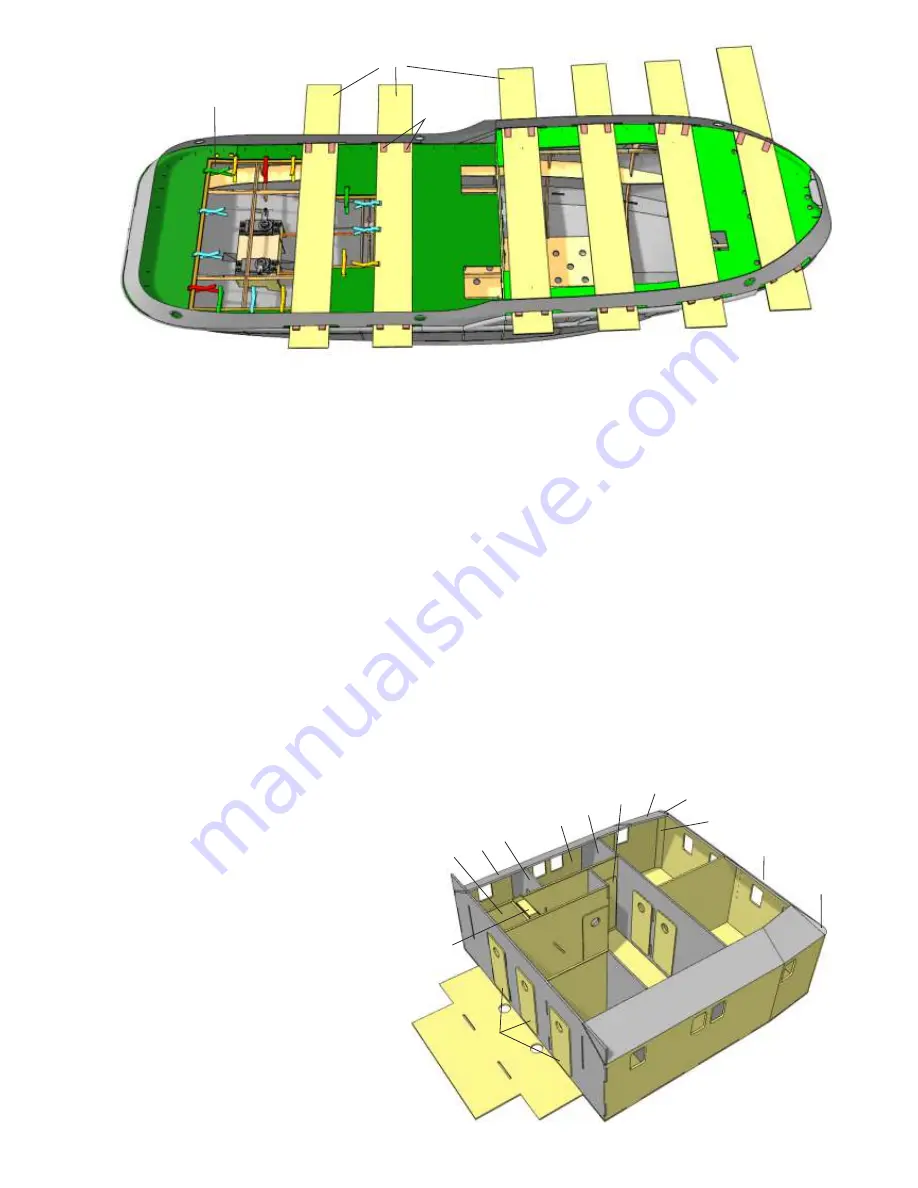
Stern roller
The parts of the stern roller should be glued together as shown in the
drawing. Prepare the cradle by curving it over a table edge or cylindrical
former. Glue parts 51 in the cradle, then glue the bearing plates 55 in the
roller 54. If you wish, 4 x 8 mm ballraces can be fitted in the bearing
support.
The final step is to glue the bearing cover 53 on the end.
Slip the shaft 56 through all the parts to check alignment, and leave it in
place while the glued joints harden.
53
52
51
55
54
50
56
Remove a section 74 x 24 mm in size from the centre of the hull
at the stern, as shown in the drawing, and glue the stern roller
cradle in the opening using Stabilit or Acrylit. Cut back the bulge
in the stern bulwark at an angle of about 24°.
Round off the sides of the bulwark adjacent to the cradle.
