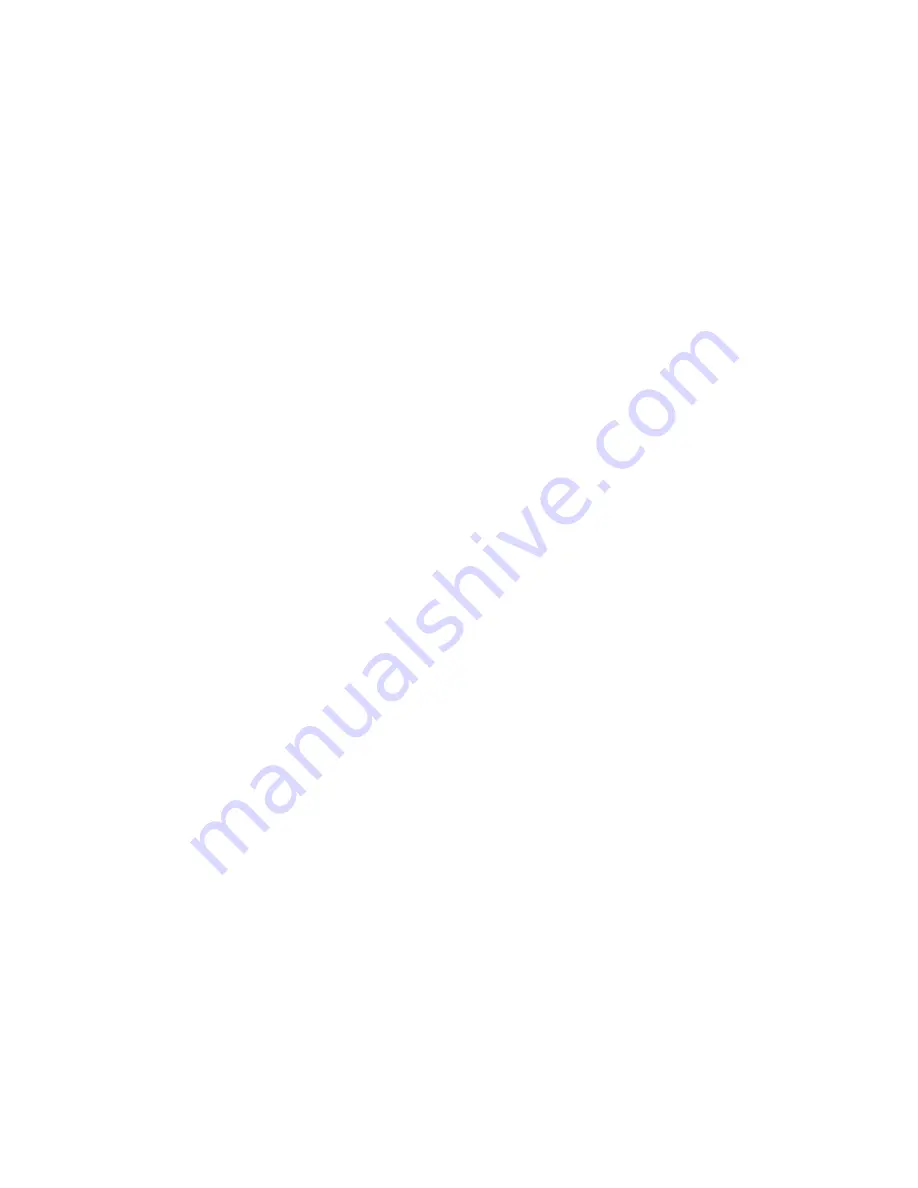
M412982
1
© Copyright 2002, Alliance Laundry Systems LLC
All rights reserved. No part of the contents of this book may be reproduced or transmitted in any form or by any means without
the expressed written consent of the publisher.
© Copyright, Alliance Laundry Systems LLC – DO NOT COPY or TRANSMIT
(continued)
Table of Contents
Section 1 – Safety Information
Locating An Authorized Service Person .................4
Model Identification ................................................5
Customer Service ....................................................6
Serial Plate Location ...............................................6
Safety Warnings and Decals ...................................7
Safety Precautions for Servicing Tumblers ............7
1. Motor Does Not Start .......................................9
2. Motor Overload Protector Cycles Repeatedly ...
3. Motor Runs But Cylinder Does Not Turn. .....10
4. Motor Does Not Stop .....................................10
5. Gas Burner Does Not Ignite ...........................11
6. Burner Ignites And Goes Out Repeatedly .....12
7. Burner Shuts off Prematurely ........................12
8. Burner Repeatedly Cycles Off On High
Limit Thermostat ............................................13
9. Steam Valve or Burner Does Not Shut-off ...13
10. Clothes Do Not Dry .......................................14
11. Tumbler Overheating .....................................14
12. Burners Not Burning Properly - Gas Models 15
13. Loading Door Opens During Operation ........15
14. Tumbler Runs But No Steam To Coils
- Steam Models ..............................................15
15. Water In Steam Line - Steam Models ............16
16. Tumbler Will Not Start, Time On Drying
Timer, Door Closed ........................................17
17. Motor Runs But Will Not Heat ......................18
18. Cylinder Turns, But Will Not Heat ................19
19. Grounding Instructions ..................................21
Section 5 – Service Procedures
20. Access Panel/Control Box .............................23
21. Loading Door Assembly ................................23
22. Loading Door Hinge Brackets .......................23
23. Loading Door Hinges .....................................24
24. Loading Door Handle ....................................24
25. Front Panel .....................................................25
26. Loading Door Switch .....................................26
27. Push-to-start Switch .......................................26
28. Cooling And Drying Run Lights ...................26
29. Relay ..............................................................26
30. Cooling and Drying Timers ...........................27
31. Reversing/Nonreversing Switch ....................28
32. Control Thermostat ........................................28
33. Micro control .................................................29
34. Emergency Stop Button - DC, JC and SC
Models ............................................................31
35. Ignition Reset Switch - DC, JC and SC
Gas Models ....................................................31
36. Fuse Holder ....................................................31
37. Signal Buzzer .................................................31
38. Gas Valve .......................................................33
39. Igniter .............................................................33
40. Ignition Control ..............................................33
41. Burner Tube ...................................................33
42. Stove High Limit Thermostat ........................34
43. Cabinet High Limit Thermostat/ Load Ready
Thermostat .....................................................34
44. Steam Coils ....................................................35
45. Airflow Switch ...............................................35
46. Drive Guard Cover .........................................36
47. Cylinder Belt ..................................................37
48. Drive Belt .......................................................38
49. Step Pulley Assembly ....................................38
50. Cylinder Sheave .............................................38
51. Motor Pulley ..................................................39
52. Jackshaft Assembly ........................................39
53. Cylinder Assembly ........................................39
54. Trunnion Bearings .........................................40
55. Fan Motor And Fan Assembly .......................41
56. Fan .................................................................41
57. Trunnion Shaft Assembly ..............................42
58. Cylinder Drive Motor ....................................43
59. Reversing Timer ............................................44
60. Reversing Contactor ......................................44
61. Fan Motor Contactor ......................................44
62. Transformer ...................................................44