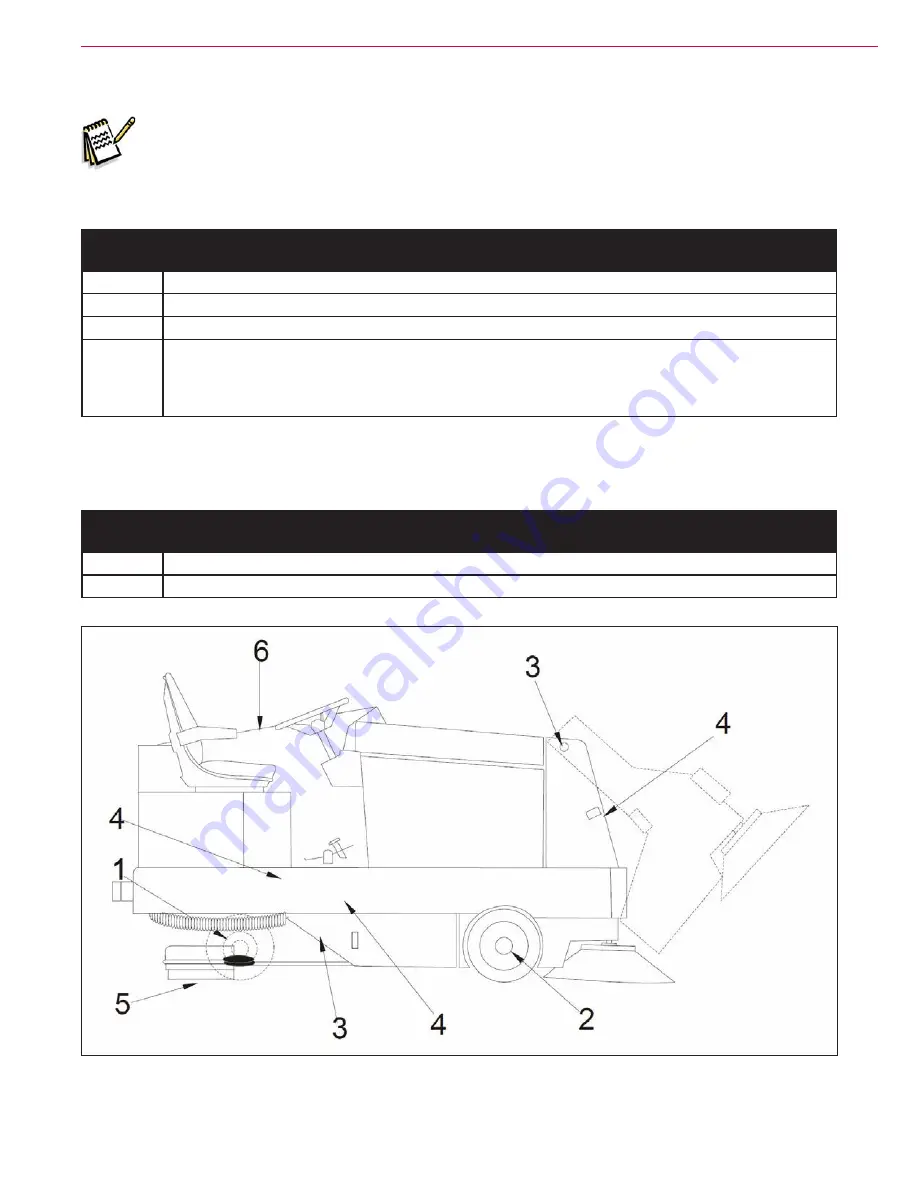
General Information
29
Service Manual – Advance 7765 / Nilfisk CR1500
Lubrication Locations
Note:
Use a good grade multipurpose grease. Avoid using too much grease.
Lubrication Every 100 Hours
Location
Number
Procedure
1
Lubricate the drive wheel swivel, wheel bearings and steering rack guide
2
Lubricate the front wheel bearings
3
Lubricate all moving joints
4
Lubricate all bushings with Loctite
®
Silver Grade Anti-Seize compound. Note that the bushings
are located on the steering, scrub deck lift, squeegee lift, main broom lift, both threaded ends of
the throttle cable and on the variable dump door cylinders. (Refer to the relevant sections in this
manual and the Parts List.)
Lubrication Every 250 Hours
Location
Number
Procedure
5
Lubricate the squeegee casters
6
Clean and lubricate the governor linkage (diesel only)
Summary of Contents for 56514925
Page 28: ...General Information 28 Service Manual Advance 7765 Nilfisk CR1500 Maintenance Item Locations ...
Page 74: ...Engine System common Electrical System 74 Service Manual Advance 7765 Nilfisk CR1500 ...
Page 89: ...Engine System Diesel 89 Service Manual Advance 7765 Nilfisk CR1500 Starter Relay ...
Page 113: ...Engine System Gasoline LPG 113 Service Manual Advance 7765 Nilfisk CR1500 ...
Page 114: ...Engine System Gasoline LPG 114 Service Manual Advance 7765 Nilfisk CR1500 ...
Page 115: ...Engine System Gasoline LPG 115 Service Manual Advance 7765 Nilfisk CR1500 ...