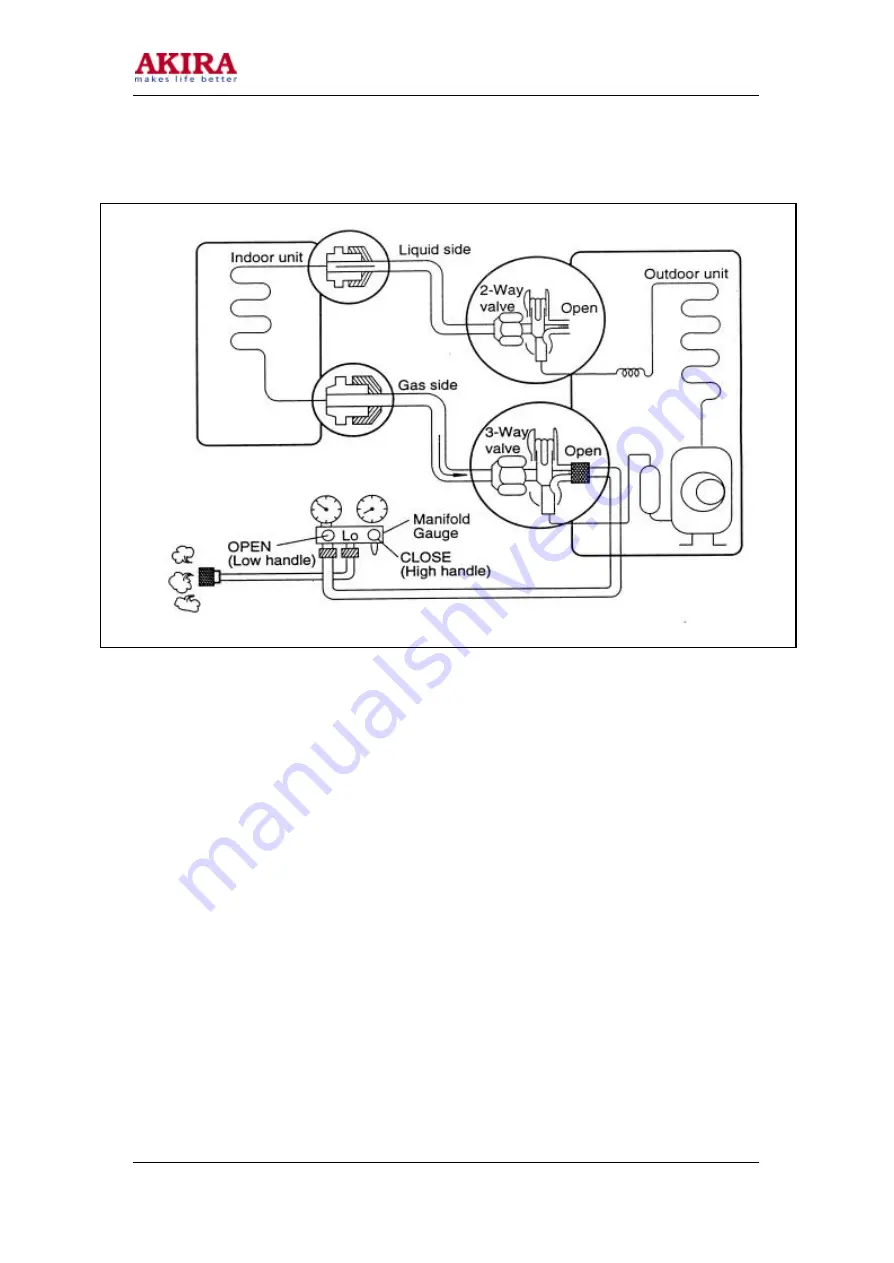
39
Model No:
AC-S10CK_S10HK
Version 1.0
F
Leave the valve on the charge set closed.
F
Connect the charge hose with the push pin to the service port.
l
Open the valve (Low side)on the charge set and discharged the refrigerant until
the gauge indicates 0kg/cm
2
.g.
F
If there is no air in the refrigerant cycle (the pressure when the air conditioner is
not running is higher than 1 kg/cm
2
.g),discharge the refrigerant until the gauge
indicates 0.5 to 1 kg/cm
2
.g.If this is the case, it will not be necessary to apply an
evacuation.
F
Discharge the refrigerant gradually. If it is discharged too suddenly, the refrigera-
tion oil will also be discharged.
5. EVACUATION (ALL AMOUNT OF REFRIGERANT LEAKED)
l
Connect the vacuum pump to the charge set’s center hose.
l
Evacuating for approximately one hour.
F
Confirm that the gauge needle has moved toward -76cmHg (vacuum of 4
mmHg or less)
Summary of Contents for AC-S10CK
Page 24: ...24 Model No AC S10CK_S10HK Version 1 0 F Cut the cable a 1 5m longer than the pipe length ...
Page 50: ...50 Model No AC S10CK_S10HK Version 1 0 2 Exploded view of outdoor unit for model AC S10CK ...
Page 51: ...51 Model No AC S10CK_S10HK Version 1 0 3 Exploded view of outdoor unit for model AC S10HK ...