ho-Pac is designed for mounting on mobile
equipment with hydraulic booms, such as rubber tired
or track-type construction vehicles and is attached to
the carrier in the same manner as mounting a bucket.
The Ho-Pac operates off the host machine's hydraulic
system and reaches out to work anywhere the
machine's boom can reach.
Applications include backfill compaction, base course
preparation, finish surface treatment and
embankment buildup.
The Ho-Pac can also be an effective sheet or pile
driver. Vibration energy is transferred through the
sheet or pile to the soil. Soils with 50% or more
granular content are “liquefied” by the vibration,
which breaks the skin friction, allowing the sheet or
pile to penetrate more easily. Refer to the
Compaction Manual for further details.
4.2 Familiarization of Ho-Pac Components
Fig. 4-1 Main Components and Subassemblies
Major subassemblies of the Ho-Pac include:
Mounting Frame
– The Mounting Frame serves as
the connection point used to attach the Ho-Pac to the
stick / linkage of the carrier.
Suspension System
– Rubber Spring Mounts
suspend the Dynamic Assembly from the Mounting
Frame. They isolate the vibratory energy from
transferring to the carrier and operator.
Dynamic Assembly
- Generates and transfers the
vibratory energy to the soil. The assembly includes
the hydraulic motor, bearings, eccentric mass,
housing and compaction plate.
Control Valve
– All Ho-Pac models come standard
with the multi-function control valve. Benefits include
optimized operation with improved reliability of critical
components such as the motor and bearings.
NOTE
:
The valve is factory pre-set and requires no
further adjustments.
The control valve performs the following functions:
x
Flow regulator
- Prevents over-speeding the
hydraulic motor.
x
Pressure control
– Protects the motor and other
hydraulic components from over-pressure. This is
factory pre-set at the maximum operating
pressure plus 200 psi (14 bar).
x
Anti-cavitation circuit
- Controls deceleration of
the hydraulic motor and eccentric mass. Also
protects motor from damage on circuits not set
up with an open return.
x
Return line check valve
- Prevents reverse flow
to the hydraulic motor. Also provides a nominal
back-pressure to ensure the proper operation of
auxiliary valves, such as Allied’s AC40 and AC75
priority flow control valves.
4.3 Principle of Operation
The vibratory action is generated by the eccentric
movement of the out of balance weight, driven by the
hydraulic motor turning at a high rpm.