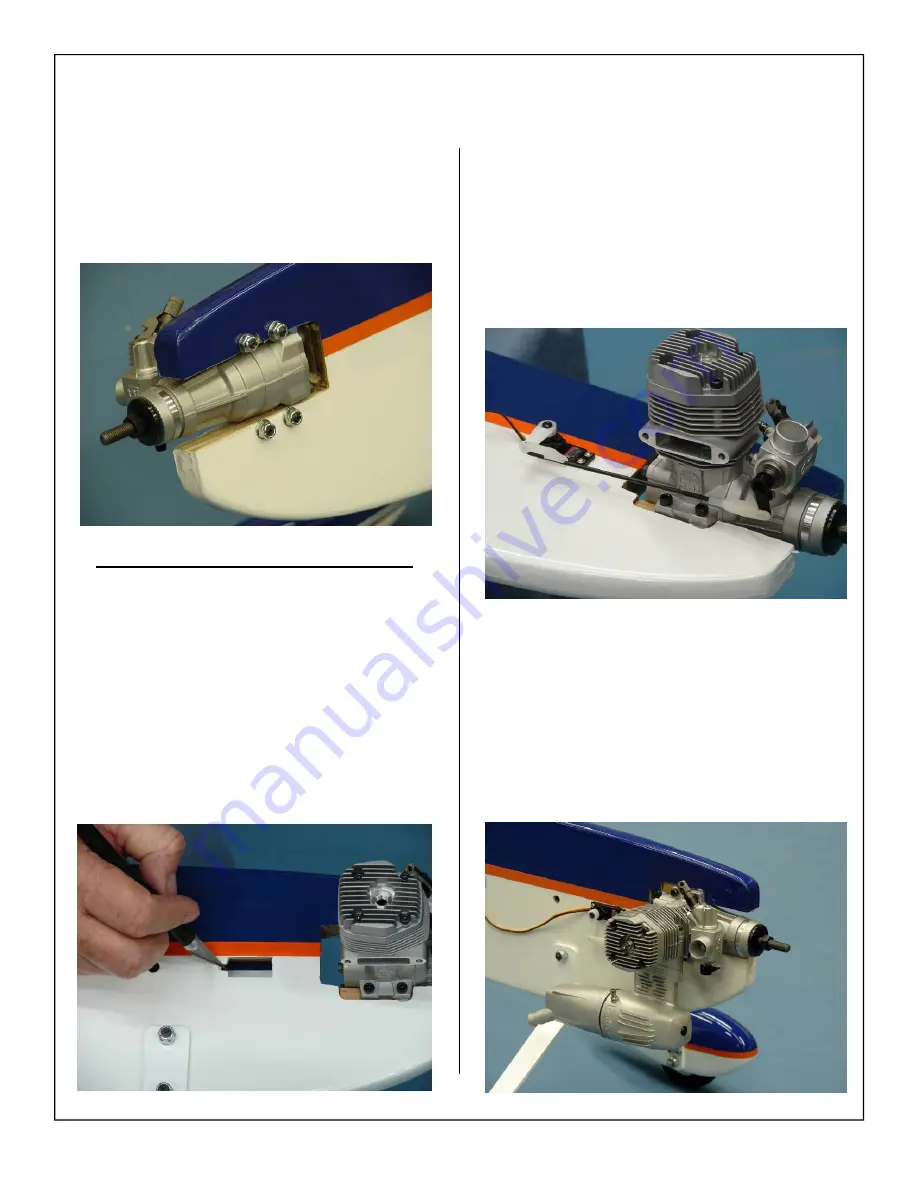
29
6. Place engine between mounting rails and allow
all four bolts to pass through. Install flat washer
and 6-32 lock nuts onto mounting bolts and
tighten them evenly. Ensure that the wood does
not crush as the bolts are tightened.
2 Stroke Throttle Servo Installation
1. Remove the covering from the
LOWER
throttle
servo mount using a sharp hobby knife as
shown.
Note:
Two throttle servo mounting locations have
been provided, if using a 4 stroke engine
please skip to step #1 on page 30
2. Install the throttle servo using the servo screws
provided with the servo.
3. Install throttle servo linkage as shown below.
4. Finished 2 stroke engine installation shown be-
low.