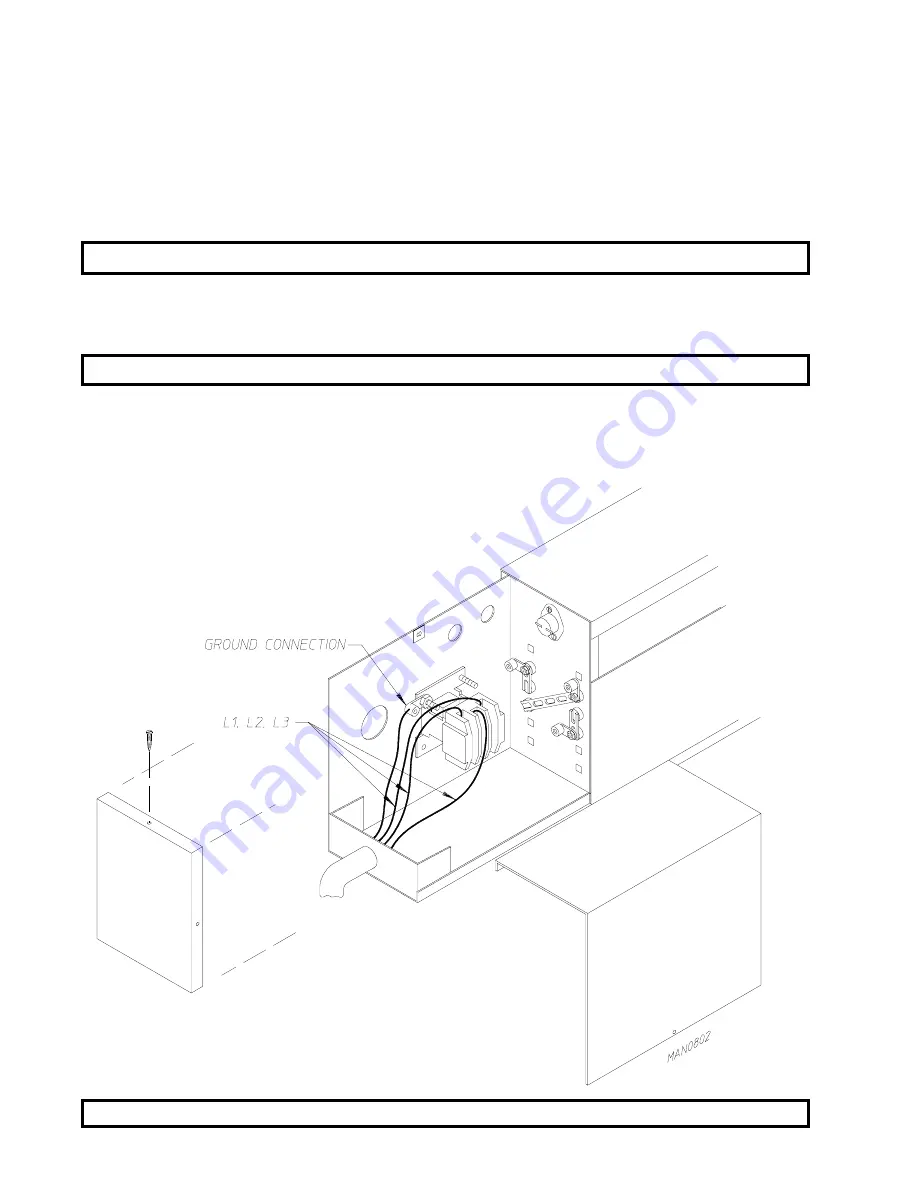
26
IMPORTANT
: A strain relief
must be
used where the input wiring enters the oven assembly.
b) ELECTRICALLY Heated Models Only
The only electrical input connections to the dryer are the 3-phase (3 Ø) power leads (L1,L2,L3
and sometimes neutral) and ground. Single phase power for the control circuit and for any
single phase (1 Ø) motors (if present) is done internally to the dryer by the factory at the
oven contactor. No single phase (1 Ø) input connection is required on a 3-phase (3 Ø)
dryer.
CAUTION
: The dryer
must be
grounded. A ground lug has been provided for this purpose.
Input connection wiring
must be
sized properly to handle the dryer's current draw. This
information is printed on the dryers data label.
IMPORTANT
: A separate circuit serving each dryer
must be
provided.
The electrical input connections are made at the electric oven contactor located inside the
assembly at the rear center upper section of the dryer. The ground connection is made to a
copper lug also provided in this area. To gain access, remove oven rear service cover.
Summary of Contents for ADE-75
Page 22: ...18...