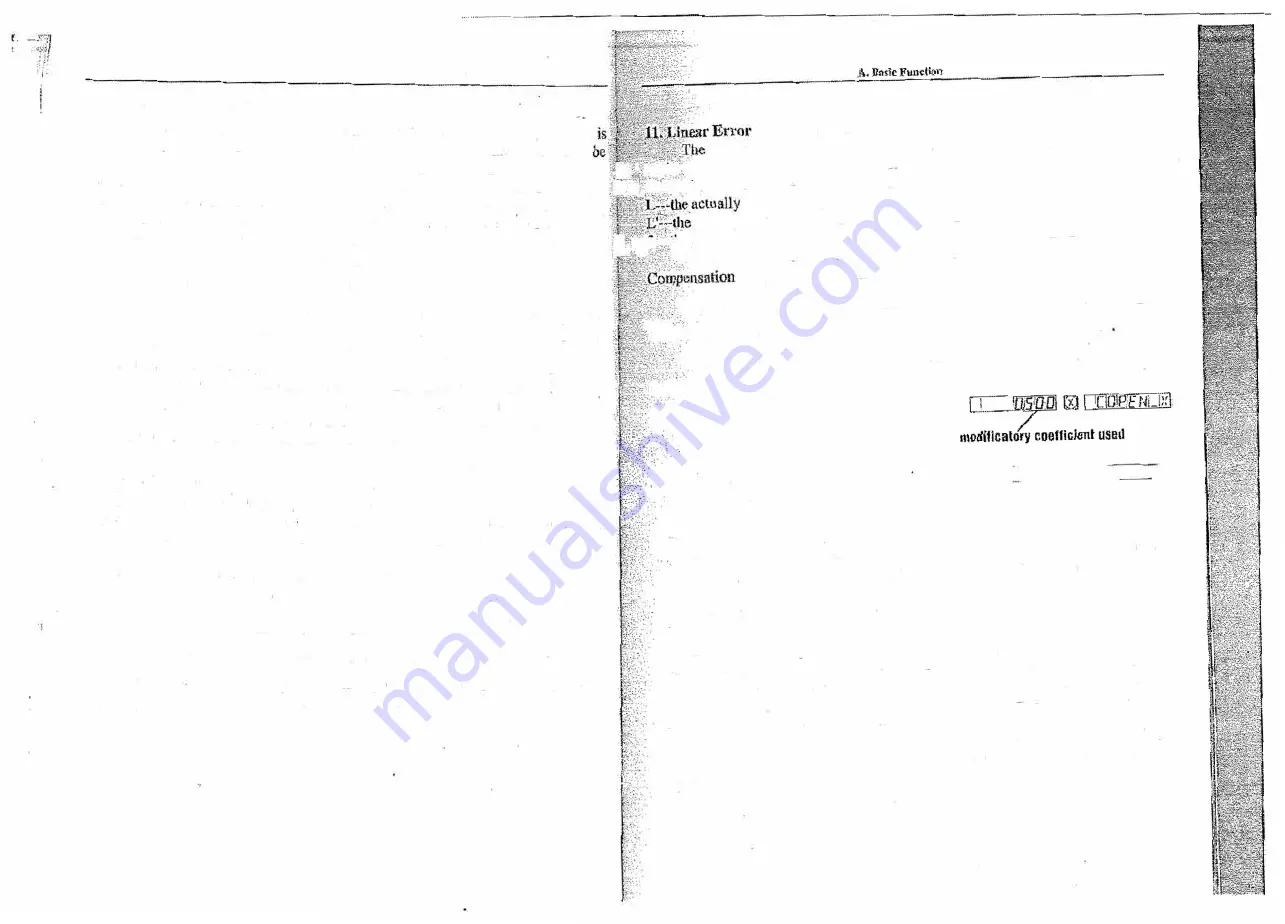
A, !Jaslc Function
3. Finding the function of the mechanical origin
If II
·
ff h I
t
I ·
·
th
t
I
Compensation
'·- I 1·
onection
1ere 1s power o w en t 1e ras er ru er Is movrng, or e ra er ru er
linear error compensation function is used to maiu: t 1e mear c
moved before the power is on, after re-start, the mechanical origin needs to
.
t
error of the grating metermg sys em.
found again. Because of movement in power off or before power on, the f:/',ofJ[1esy
st
•er
fnactor
S
=(L-L')/(L/lOOO) mm/m
coordinate origin of the machine tool can not match the value in the digit display lt[f,
Corr
�(:ll.on
metered length (mm)
meter. If the mechanical origin is not found, the misplaced relationship is brought
dis layed value on digital display meter (mm)
.
