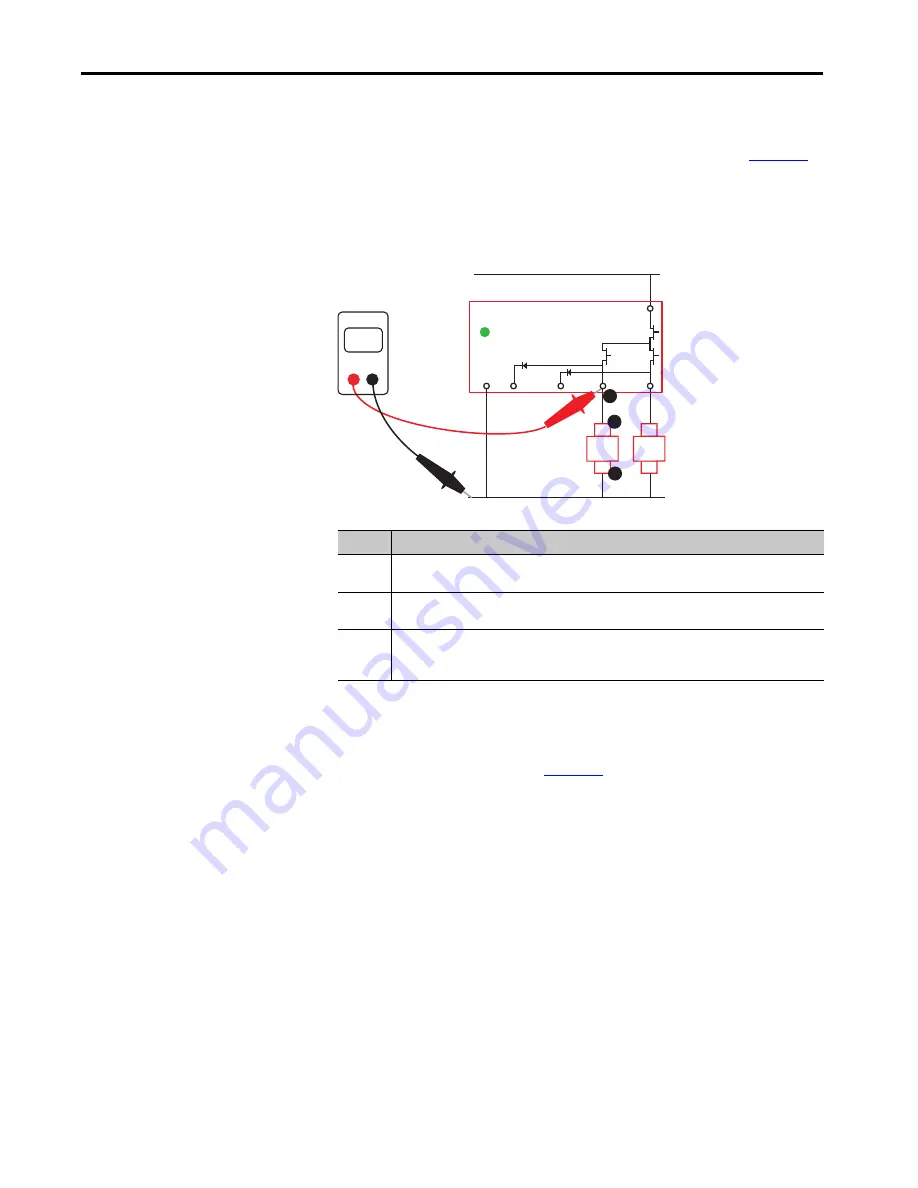
80
Rockwell Automation Publication 440R-UM013E-EN-P - March 2017
Chapter 11
Troubleshooting
Check the OSSD Connections
Confirm that voltage is present at the relay terminals and the load.
shows an example of the measurement points for one output channel (terminal
14). Since most safety circuits consist of two channels, repeat the checking on
the second channel (terminal 24).
Figure 77 - OSSD Output Connections
Check the PowerFlex Drive Connections
Confirm that voltage is present at the relay terminals and the safety input
terminals of the PowerFlex drive.
measurement points for one output channel (terminal 34). Repeat the
checking on the second channel (terminal 44). The terminal connections from
34 and 44 to S1 and S2 can be reversed.
Step
Description
1
The voltage at 14 must be slightly less than the supply voltage. If not, then the DIS relay must be
replaced.
2
The voltage at A1 must be slightly less than the supply voltage and must be the same voltage as
measured at terminal 14. If not, check for an open circuit (broken wire) between terminal 14 and A1.
3
The voltage at A2 must be zero. If not, check for an open circuit between A1 and the voltage supply
ground connection. If A2 measures zero volts and A1 measures the supply voltage, then K1 is not
operating properly, and must be replaced.
34
44
14
24
A1
A2
24V DC supply
24V common
23
Volts
DMM
1
OUT
K1
A2
A1
K2
A2
A1
2
3
Summary of Contents for Guardmaster
Page 12: ...12 Rockwell Automation Publication440R UM013E EN P March 2017 Chapter 1 Overview Notes...
Page 16: ...16 Rockwell Automation Publication440R UM013E EN P March 2017 Chapter 2 Installation Notes...
Page 40: ...40 Rockwell Automation Publication440R UM013E EN P March 2017 Chapter 4 Configuration Notes...
Page 99: ......