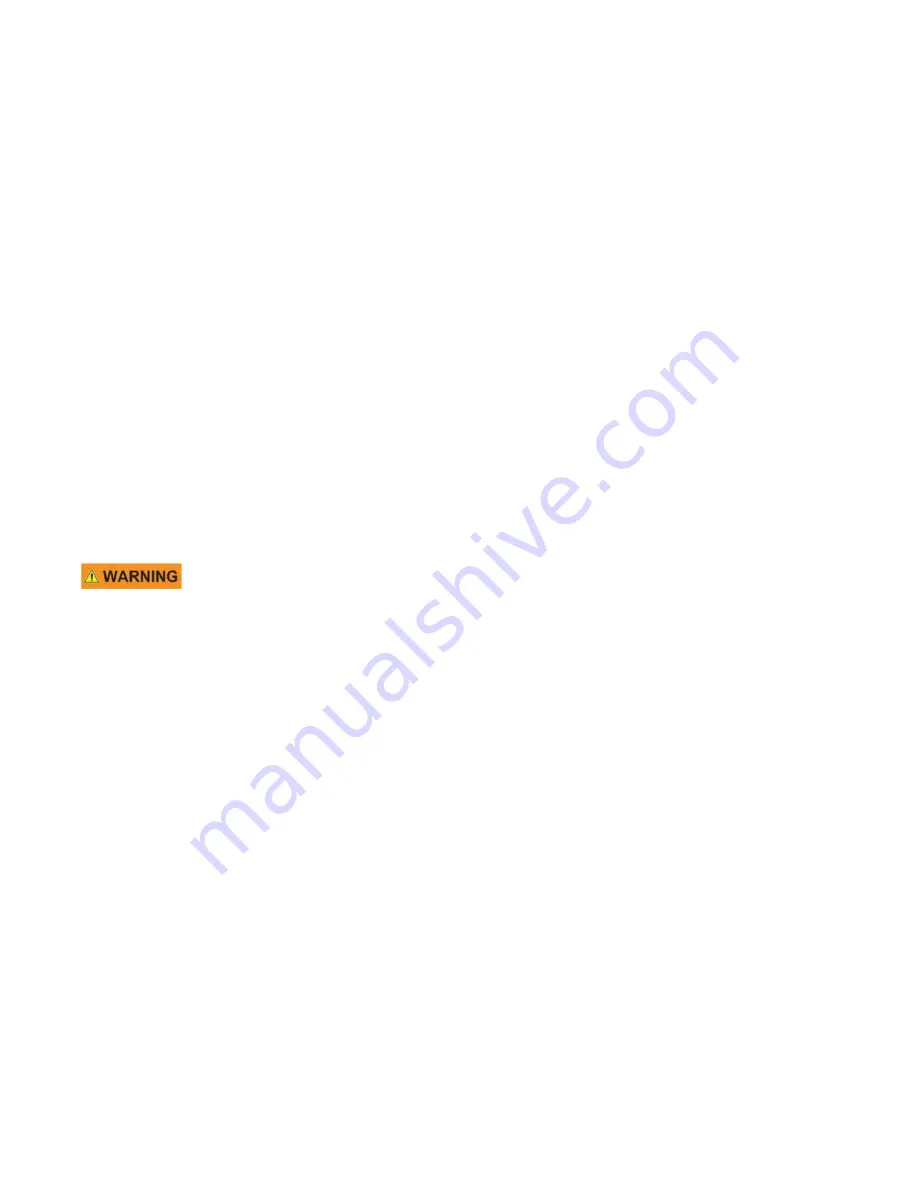
7713397 R2
35
Natural Gas (NG) Fuel Source
• Refer to the Standard Model Specifications table in
Section 5. – Specifications on page 100
for maximum
heat capacity output. Ensure that the pressure supplied to the fuel train inlet is 15 to 20 psi.
• The natural gas inlet line fitting for all NECO Dryers is 2".
• The supply regulator set should be located near the dryer to reduce the supply line length.
• Contact your local natural gas supplier for line sizing.
Fuel Train Inspection
Important
The following inspections should be done at initial installation, as well as annually, to ensure safety:
•
The dryer fuel train shall be inspected for leaks to verify the gas tightness of the dryer components
and piping under normal operating conditions. After installation and annually, use a solution of soap
and water to check fittings and pipe for leaks.
•
The gas tightness of the solenoids can be checked by adding test gauges to the test ports of the
main solenoid valves. While the dryer is running, turn off the manual shutoff valve before each
burner, and turn off the fuel supply manual shutoff at the inlet fuel supply to the dryer. Monitor the
pressure of upstream and downstream pressure gauges. If the pressure of any of the gauges drops
to zero, there could be a leak in the system. Use a solution of soap and water to find the source of
the leak.
4.4.3 Set Up Electrical Supply
• NECO recommends hiring an expert for proper advice, accurate paperwork, and safe
procedures to complete electrical work in conformance with local codes.
• For dryer installations in Canada — Electrical disconnect shall be installed and all wiring
must be done in accordance with the Canadian Electrical Code, Part 1, CSA C22.1.
• The Dryer Rating Label on the control panel lists the full-load amps required for the dryer and the input
voltage.
• The customer is responsible for providing materials and labor to connect the control to the power source,
including a properly sized and placed fused disconnect box.
• The electrical power supply will have to meet service amp requirements.
• Copper wire of the appropriate size, based on the required amps and distance, must be run between the
main disconnect switch and the distribution block located in the dryer control panel.
CONTINUOUS-FLOW GRAIN DRYER – COMMANDER CONTROL