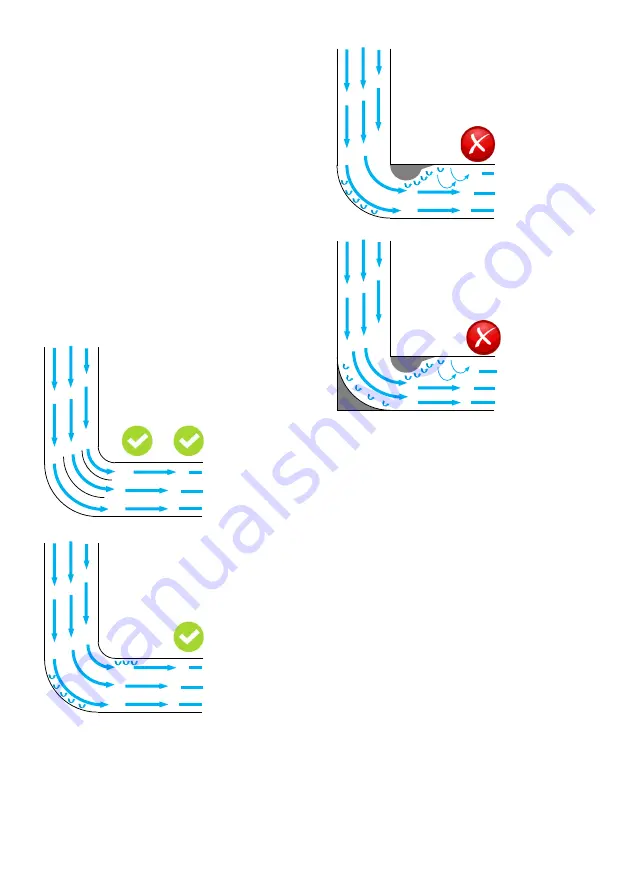
20
7.5 Length of the Exhaust Ducting,
Curves & Bends
As the length of the exhaust ducting increases, the
counter pressure (duct resistance) increases and the
airflow rate decreases.
Bends and curves are problematic as they present
deflection surfaces that dam the air steam and
generate turbulence. This causes an increase in
counter pressure. Bends and curves in the ducting
should therefore be kept to a minimum. If bends
and curves are required for structural reasons,
bends with largest possible radius are advisable. The
smaller the bend radius, the greater the counter
pressure. Corners at right angles should also be
avoided if possible because these lead to even
greater pressure losses and therefore a loss of
performance.
TIP
The following rule of thumb applies for good duct
routing:
The distance between two bends should be at least
1m, although 1.5m is better.
Optimal flow due to integrated guide
bodies and rounded edges in the duct
bends of Compair ducting system.
Good flow as a result of
rounded edges.
Unfavourable flow:
Air swirls are created behind the
sharp interior corners.
Bad flow:
Air swirls are created behind the
sharp corners.