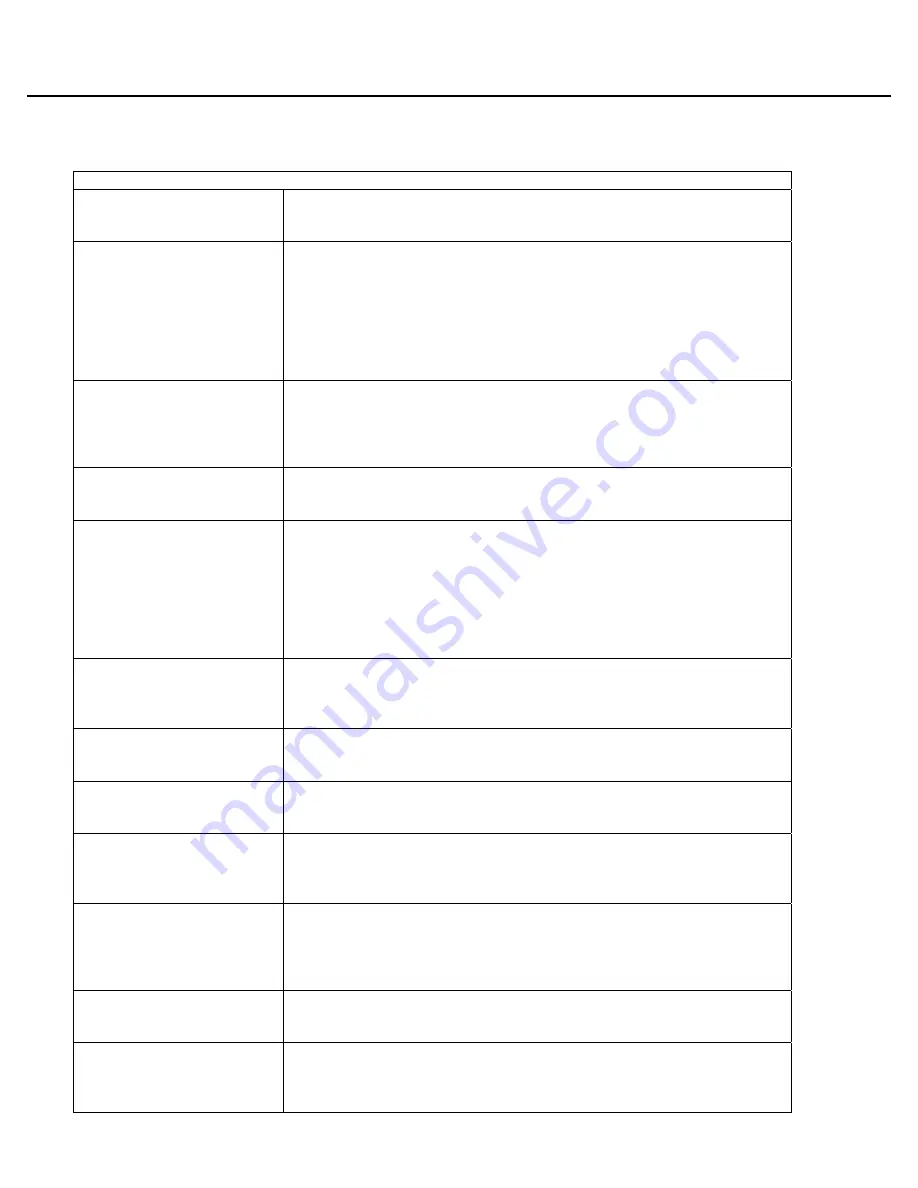
Maintenance
Algas-SDI Operation and Maintenance Manual – P/N – 54000
16
Table 4
– Annual Maintenance Requirements
Annual Maintenance Items
Strainer
Remove the plug and clean the screen. Replace screen if tears or holes
are present. If oils or contaminants are present, it may be necessary to
use a cleaner to remove all of the contaminants.
Thermostat
Check thermostat for proper operation per the
Start-up procedure
.
Establish pilot and turn the thermostat dial counter-clockwise to high,
burners should cycle on. Turn the dial clockwise to the “off” position,
main burner and pilot should both extinguish in a short period of time.
Replace the thermostat if not operating properly (thermostat cannot be
serviced). NOTE: Before replacing the thermostat, be sure the
thermocouple is delivering the proper voltage to the thermostat (see
below).
Thermocouple
Check electrical output of the thermocouple with a millivolt meter. The
thermocouple output (when hot) should be 13 - 30 mV. Lower than 13
mV reading indicates the thermocouple should be replaced. NOTE: Be
careful not to over tighten the thermocouple! First hand tighten and then
turn 1/8
th
turn with wrench.
Pilot Assembly
Inspect pilot flame to ensure flame is enveloping 3/8” to ½” of the
thermocouple tip. Clean pilot orifice. If pilot assembly is corroded or
significantly deteriorated, replace complete pilot assembly.
Main Burner Assembly
Inspect burner tips to ensure each tip has proper flame. For easy access
to clean the burner tips, disconnect burner supply line and remove the
burner from the unit. With compressed air (if possible), blow out main
burner ring prior to cleaning the burner tips. Check orifices and air supply
openings for debris, insects and/or dirt. Clean any plugged or obstructed
orifices. Direct Fired vaporizers built after October 2002 have #66 burner
jet orifices. Vaporizers built after October 2013 have #69 burner jet
orifices.
Flame Spreader Bar
Models 80/40H & 120/60H
Upon initial installation and during periodic maintenance inspections,
check flame spreader bar position to ensure both burners light
simultaneously and smoothly. Straighten spreader bar if it is positioned at
an angle or not positioned on top of the pilot properly.
Liquid Inlet Valve
Use repair kit p/n: 3-0016 to replace internal components of the liquid inlet
valve. See detailed
Liquid Inlet Valve Maintenance Instructions
for further
information.
Capacity Control Valve
Use repair kit p/n: 3-0017 to replace internal components of the capacity
control valve. See detailed
Capacity Control Valve Maintenance
Instructions
for further information.
Vaporizer Tubing
Inspect all tubing for pitting or flaking - run hands along the underside of
each of the tubes to check for signs of corrosion. Replace tubes if
corroded. Disconnect all tubing and blow tubes free of debris. Re-install
tubing to the vaporizer and check and tighten all fittings.
Relief Valves
Inspect all relief valves on the vaporizer, liquid and vapor lines for signs of
corrosion and rain caps. Replace rain cap if it is damaged or missing.
Replace relief valves per manufacturer’s recommended replacement
period. Also replace relief valve if it shows significant corrosion on the
outlet or has relieved.
Burner Regulator
Check regulator delivery pressure at the drip leg and at the burner
pressure port to ensure proper pressure is delivered to the thermostat and
burners. See page 3.
Heat Exchanger
1. Check heat exchanger flue for holes or excessive scale.
2. Remove debris, soot build-up and any obstructions from the
outside surface of the heat exchanger between the fins and in the
area between the heat exchanger and flue. High pressure air or
Summary of Contents for Direct Fired F6-ASME
Page 4: ...This page left intentionally blank...
Page 7: ......
Page 10: ...This page left intentionally blank...
Page 42: ...APPENDIX A TECHNICAL INFORMATION...
Page 43: ...Appendix A This page intentionally left blank...
Page 50: ...Appendix A...
Page 51: ...Appendix A...