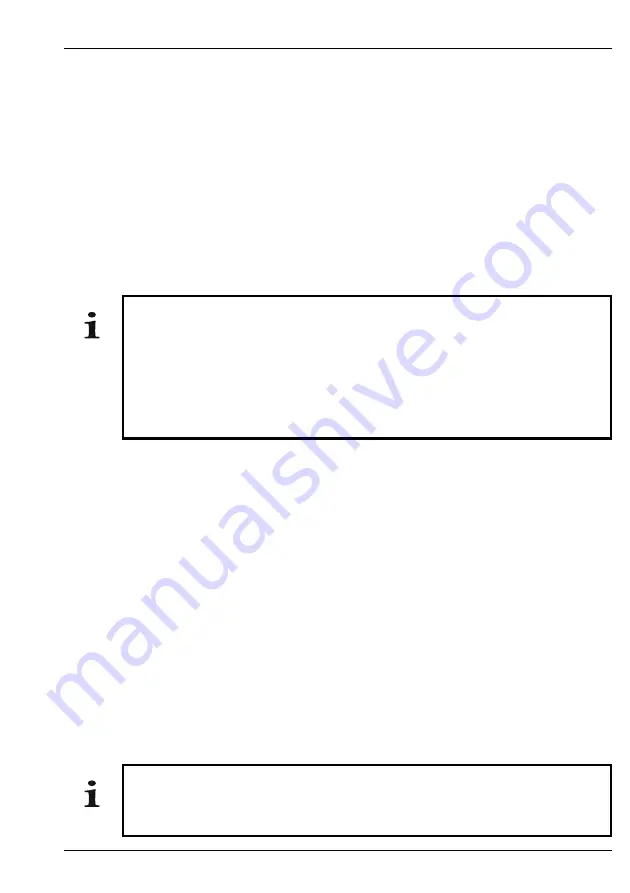
3 Product description
3.4 Technical data
Actuators NK and VK, Position Controller ESR-NK
19
3.4.5 Functional data
Torques, positioning forces and positioning ranges
NK
Torque:
2 to 15Nm
Positioning times:
0.8s/90° to 120s/90°
Swivel range:
max. 300°
VK
Positioning force:
up to 1,000N
Stroke:
max. 20mm
(Positioning times on request)
Important information!
The torques and positioning forces specified above are nominal values.
They are reached when the supply voltage corresponds to the rated volt-
age.
–
In some cases, the actual torque may be higher than the rated torque!
–
In some cases, the actual positioning force may be higher than the
rated positioning force!
Gearbox
Maintenance-free steel spur gearing
Installation position
NK
Any orientation
VK
Prescribed installation positions
(see Fig. 5.3
“Series VK – installation positions”
)
Switches
−
Switch function: changeover switch (NC/NO contact)
−
Switching capacity: max. 2.5A, 250V AC
Switches with gold-plated contacts are available for small switching loads and
low voltages.
Important information!
Limit switches and auxiliary switches are
not
suitable as signal encoders
for safety-related controls!
Summary of Contents for ESR-NK Series
Page 6: ......
Page 28: ......
Page 58: ......
Page 78: ......
Page 86: ......
Page 92: ...11 1 Certificates 11 Appendix 86 Actuators NK and VK Position Controller ESR NK...
Page 93: ...11 Appendix 11 1 Certificates Actuators NK and VK Position Controller ESR NK 87...
Page 94: ...11 1 Certificates 11 Appendix 88 Actuators NK and VK Position Controller ESR NK...
Page 95: ...11 Appendix 11 1 Certificates Actuators NK and VK Position Controller ESR NK 89...
Page 96: ......