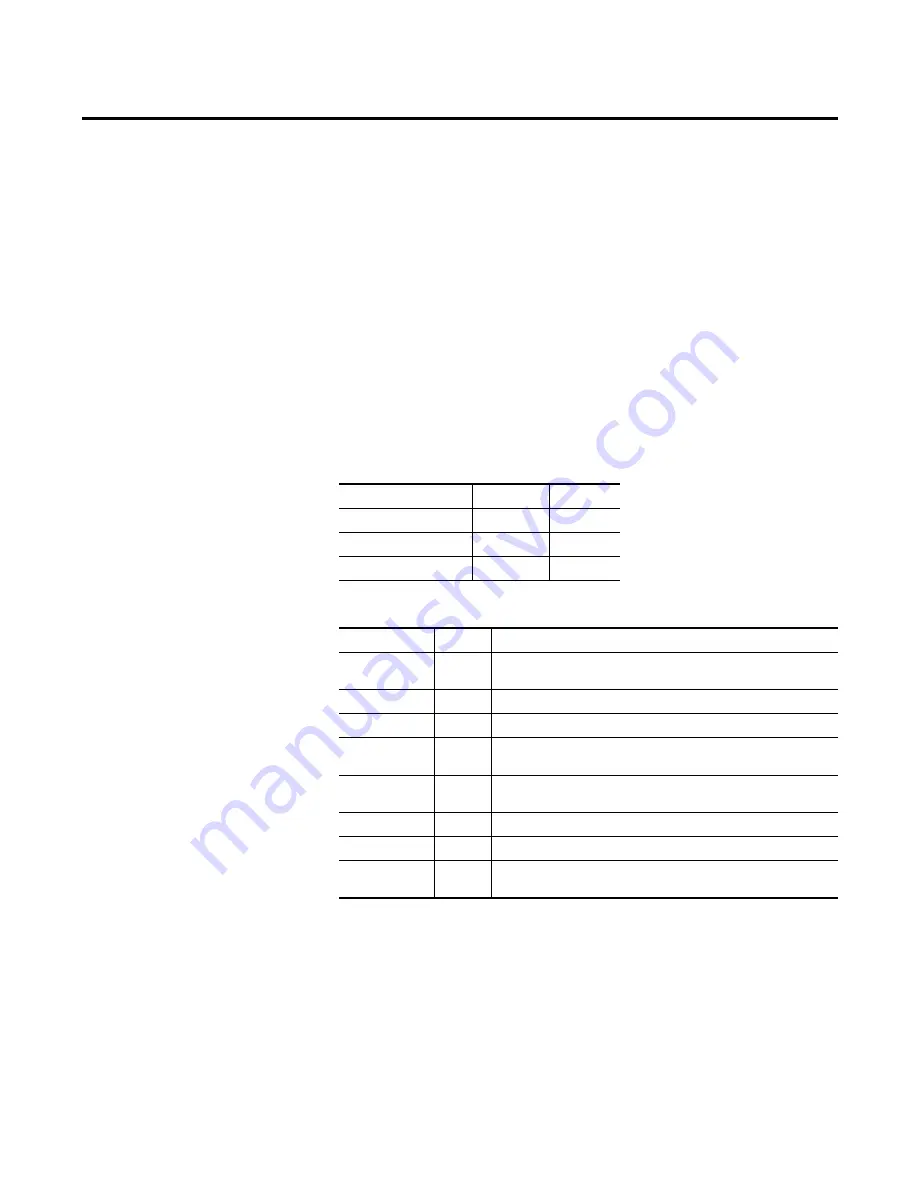
Rockwell Automation Publication 1734-UM007E-EN-P - October 2015
21
Chapter
3
Communicate with Your Module
About This Chapter
Read this chapter for information about how the 1734-SSI module transmits SSI
sensor data over the DeviceNet network.
About Communications
Data can be exchanged with the master through a polled, cyclic, or change-of-
state connection. Bit-strobe Command Response Messaging and the
Unconnected Message Manager (UCMM) are not supported.
(1)
The module produces and consumes data as follows:
See the following tables for consume and produced bit and byte definitions.
(1) If you are not familiar with these terms, see the DeviceNet Specification for definitions (online: www.odva.org).
I/O Connection Type
Consumes
Produces
Polled
2 bytes
10 bytes
Cyclic
2 bytes
10 bytes
Change-of-state
2 bytes
10 bytes
Byte
Bit
Description
Produce 0
0...7
Low byte of present low SSI word. Bit 0 is the least significant bit of the entire
present SSI word.
Produce 1
0...7
High byte of present low SSI word.
Produce 2
0...7
Low byte of present high SSI word.
Produce 3
0...7
High byte of present high SSI word. Bit 7 is the most significant bit of the entire
present SSI word.
Produce 4
0...7
Low byte of latched low SSI word. Bit 0 is the least significant bit of the entire
latched SSI word.
Produce 5
0...7
High byte of latched low SSI word.
Produce 6
0...7
Low byte of latched high SSI word.
Produce 7
0...7
High byte of latched high SSI word. Bit 7 is the most significant bit of the entire
latched SSI word.