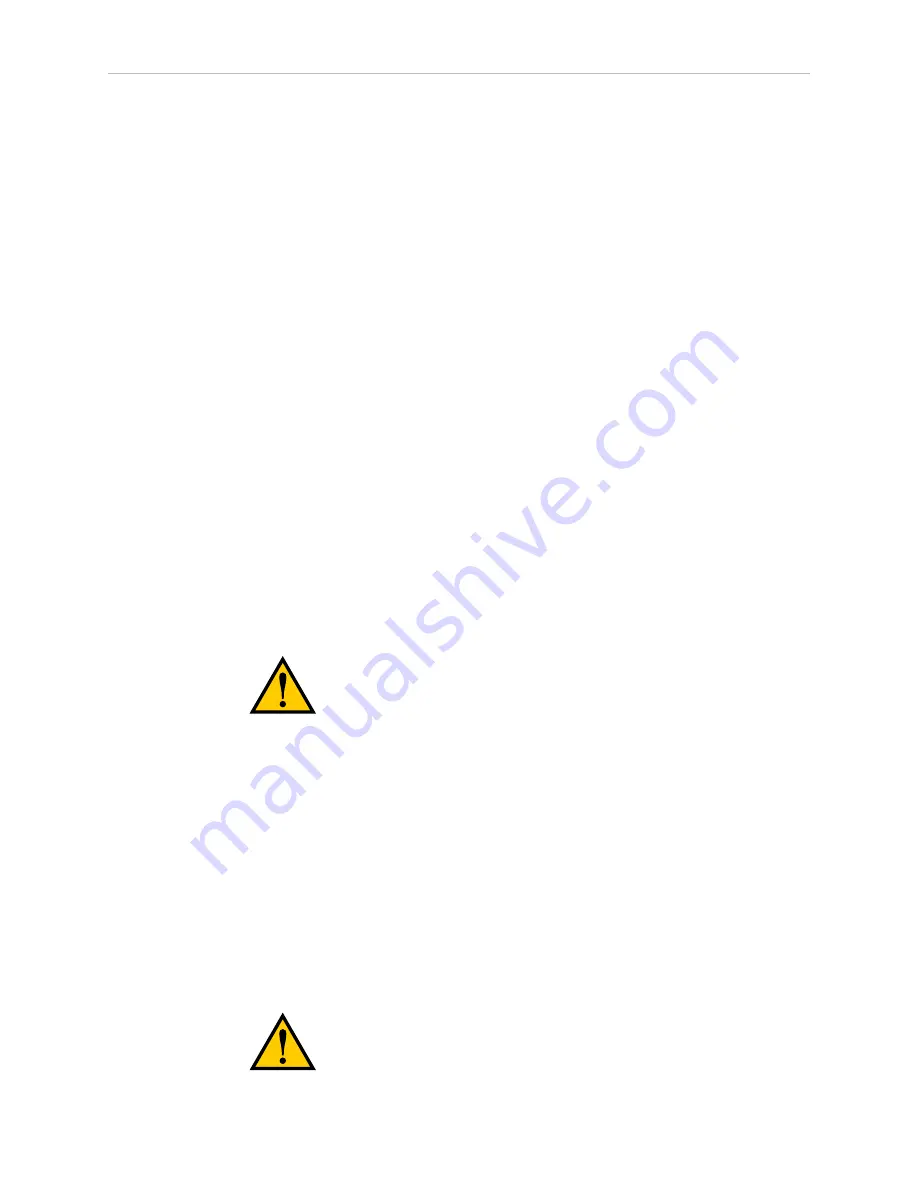
Chapter 2: Robot Installation - H
Figure 7-2 shows the mounting hole pattern for the Adept Quattro robot. Note the hole location
and mounting pad tolerances for position and flatness.
Deviation from this flatness specification will, over time, cause a possible loss of robot
calibration. If the frame does not meet this flatness specification, use shims to achieve it.
NOTE:
Adept suggests welding the robot mounting tabs as a last step in the frame
fabrication, using a flat surface as a datum surface during the tack welding
operation.
Gussets
The triangular gussets are an integral part of the frame stiffness. The vibrational strength of a
structural assembly is strongly governed by controlling the shear forces between members. The
250 mm gussets, shown in Figure 2-3, are nominally sufficient for transferring the load from
the vertical members into the horizontal cross pieces. Preferably, gussets should be placed at
the edges of the frame members to transfer the loading into the walls of the members, instead
of the faces, and enable easier cleaning. Some frame designs may benefit from extending these
gussets to 500 mm in the vertical direction, as the design intent of the gussets is mainly to
secure the long vertical members from rotating out of position. For this reason, the gussets to
the across-the-belt horizontal member should be at the bottom of the member, as shown in
Figure 2-3, and as close to the vertical midplane of the frame as feasible (15 mm thickness is
adequate for most situations).
2.6 Mounting the Robot Base
NOTE:
All mounting hardware is user-supplied.
CAUTION:
Remove all ancillary components (controller,
outer arms, platform, etc.) from the shipping crate before
lifting the robot base.
Robot Orientation
Adept recommends mounting the Adept Quattro robot so that the Status Display Panel faces
away from the conveyor belt. Although the work envelope of the robot is symmetrical, this
orientation gives better access to the status display, status LED, and Brake-Release button. It
also balances the arm loading for aggressive moves across the belt.
This orientation places the robot World Y-axis along the conveyor belt, and the X-axis across
the belt.
Mounting Surfaces
Mounting surfaces for the robot mounting flanges must be within 0.75 mm of a flat plane. If
the surfaces do not meet this tolerance, use shims to attain it.
CAUTION:
Failure to mount the Quattro robot within
0.75 mm of a flat plane will result in inconsistent robot
motions.
Adept Quattro User's Guide, Rev E
Page 32 of 180
Summary of Contents for Quattro s650H
Page 1: ...Adept Quattro User s Guide covers the Adept Quattro s650H s650HS s800H and s800HS Robots...
Page 2: ......
Page 82: ......
Page 102: ......
Page 108: ......
Page 164: ......
Page 174: ......
Page 178: ......
Page 179: ......
Page 180: ...P N 09955 000 Rev E 5960 Inglewood Drive Pleasanton CA 94588 925 245 3400...