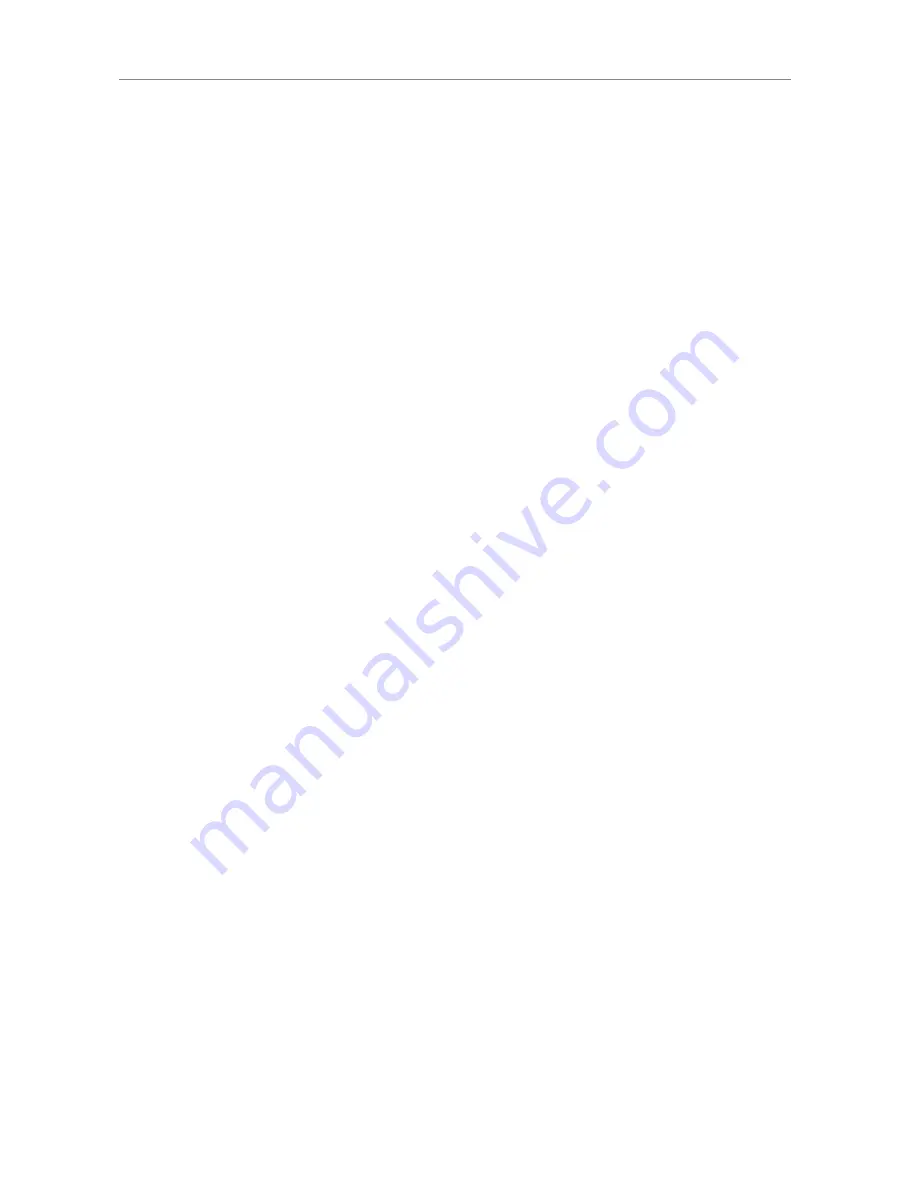
8
2 USER INSTRUCTIONS
2.1 Introduction
Following the completion of installation and commissioning, the authorized dealer and service technician will
inform you about the use and maintenance of the boiler. You may ask any question of them to understand the
boiler further and they will be pleased to help.
Read this booklet carefully before using the boiler and follow the safety instructions and warnings while using
the boiler. This will provide long-term, safe and most economic use of your boiler.
In this section, additional technical and information is given to introduce the boiler.
2.2 Course Of Action In Case Of Gas Leakage
If you smell gas or the gas alarm device signals;
Be calm,
Turn off the appliance,
Open all the doors and windows to vent the room,
Extinguish any
fl
ame,
Close gas valves of any appliance and at the apartment inlet,
Do not light anything and do not smoke,
Do not switch on or off and electrical device,
Do not attach or pull out electric plugs, do not ring the bell,
Do not use the telephone where the gas smell exists,
Contact your gas supplier and
fi
re brigade and explain the situation.
2.3 Warnings!
This appliance must only be used for the intended purpose of manufacture.
Alarko Carrier Sanayi ve Ticaret A.
Ş
. does not take any responsibility for the damage or injury on persons,
animals or objects caused by incorrect installation, service or maintenance, use except for the intended pur-
pose or disobeying any of the warnings within this booklet.
Spaces allowed for installing a gas-
fi
red boiler are de
fi
ned by international and/or local regulations and rules
of gas distribution companies. You can supply detailed information about those limitations from your installer.
For your own safety, do not ask the installer to install your boiler to prohibited spaces.
Before gas installation, a suitable gas installation project has to be prepared and approved according to the
requirements of local gas distribution organization. After approval of local gas distribution organization and
precise application of installation, have your boiler commissioned by an Authorized Service.
Commissioning is a free service.
Do not let unauthorized people to interfere or service the boiler.
Gas conversion process, if necessary, must be made by an authorized service only.
Conversion is paid by the end-user.
Keep
fl
ammable and combustible objects, either liquid or solid, away from the boiler.
Do not place cooker near the appliance and protect the boiler from direct vapour.
Do not use any spray, chemical solvent, chlorinated cleaner, paint or adhesive near the boiler.
The boiler is to be connected to an earthed 230 V 50 Hz electric supply.
To enable the frost protection function in winter when the weather temperature might fall below 0°C, do not turn the boiler off.
Filter must be installed at the water inlet of the boiler to protect the pump and the
fi
lter must be cleaned pe-
riodically. The pump shaft should be rotated manually before starting the boiler after a long time of inactivity.
Apply the authorized service to take more information about this process.
If you charge the central heating system with hard water, this may cause blockage of the heat exchanger.
Mains supply water should not exceed 17,5° French hardness value.
Hot water circuit does not need a pressure relief valve. On the other hand, pressure should not exceed 6
bars. In case of doubt, a pressure regulator should be
fi
tted. Consult your installer on this issue.