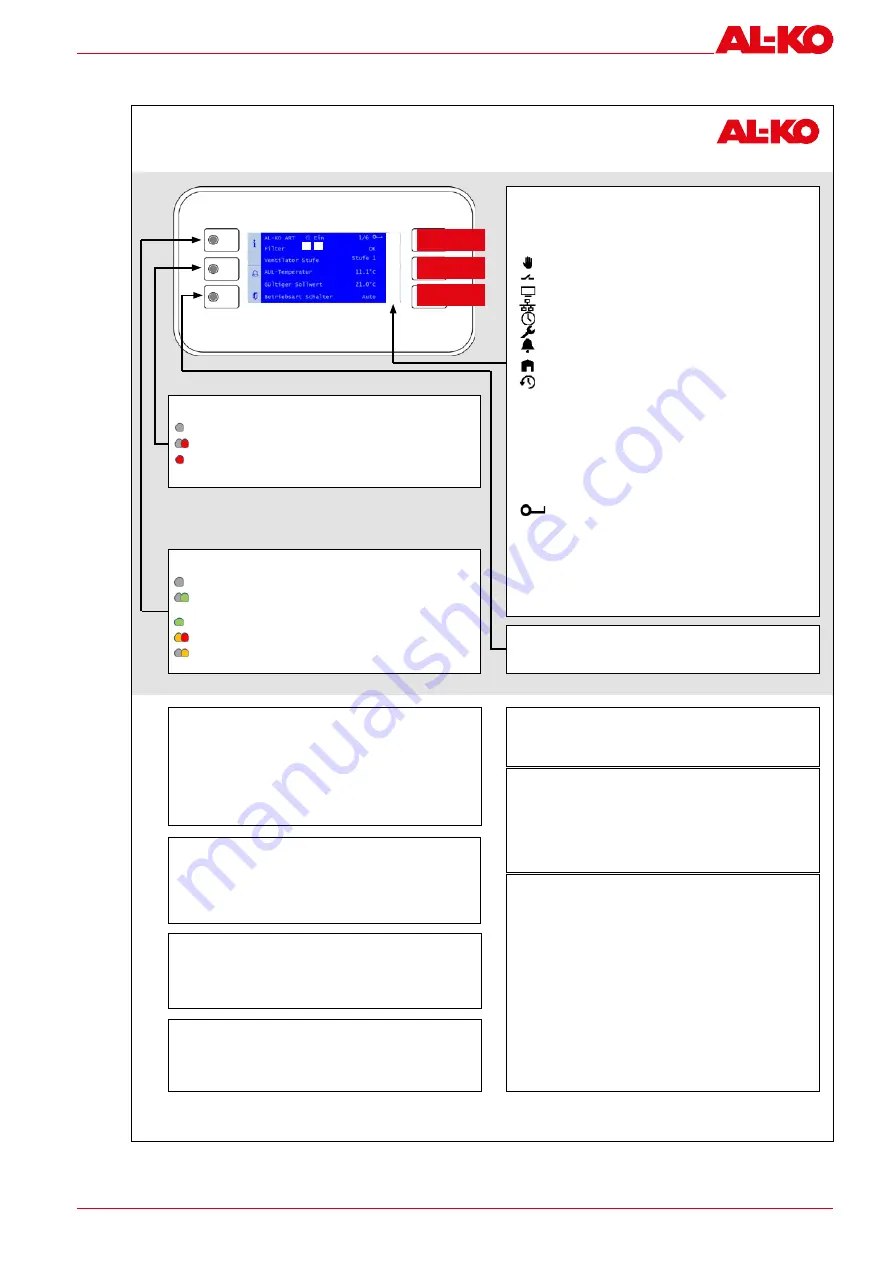
Subject to changes in line with technical progress.
49
3059570
Integrated control
7.1
HMI Basic quick start guide
ART Tech Level II
Quick Guide HMI Basic (Room Control Panel)
UP arrow key
DOWN arrow key
ENTER button
Switch on the plant using the control panel (user password required)
1. Use
INFO
to access the
start page
. Select
Operating mode
with the
arrow
keys
and press
ENTER
.
2. Use the
arrow keys
to mark the required
operating mode
and press
ENTER
.
Plant information
Use
INFO
to access the
main menu
. Select
Information
with the
arrow keys
and
press
ENTER
.
