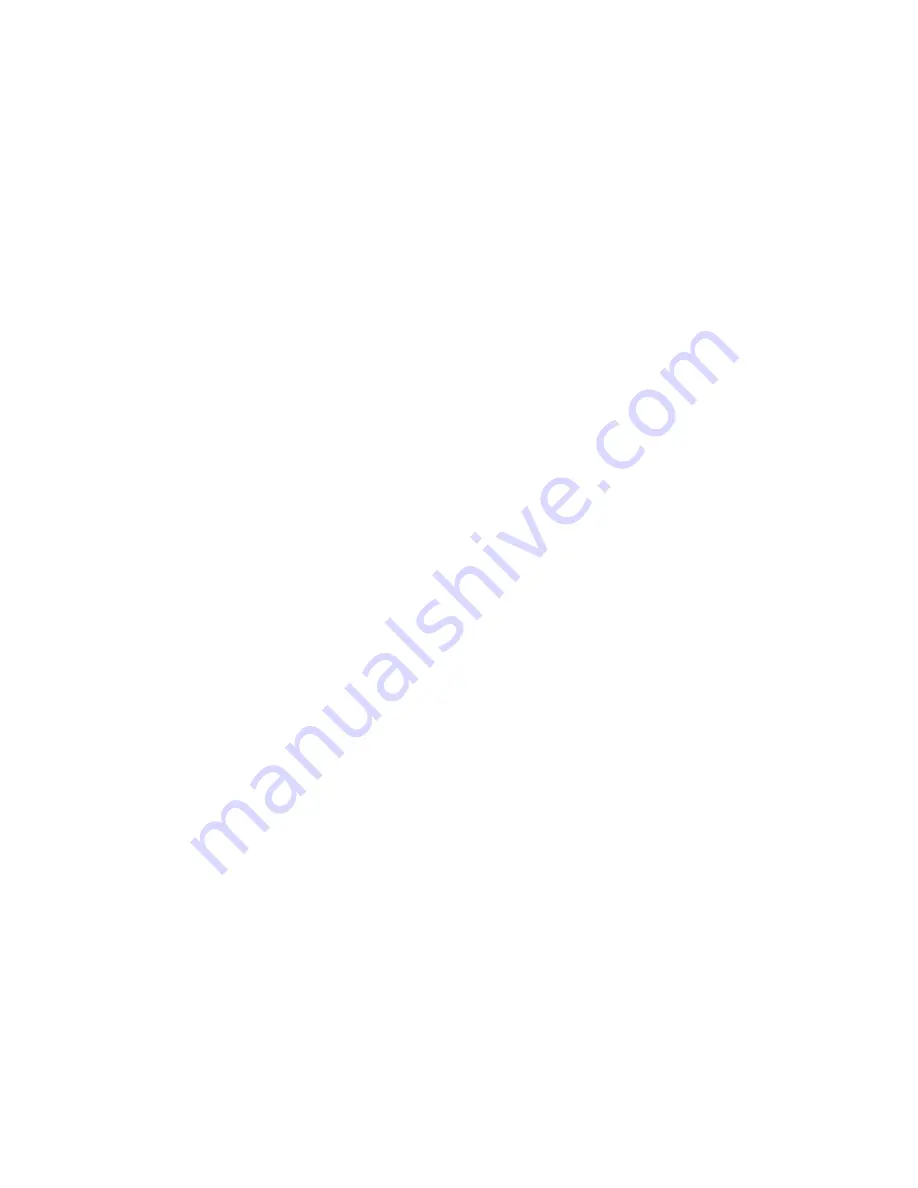
TC 120
682.98767.00 • 10/04/2018
37
6-2 Corrective Maintenance
Pumps and Seals
Before leaving our factory, we test each unit extensively, then we calibrate each unit.
Afterwards, the unit is drained and blown out with air to remove water from piping systems.
If the unit is allowed to stand idle for a long time before being installed in your factory, the
housing gasket at the pump can dry out and can possibly leak when the unit is started. In most
cases these gaskets will soon swell and form a tight seal. In other cases, it may be necessary
for you to tighten the pump bolts to stop a leaking condition.
Pump seal surfaces can separate slightly because of rough handling or from vibration during
transit. This could cause a leak at the pump seal when the pump is started, but in most cases
the surfaces will mate again after the pump is allowed to run for a short period of time. If they
do not reseal, you may need to open the pump and free the seal by hand. It is seldom
necessary to install a replacement seal in a new unit unless the seal has been damaged
because the unit was started without water.
Our pump seals have a long period of service life. Some conditions, of course, can shorten
seal life, including the presence of grit, operation of the unit without water, sustained high
water temperature, or presence of certain chemicals in the water. Our pump seal assembly has
been developed to resist abrasive particles that are present in many water systems. This is
done by a special flushing system that uses water exiting the pump to constantly wash the
seal area.
It is also fitted with high temperature flexible components for maximum heat resistance.
These same components remain flexible even at low temperatures. Thus, the standard seal is
a fine combination of heat resistant and wear resistant components. Unfortunately, even
under normal use, the seal will eventually wear and require replacement.
A small puddle underneath the unit is a sign of rotary seal wear, and if investigation confirms
the pump as the source, the seal should be replaced as soon as practical. The water slinger is
intended to provide temporary protection against this, but a continued and substantial leak
will ruin the motor bearing and cause further damage.
After the unit has been in service for a period of years where abrasive conditions are present,
you may find that the pump bracket (the top half of the pump casting), can be eroded away in
the area around the seat of the rotary seal. This area should provide a straight, smooth bearing
surface for the cup seal. Should your casting show signs of erosion in this area, the casting
needs to be replaced. The replacement cost of the casting is very modest compared to the
down time and maintenance cost for frequently replacing the seal.
Under some conditions, the pump may not start. After turning off the power supply, check the
motor shaft to be certain it is free to turn. By removing the drip cover on top of the motor,
you’ll have access to the end of the shaft. It has been slotted to make it easy to turn with a
screwdriver. If the shaft is free to turn, next check that the motor overloads are set, check for
blown fuses, and finally check the power supply on each leg to the motor. A qualified
electrician should check the motor and its circuit.