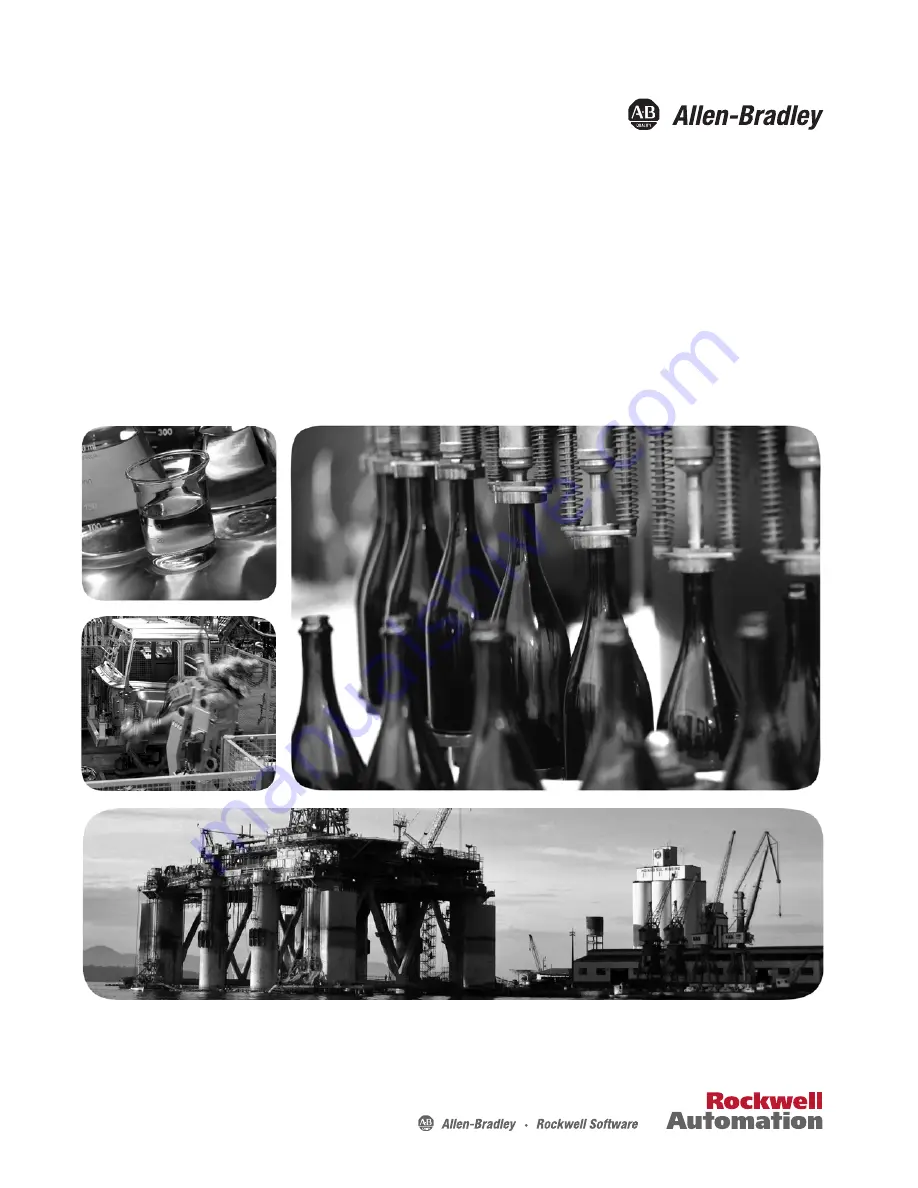
GuardLogix 5580 and Compact GuardLogix 5380
Controller Systems
Catalog Numbers 1756-L81ES, 1756-L82ES, 1756-L83ES, 1756-L84ES, 1756-L8SP, 1756-L81ESK, 1756-L82ESK,
1756-L83ESK, 1756-L84ESK, 1756-L8SPK, 5069-L306ERMS2, 5069-L306ERS2, 5069-L310ERMS2, 5069-L310ERS2,
5069-L320ERMS2, 5069-L320ERS2, 5069-L320ERS2K, 5069-L320ERMS2K, 5069-L330ERMS2, 5069-L330ERS2,
5069-L330ERS2K, 5069-L330ERMS2K, 5069-L340ERMS2, 5069-L340ERS2, 5069-L350ERMS2, 5069-L350ERS2,
5069-L350ERS2K, 5069-L350ERMS2K, 5069-L380ERMS2, 5069-L380ERS2, 5069-L3100ERMS2, 5069-L3100ERS2
Safety Reference Manual
Original Instructions
Summary of Contents for Compact GuardLogix 5380
Page 88: ...88 Rockwell Automation Publication 1756 RM012B EN P April 2018 Appendix C Reaction Times Notes...
Page 108: ...108 Rockwell Automation Publication 1756 RM012B EN P April 2018 Glossary Notes...
Page 114: ...114 Rockwell Automation Publication 1756 RM012B EN P April 2018 Index...
Page 115: ......