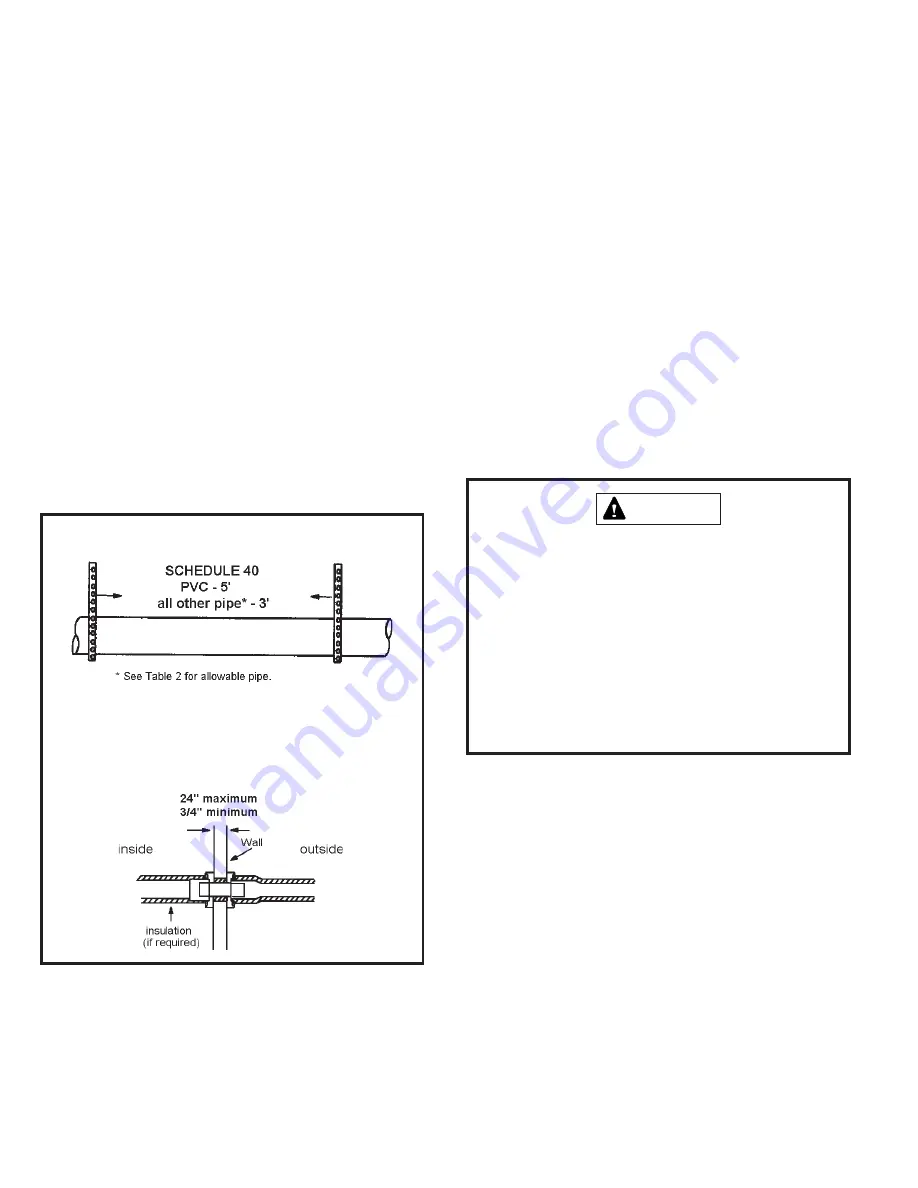
506878-01
Page 16 of 62
Issue 1139
6. Promptly apply solvent cement to end of pipe and inside
socket surface of fitting. Cement should be applied
lightly but uniformly to inside of socket. Take care to
keep excess cement out of socket. Apply second coat
to end of pipe.
7. Immediately after applying last coat of cement to pipe,
and while both inside socket surface and end of pipe
are wet with cement, forcefully insert end of pipe into
socket until it bottoms out. Turn PVC pipe 1/4 turn during
assembly (but not after pipe is fully inserted) to distribute
cement evenly. Do not turn ABS or cellular core pipe.
NOTE:
Assembly should be completed within 20 seconds
after last application of cement. Hammer blows should not
be used when inserting pipe.
8. After assembly, wipe excess cement from pipe at end
of fitting socket. A properly made join will show a bead
around its entire perimeter. Any gaps may indicate an
improper defective assembly due to insufficient solvent.
9. Handle joints carefully until completely set.
Exhaust Piping
1. In areas where piping penetrates joist or interior walls,
hole must be large enough to allow clearance on all sides
of pipe through center of hole using a hanger.
2. When furnace is installed in a residence where unit is
shut down for an extended period of time, such as a
vacation home, make provisions for draining condensate
collection from trap and lines.
Removal of the Furnace from Common Vent
In the event that an existing furnace is removed from a
venting system commonly run with separate gas appliances,
the venting system is likely to be too large to properly vent
the remaining attached appliances.
Conduct the following test while each appliance is operating
and the other appliances (which are not operating) remain
connected to the common venting system. If the venting
system has been installed improperly, you must correct the
system as indicated in the general venting requirements
section
.
Venting Practices
Piping Suspension Guidelines
NOTE:
Isolate piping at the point where it exits the outside wall or
roof in order to prevent transmission of vibration to the structure.
Wall Thickness Guidelines
Figure 18
WARNING
CARBON MONOXIDE POISONING HAZARD
Failure to follow the steps outlined below for each
appliance connected to the venting system being placed
into operation could result in carbon monoxide
poisoning or death.
The following steps shall be followed for each appliance
connected to the venting system being placed into
operation, while all other appliances connected to 1he
venting system are not in operation:
1. Seal any unused openings in the common venting
system.
2. Inspect the venting system for proper size and horizontal
pitch. Determine that there is no blockage, restriction,
leakage, corrosion, or other deficiencies which could
cause an unsafe condition.
Summary of Contents for 95G2UHV
Page 3: ...506878 01 Page 3 of 62 Issue 1139 EXPANDED VIEW Figure 1 ...
Page 28: ...506878 01 Page 28 of 62 Issue 1139 Figure 31 FIELD SUPPLIED WALL TERMINATION ...
Page 29: ...506878 01 Page 29 of 62 Issue 1139 Figure 32 ...
Page 35: ...506878 01 Page 35 of 62 Issue 1139 Figure 47 TRAP DRAIN ASSEMBLY USING 1 2 PVC or 3 4 PVC ...
Page 46: ...506878 01 Page 46 of 62 Issue 1139 TYPICAL WIRING DIAGRAM Figure 56 ...
Page 60: ...506878 01 Page 60 of 62 Issue 1139 Start Up Performance Check List UNIT SET UP ...
Page 61: ...506878 01 Page 61 of 62 Issue 1139 UNIT OPERATION Heating Mode Cooling Mode ...