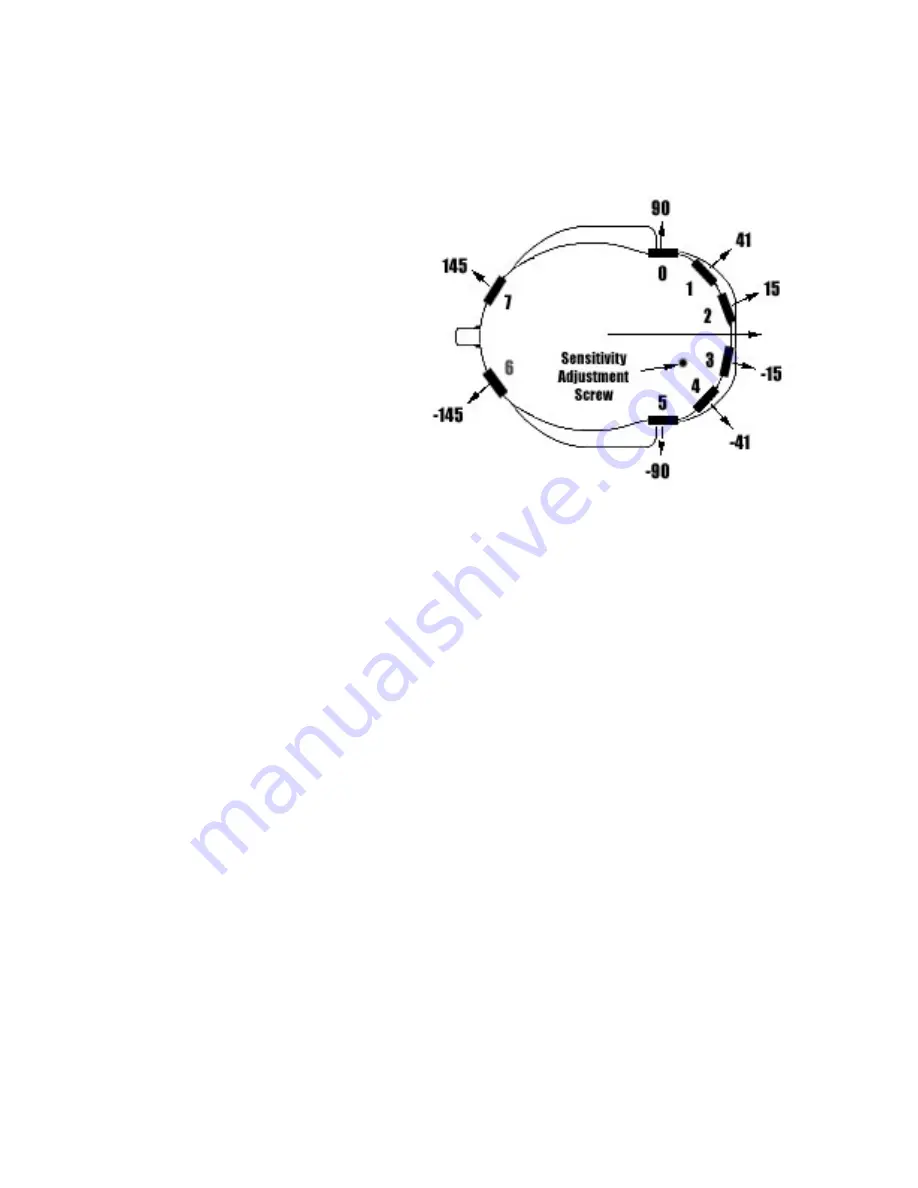
M
OBILE
R
OBOTS
S
ONAR
The AmigoBot comes standard with a single array of eight sonar. The sonar positions are
fixed: one on each side, four facing forward, and two at the rear, together providing
nearly 360 degrees of range sensing. The sonar are numbered clockwise around the
robot, beginning with the left side disc.
Sonar Rate and Sequence
The sonar array’s transducers
are multiplexed: Only one disc
is active at a time. The sonar
ranging acquisition rate is
adjustable, normally set to 25
Hertz (40 milliseconds per
transducer). Sensitivity ranges
from 10 centimeters (six inches)
up to five meters, depending on
the ranging rate. You may
control the sonar’s firing pattern
through software, too; the
default is left-to-right in
sequence 0 to 7 for each array.
See the AmigoSH Chapters 5
and 6 for details.
Figure 14. AmigoBot's sonar array
Sonar Sensitivity
All eight sonar are controlled from a single board. Although calibrated at the factory,
you may adjust the sonar sensitivity and range to accommodate differing AmigoBot
operating environments. The sonar gain control is a one-turn screwcap accessible
through a hole on the top and near the front of AmigoBot. You may have to remove an
accessory to uncover the hole.
Using a flat-bladed screwdriver, turn the adjustment screw counterclockwise to make the
sonar less sensitive to external noise and false echoes. Low sonar-gain settings reduce
the robot’s ability to see small objects. Under some circumstances, that is desirable. For
instance, attenuate the sonar if you are operating in a noisy environment or on uneven
or highly reflective floor
a heavy shag carpet, for example. If the sonar are too
sensitive, they will “see” the carpet immediately ahead of the robot as an obstacle.
Increase the sensitivity of the sonar array by turning the gain-adjustment screw clockwise,
making the sonar more likely to see small objects or objects at a greater distance. For
instance, increase the sonar gain if you are operating in a relatively quiet and open
environment with a smooth floor surface.
M
OTORS
, W
HEELS
,
AND
P
OSITION
E
NCODERS
AmigoBot’s tires are four inches (10.2cm) in diameter and made of soft, but firm rubber
for good traction and low compressibility. AmigoBot’s drive system uses high-speed,
high-torque, reversible-DC motors. Each drive motor includes a high-resolution optical
quadrature shaft encoder that provides 123 ticks per millimeter of wheel rotation for
precise position and speed sensing and advanced dead-reckoning.
Three FLASH-based parameters influence AmigoBot’s odometry:
RevCount
sets the
differential encoder ticks for 180 degrees of rotation which AmigoSH uses to compute
heading and speed of rotation.
TicksMM
is the number of ticks per millimeter of tire
13