Cut out the openings for the scuppers and cable hawses using a
diamond cut-off disc.
The top edge of the deck is the top edge of the fore-and-aft
bulge on the hull.
Glue the main deck supports 57 and doublers 58
together on a flat surface. Don't glue the front and
rear parts together.
The outside edges must line up flush.
Glue the deck supports 57 / 58 in the notches in
the frames.
Apply glue between the two parts, and tape the
area where the supports are angled.
57 58
Main deck
Important:
check that the scuppers are cut out as far as the peripheral rubbing strake. The correct scupper height is about 5 mm.
Remove the main deck 59 and remove any rough edges on the rear face.
Press the deck into the hull.
Engage the front lugs in frame 13.
Since the hull is hand-laminated, the wall thickness may vary slightly in the area where the hull meets the bulwark at the level of the peripheral
rubbing strake.
Sand smooth any irregularities in the hull, and trim the deck until it is a snug fit.
The rear face of frame 13 must end flush with the rear scupper and the step in the rubbing strake.
- If you have not installed the stern roller, the deck support 25 can now be glued in place.
- If you have fitted the stern roller, the engraved area of the main deck 59 must first be removed.
Cut a few wedges from the spruce strip 61. Cut the spruce strip 60 into suitable lengths and fit them through the scuppers above the deck. Now
use the wedges to press the deck down. This action presses the framework down onto the bottom of the hull, and the glued joints can now be
completed. The sole purpose of the framework is to support and secure the deck, so there is no need to glue all the joints over their full length.
17
18
19
20
Steps 17 and 18 describe the installation of the stern roller. If you don't wish to install the system, please continue with Step 19.
spring clips
60
Wedges 61
59
64
Allow the glued joints to set hard, then remove the main deck and apply adhesive (Stabilit or Acrylit) to the top edge of the frames. Place the
deck in position again, and secure it using the wedges and rulers or other long strips. Use spring clips to press the deck onto the deck supports
as shown.
Allow the glued joints to set hard, then place the foredeck 64 in position and check that its rear edge lines up flush with frame 13. You may
need to carry out minor trimming to the front area of the deck to achieve this. Remove any irregularities on the inside of the GRP hull. Mark on
the inside of the hull the height of the foredeck support 25, and glue it in place.
Remove the foredeck again.
Now glue the foredeck girders 24 to frame 16. Fit frame 17 in the hull under the deck girders, spaced about 84 mm from frame 16, then glue it
in place with cyano. Apply Stabilit or Acrylit to the top edge of the frames. Place the foredeck in position and secure it as described before
using rulers, wooden strips and wedges.
It is important not to distort the rear end of the deck, otherwise the superstructure will not fit. The inside of the opening must end flush with
the frames. Glue frame 17 in the hull.
Leave all the glued joints to set hard, then remove all the wedges and clamps.
Fill any gaps between hull and deck with Stabilit or Acrylit, immediately wiping away any excess adhesive before it sets using a cloth or
kitchen paper soaked in methylated spirit ('meths'). Check that the slots in the deck for the bulwark stanchions are not blocked with glue. If
they are, immediately open them up with a pointed balsa strip.
The hawse pipes 7 can now be trimmed to fit and glued in place; glue them under the anchor winch 7.1. Lay the hull on one side and apply
spray filler or filler / primer on the inside of the bulwark. Alternatively apply conventional filler paste and sand smooth when dry.
The deckhouse coaming is fitted next, but not before the lower section of the deckhouse is built.
Deckhouse
Place the base plate on a flat surface, and glue
the individual sheet components to it following
the sequence of the part numbers. Note that all
the parts have tabs and slots which only fit one
way round. Make the superstructure fillets 70
from the tube material: quarter the tubes
lengthwise and trim them to fit.
Repeat the procedure with the upper
superstructure fillets 71.
Parts 84 and 85 butt together at the top.
Trim the upper superstructure fillets to fit as
shown.
Assemble the companionway 86; it will be
glued to the angled wall 79, but only after the
lower deckhouse has been painted.
73
79
85
75
66
78
74
85
71
70
66
72
84
67
71
85
85
66
66
81
77
76
69
68
83
65
82
86
21
22
23
24
Summary of Contents for Jonny
Page 1: ...aero naut Jonny Harbour tug Order No 3030 00...
Page 30: ......
Page 31: ......
Page 32: ......
Page 33: ......