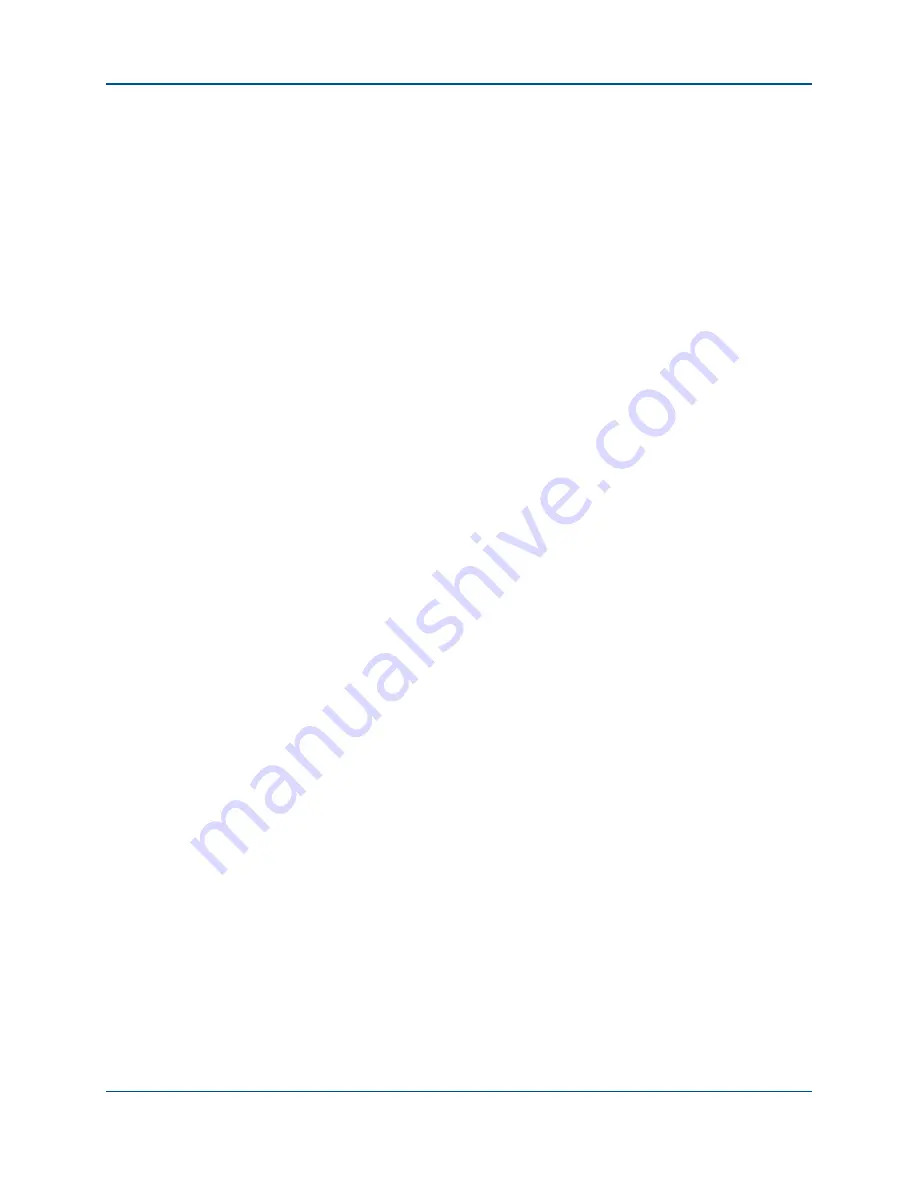
BM/BMS Series Hardware Manual
Introduction
www.aerotech.com 1-21
1.7. Installation
Motors are installed by bolting the motor flange to a mounting surface using four holes
on the motor flange. The load is connected to the motor shaft using keyways and/or flats
(See motor drawing for additional information and availability).
1.7.1. Wiring
External wiring to the motor must meet certain requirements. Wiring must be able to
carry the rated current without overheating. The insulation of the wire must be rated for
the voltage at which the motor will be operating. The Protective Ground must meet rated
current requirements. Signal wiring (Encoder, Hall, etc…) must have the proper
insulation voltage rating and current carrying capacity.
The motor power conductors must be sized to handle the maximum current of the motor.
The motor fuse or other protective device typically determines this current. The
insulation must be rated for the maximum voltage applied to the motor (300V wire
insulation typical). As a minimum requirement the motor wiring must be shielded to
reduce electromagnetic emissions.
The Protective Ground is a safety conductor that is used to ground the motor case. The
Protective Ground conductor must have a current capacity that is at least equal to the
motor wires. The insulation of the Protective Ground wire is standard Green/Yellow and
must be rated for the maximum voltage that will be applied to the motor. The Protective
Ground wire is usually bundled along with the motor wires, but system requirements may
require that a separate Protective Ground wire is needed.
Signal wires should have a current capacity of at least 1 Amp. The insulation of the wires
should have a rating of at least the maximum voltage (300 V typical) that will be applied
to the motor. As minimum requirements the signal wires need to be bundled together
within a shielded cable and signal and motor wires must not be bundled together. Motor
wires must be shielded separately from the signal wires to prevent EMI interference.
Summary of Contents for BM Series
Page 6: ...Table of Contents BM BMS Series Hardware Manual iv www aerotech com...
Page 8: ...List of Figures BM BMS Series Hardware Manual vi www aerotech com...
Page 10: ...List of Tables BM BMS Series Hardware Manual viii www aerotech com...
Page 12: ...Declaration of Conformity BM BMS Series Hardware Manual x www aerotech com...
Page 50: ...Appendix A BM BMS Series Hardware Manual A 8 www aerotech com...
Page 56: ...Index BM BMS Series Hardware Manual Index 2 www aerotech com...
Page 58: ......