See the operating manual for a description of the individual items.
Setting the temperature setpoint (user password required)
1. Use
INFO
to access the
main menu
. Select
Setpoints
with the arrow keys and
press
ENTER
.
2. Go to
Temp control
with the
arrow keys
and press
ENTER
.
3. Select
Comfort setpoint
or
Economy setpoint
with the
arrow keys
and press
ENTER
. Now change the value with the
arrow keys
and confirm again with
ENTER
.
Setting the timer program (user password required)
1. Use
INFO
to access the
main menu
. Select
Time program
with the arrow keys
and press
ENTER
.
2. Recommendation: Set the switching times for
Monday
and copy it to the other
days. To do this, select
Monday
with the
arrow keys
and press
ENTER
.
3.
Time 1
is fixed to
00:00
and cannot be changed. For
Value 1
,
off
is recom-
mended as otherwise the plant starts at 00:00.
Use the
arrow keys
to go to
Time 2
or
Value 2
and press
ENTER
. Use the
arrow keys to send the morning compensation time (e.g.
07:00
) and the oper-
ating mode (e.g.
Stage 1
).
4. Set the other value/time pairs in the same way. Leave unused switching times
at
*:*
.
Set a corresponding
value …
to
off
as the shut-down time.
5. If necessary, copy the time switching catalogue from
Monday
to other days.
To do this, use the
arrow keys
to go to “Copy schedule” and press
ENTER
. Use
the
arrow keys
to select the destination (e.g.
Tues-Fri
for Tuesday to Friday)
and confirm with
ENTER
. The time switching catalogue is copied.
Important information!
1. The number of plant steps and the availability of the economy mode depend on
the configuration of the plant (see operating instructions).
2. In economy mode, the plant is operated at a reduced temperature setpoint. See
the operating manual for further information.
Password entry
1. Press
INFO
to access the
main menu
. The topmost entry is the
password
enter
. Press
ENTER
.
2. A password consists of four numbers. Each number is set separately with the
arrow keys
and confirmed with
ENTER
.
Enter the user password
1 0 0 0
.
After entering the password correctly, a key symbol appears at top right of the
display.
3. Other passwords levels are described in the operating manual.
Acknowledging alarms (only when alarms are pending)
1. Press
ALARM
; the
alarm list detail
appears.
2. Then press
ALARM
again; the
alarm list
appears. The topmost entry is
Ac-
knowledge
. Press
ENTER
.
3. Select
Execute
with the
arrow keys
and press
ENTER
again. The acknowledge-
ment attempt is started.
2
1
3
4
5
6
7
8
Display on the start page
If no button is pressed for a few minutes, the display jumps to the main menu.
Press
INFO
to go to the start page with the most important plant information.
1. State
Plant switched on control panel (HMI Basic, Facility, Web)
Plant switched via external enable (e.g. presence sensor)
Plant switched on the room control panel (HMI Room)
Plant switched via the building management system
Plant switched via the time program
Plant OFF: Configuration is not complete
Plant OFF: switched off alarm or emergency stop
Plant ON: Free cooling, cool-down or overheating protection
Plant ON: early start before time program (boost)
2. Operating mode
Off
Plant OFF
Start
Plant is starting up (dampers open, pre heating)
On
Plant ON
Comfort
Plant ON in comfort mode
Economy
Plant ON in economy mode
Run-on
Plant follow-up (humidifier/electrical heating coil)
3.
Display of the logged-in password level
4. Filter alarm
Display of the filter state (depending on the equipment
of the plant, the degree of soiling in percent is also
displayed).
5. Fan steps
Display of the current fan steps
6. Outside air temp
Display of the current outdoor temperature
7. Valid setpoint
Display of the current valid temperature setpoint
8. Operating mode switch Switching of the operating mode on the control panel
ESCAPE button
Press this button to return to the previous menu item.
INFO button with integrated INFO-LED
Off:
Plant off
Green flashing:
Plant starts (dampers open, preheating) or running
on (humidifier drying, electric heating cooling)
Green:
Plant on
Orange/red flashing:
Manual mode active
Orange flashing:
Plant not functional as not fully configured
ALARM button with integrated ALARM LED
Off:
No alarm; press to go directly to the
alarm history
.
Red flashing:
Alarm
Red:
Alarm is still active; an attempt has been made to ac-
knowledge it
3421375