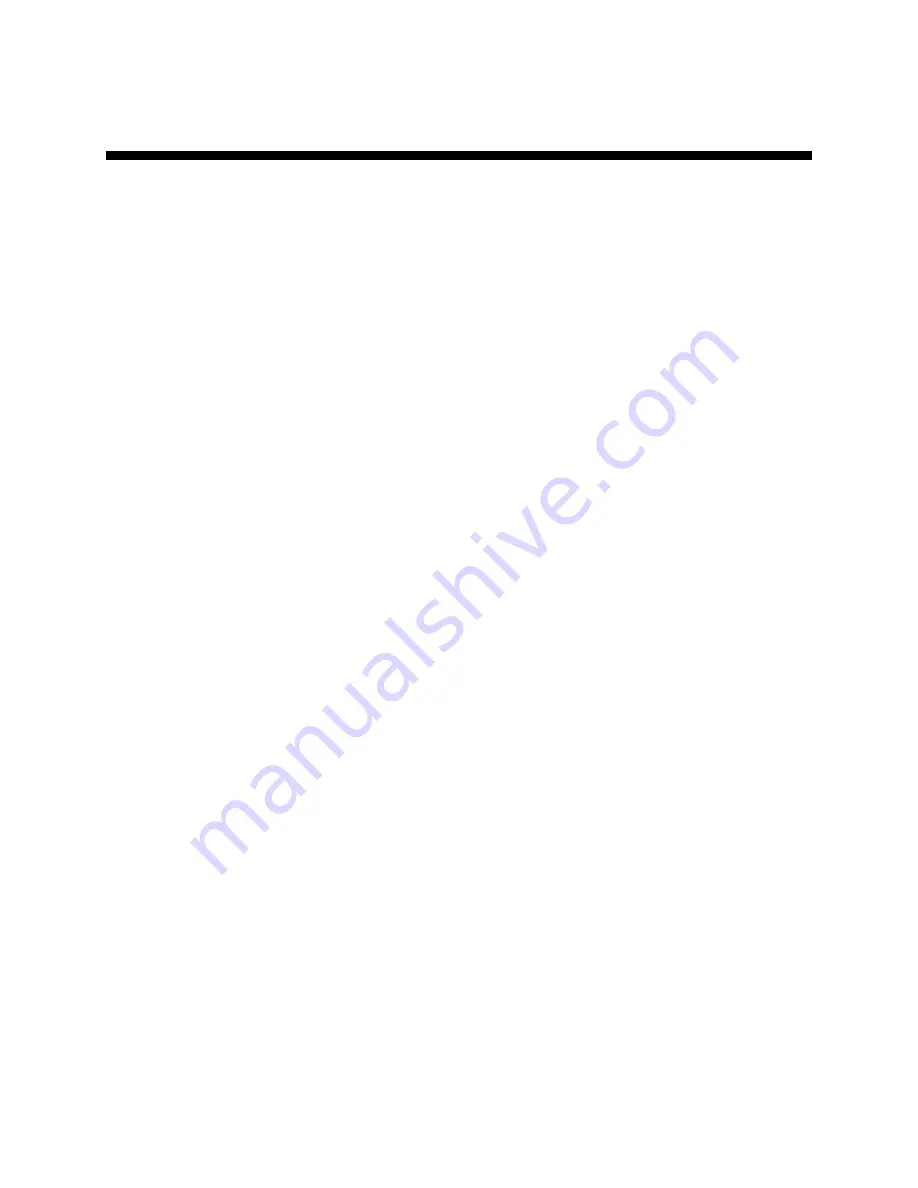
TC 120
682.98767.00 • 10/04/2018
iv
Table of Contents
CHAPTER 1:
SAFETY ................................................................ 7
1-1
How to Use This Manual ............................................................................................ 7
Safety Symbols Used in this Manual ................................................................... 7
1-2
General Safety Regulations ....................................................................................... 8
1-3
Responsibility ............................................................................................................ 8
1-4
Warnings and Precautions ....................................................................................... 11
CHAPTER 2:
FUNCTIONAL DESCRIPTION ........................... 14
2-1
Introduction .............................................................................................................. 14
2-2
Necessary Documents ............................................................................................. 14
2-3
Models Covered ...................................................................................................... 15
2-4
Standard TCU Series Features ................................................................................ 15
2-5
Available Options ..................................................................................................... 16
CHAPTER 3:
INSTALLATION .................................................. 18
3-1
Installation Location Considerations ........................................................................ 18
3-2
Process Approach Temperature Considerations ...................................................... 18
3-3
External Piping Sizing Considerations ..................................................................... 18
3-4
Piping Considerations for Permanent Installations ................................................... 18
3-5
Piping Considerations for High Mobility Installations ................................................ 19
3-6
Process Water Considerations................................................................................. 19
Raw Water .........................................................................................................19
Distilled Water ....................................................................................................20
Deionized Water ................................................................................................20
3-7
Making Process Water Connections ........................................................................ 20
Closed Circuit/Direct Injection ............................................................................20
TO PROCESS — 1½” NPT ................................................................................20
FROM PROCESS — 1½” NPT ..........................................................................20
3-8
Making Cooling Water Connections ......................................................................... 20
Water In — ¾” ...................................................................................................20
Water Out ..........................................................................................................21
Pressure Relief — ¾” .........................................................................................21
3-9
Making System Purge Connections ......................................................................... 21
3-10
Making Electrical Connections ................................................................................. 22
CHAPTER 4:
IDENTIFYING CONTROLS AND FEATURES ... 24
4-1
Identifying Mechanical Controls and Features ......................................................... 24
To Process Probe ..............................................................................................24
Safety Thermostat ..............................................................................................24
Pressure Relief Valve ........................................................................................24
Pumps ...............................................................................................................24
Heaters ..............................................................................................................25
Solenoid Valves .................................................................................................25
Motorized Modulating Valves .............................................................................25
Water Hammer Arrestor (Shock Stop) ................................................................25