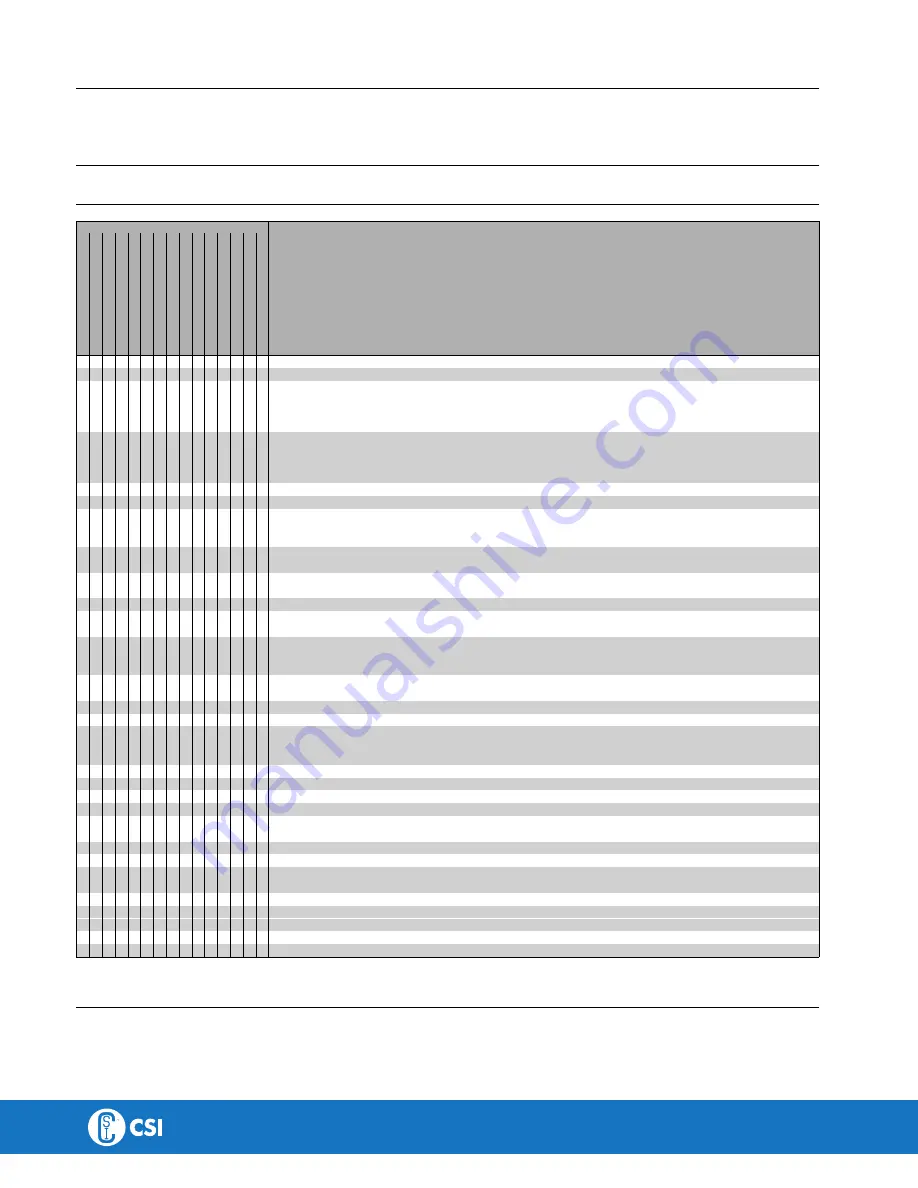
5 Maintenance
Take care not to damage shaft surfaces, in particular where bearings and lipseals will be located
Ensure all fastenings are tightened to the torque settings as shown in Technical Data (See chapter 6 Technical data)
5.11 Trouble shooting
P
Prroobblleem
m
No flo
w
Under capacity
Irr
egular di
scharge
Lo
w
di
scharge pr
ess
ure
Pump
w
ill not prime
Prime lo
st after
starting
Pump
stall
s
w
hen
starting
Pump overheat
s
Motor overheat
s
E
xce
ss
ive po
w
er ab
sorbed
Noi
se and vibration
Pump element
w
ear
S
yphoning
S
eizur
e
Mechanical
seal lea
kage
P
Prroobbaabbllee C
Caauusseess
S
Soolluuttiioonnss
√√
√√
Incorrect direction of rotation.
Reverse motor.
√√
Pump not primed.
Expel gas from suction line and pumping chamber and introduce fluid.
Increase suction line diameter.
Increase suction head.
Simplify suction line configuration and reduce length.
√√ √√ √√ √√ √√
√√
Insufficient NPSH available.
Reduce pump speed.
Increase suction line diameter.
Increase suction head.
Simplify suction line configuration and reduce length.
√√ √√ √√ √√
√√
Fluid vaporising in suction line.
Reduce pump speed.
√√ √√ √√ √√ √√
√√
Air entering suction line.
Remake pipework joints.
√√ √√ √√ √√ √√
√√
Strainer or filter blocked.
Service fittings.
Increase fluid temperature.
Decrease pump speed.
√√
√√ √√ √√ √√ √√ √√
Fluid viscosity above rated figure.
Check seal face viscosity limitations.
Decrease fluid temperature.
√√ √√ √√
Fluid viscosity below rated figure.
Increase pump speed.
Reduce fluid temperature.
√√
√√ √√
√√
Fluid temp. above rated figure.
Check seal face and elastomer temp. limitations.
√√ √√ √√
Fluid temp. below rated figure.
Increase fluid temperature.
Clean the system.
√√ √√ √√ √√
Unexpected solids in fluid.
Fit strainer to suction line.
Check for obstructions i.e. closed valve.
Service system and change to prevent problem recurring.
√√ √√ √√
√√ √√ √√ √√ √√ √√ √√ √√ √√
Discharge pressure above rated figure
Simplify discharge line to decrease pressure.
Increase flush flow rate.
√√
Seal flushing inadequate.
Check that flush fluid flows freely into seal area.
√√
√√ √√ √√
Pump speed above rated figure.
Decrease pump speed.
√√ √√
Pump speed below rated figure.
Increase pump speed.
Check alignment of pipes.
Fit flexible pipes or expansion fittings.
√√
√√ √√ √√ √√ √√ √√
Pump casing strained by pipework.
Support pipework.
√√
√√ √√ √√
Flexible coupling misaligned.
Check alignment and adjust mountings accordingly.
√√ √√ √√ √√ √√ √√
Insecure pump driver mountings.
Fit lock washers to slack fasteners and re-tighten.
√√ √√ √√ √√ √√ √√ √√
Shaft bearing wear or failure.
Refer to pump maker for advice and replacement parts.
√√ √√ √√ √√ √√ √√
Insufficient gearcase lubrication.
Refer to pump maker’s instructions.
Check rated and duty pressures.
√√ √√
√√ √√ √√ √√ √√ √√
Metal to metal contact of pumping element.
Refer to pump maker.
√√ √√ √√
Worn pumping element.
Fit new components.
√√
√√
Suction lift too high.
Lower pump or raise liquid level.
Fluid pumped not compatible with
√√
materials used.
Use optional materials.
√√
No barrier in system to prevent flow passing.
Ensure discharge pipework higher than suction tank.
√√
Pump allowed to run dry.
Ensure system operation prevents this.
Fit single or double flushed mechanical seals.
√√ √√
Faulty motor.
Check and replace motor bearings.
√√
Pumping element missing
Fit pumping element.
51
CONTACT CSI FOR MORE INFORMATION | CSIDESIGNS.COM | [email protected] | 417.831.1411