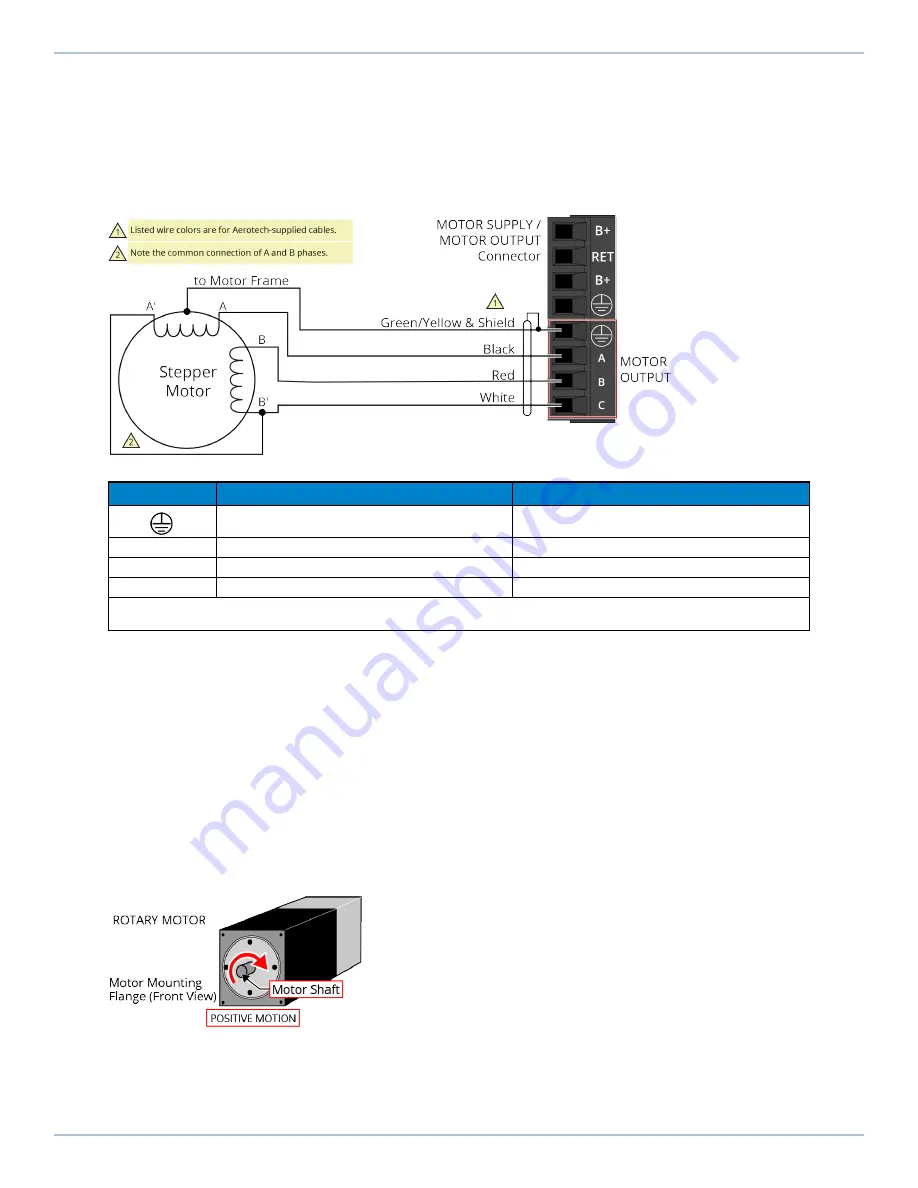
2.2.3. Stepper Motor Connections
The configuration shown in
is an example of a typical stepper motor connection. Refer to
for information on motor phasing.
In this case, the effective motor voltage is half of the applied bus voltage. For example, an 80 V motor
bus supply is needed to get 40 V across the motor.
Figure 2-10:
Stepper Motor Configuration
Table 2-10:
Wire Colors for Aerotech-Supplied Stepper Motor Cables
Pin
Wire Color Set 1
(1)
Wire Color Set 2
Green/Yellow & Shield
(2)
Green/Yellow & Shield
A
Black
Brown
B
Red
Yellow
C
White
White & Red
(1) Wire Color Set #1 is the typical wire set used by Aerotech.
(2) “&” (Red & Orange) indicates two wires; “ / ” (Green/White) indicates a single wire.
2.2.3.1. Stepper Motor Phasing
A stepper motor can be run with or without an encoder.
Without an Encoder:
You do not need to phase the motor.
With an Encoder:
Because the end of travel (EOT) limit inputs are relative to motor rotation, it is
important to phase the motor.
Run a positive motion command. The motor is phased correctly if there is a positive scaling factor
(determined by the CountsPerUnit parameters) and the motor moves in a clockwise direction when
you view the motor from the front mounting flange (
). If the motor moves in a
counterclockwise direction, swap the motor leads and re-run the command. After the motor has
been phased, if you want to change the direction of positive motion, use the ReverseMotionDirection
parameter.
Figure 2-11:
Positive Motor Direction
For Aerotech-supplied systems, the motor, encoder and Hall sensors are correctly configured and
connection adjustments are not necessary.
2.2.3. Stepper Motor Connections
XL2e Hardware Manual
34
www.aerotech.com