. d
into the later user coordinate system. As when calculating the user coordinate, the
P 11 f
( ml ) "+" symbol means the actual length 1s larger, au
Segmented compensation value is found according to tile wrong mechanical
j;
)
Y
f
>
.
····�� actua Y actor m m '
.
all
:1
"·" symbol means the actual length rn sm er.
coordinate, thus thereis big eil'Or of the displayed coordinate.
range: -I.SOO t l.500 mm/m
The method of finding mechanical origin is as follows:
.
Example: The Actual metered length of the machine tool machine table is
I .Move the raster ruler to the position which is initially set up as the
·
I
t · 999 98 mm
mechanical origin, and then set up Segmented compensation. When inputting
"tOOOmm, and the display value on the digital <lisp ay me er IS
.
the quantity of compensation segment and the compensation length, do not
· · S:(J000,999.98)1(1000/1000)=0.02 mm/m
nrnke any change, and press
I]:!
directly to skip. Enter into the interface for
choosing compensation method, press
iBJ.
The. interior of digit display meter
I) Select the.axis
0
handles automatically. At this time, directly press
!SJ
key to quit the Segmented
compensation setup, and finish finding the mechanical origin.(Remarks: II is
2) 1(ey
!SJ
applicable to setting up parameters according to sketch map 1)
2.First!y move the raster ruler to the smallest value, and then set up
Segmented compensation. When inputting the quantity of compensation
segments and the compensation length, do not make any . change, and
pressl]:j.direct.!):..,to skip. Enter into the interface for choosing compensation
method, press �-§to enter X axis to find the status of absolute zero.
Move die raster ruler towards the positive direction. When the absolute zero
is
found, it is the mechanical origin. The interior of digit display meter handles
automatically. At this time, directly press
!SJ
key to quit the Segmented
compensation setup, and finish finding the mechanical origin.(Remarks: It is
applicable
to
setting up parameters according to sketch map 2)
Note: When find the mechanical origin, the user-coordinate will resume.
Advise: ji11d the 111ec//a11ical origin before start work after power 011 to
assure
the
coordinate origin of
the
111aclti11e tool can match tile value in the
digit display
meter.
12
last lime
[ITI'f1ll?J] 0 [IUPiE!Ni.Jill
3) Key the new correction factor in:
0�0--��0
4) Key
IEJ
.
Iii b
• d in absolute display
N te· 'I'he linear error con1pensa!Ion can o y e carr1e
0
• mode (Ille message screen displays ALE) and metric
system:
12. Power Interruption Memory
.
.
th . may occur power interruptions
During the processing of a working. p
iec
�, eie
v'II automatically store the
or needed temporary turnoffs, th� digital dt�play box \ .1. displayed data and the
workillg stale (such as �he working m
ode
111 r:
v
:{eraXJ��terruption event Jn its
linear error compeusation factor) J�St !iefo
y · tl digital display box
E . fun when the machrne is turn on agam, ie
memory. ve1y
. e ki
tat J'ust before the interruption event after self
ill ecover to its wor ng s , e
·
·n
.
:1ec�ng, and the valve just before the interruption (turn off) event wr recover,
and !lie processing will continue.
13
Summary of Contents for ZX6350G
Page 1: ...DRILLING MILLING MACHINE OPERATION MANUAL ...
Page 13: ... 8 l f 00 1520 No 1 Rolling bearing position VI a D r 12 ...
Page 19: ......
Page 22: ...C Gear head 46 0 0 1 4 ctn 3 1 0 0 0 32 29 8 59 0 21 q _60 1 61 64 49 63 ...
Page 23: ...D Ho rizontal spindle 52 22 77 ...
Page 24: ... 11 J _ 10 9 8 12 I 13 r 1s 19 54 J Q 53 7 t3 6 0 E Gear box 21 20 23 ...
Page 25: ...F Changing speed part 21 19 24 ...
Page 30: ...NO NAME QUTY 61 SPRING I 62 SCREW 63 OIL POSITION 64 BOLT 29 ...
Page 35: ......
Page 37: ......
Page 39: ......
Page 40: ......
Page 45: ......