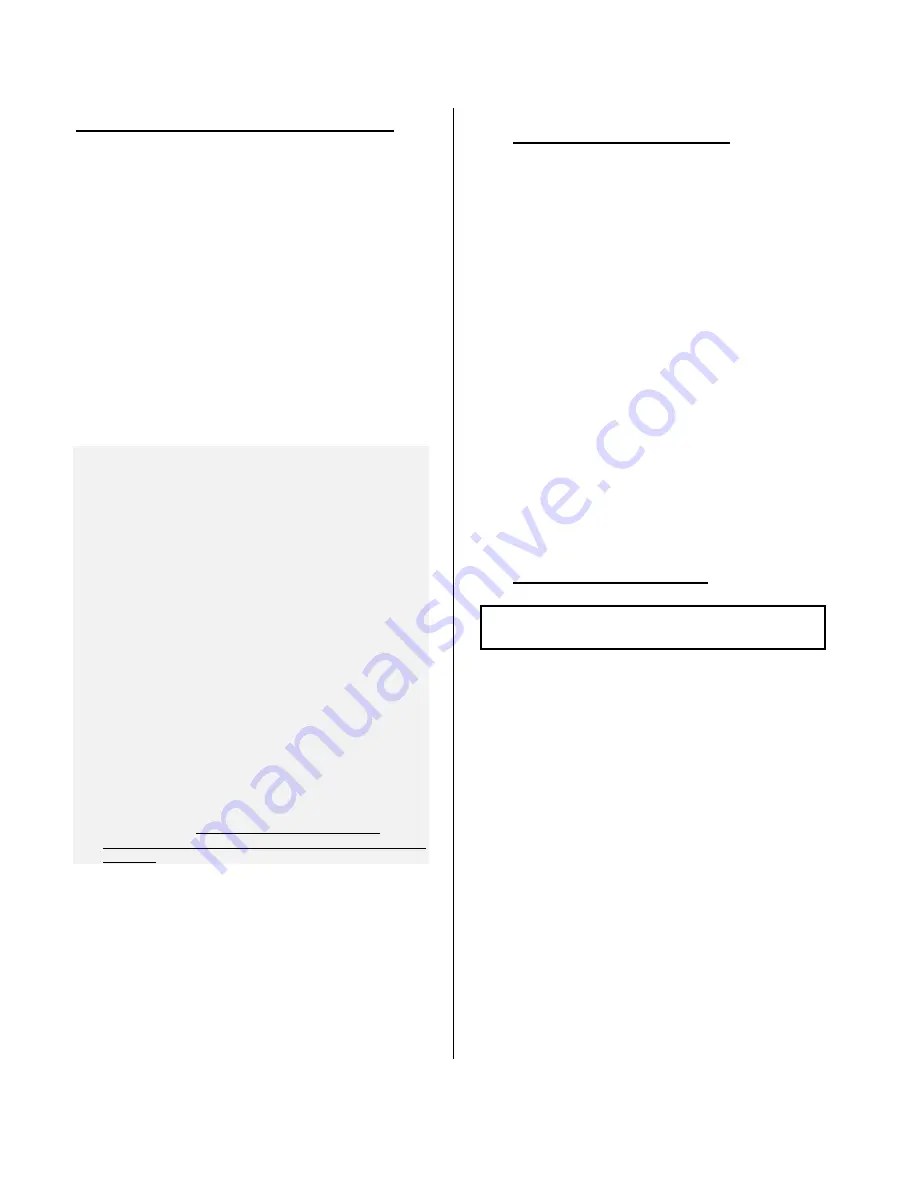
IntelliPack Series 801T Transmitter/Alarm User's Manual mV/TC/RTD Input
___________________________________________________________________________________________
- 7 -
Transmitter/Alarm Programming Procedure…continued
9. Press the
“UP”
or
“DOWN”
push-button once. Refer to
Functional Block Diagram 4501-689 and note that internally,
the output of the Range Adjust Box is now set for 100.0% for
the input full-scale value of 200
C. The transmitter will
adjust it’s output to the maximum output value (20.000mA).
If the output is not exactly at the full-scale level (20.000mA),
press the UP or DN switches continuously until the desired
output is achieved.
Note:
After first pressing the UP & DN
push-buttons, they will function as trim adjustments for the
output stage. The output trim adjustment should be limited
to
10%. Each successive depression of the “UP” or “DN”
switch will increment or decrement the output signal by a
small amount. Holding the switch depressed will increase
the amount of increment or decrement.
10. Press the
“SET”
push-button to accept the full-scale value.
Note that every time “SET” is pressed, the yellow “Status”
LED will flash once and the full-scale output will be captured.
11. If you are configuring an 801T-0500 model, which has no
alarm function, then you should skip steps 12-17 and jump
ahead to step 18.
12. Press the
“MODE”
push button one time until the yellow
zero/full-scale LED goes out and the yellow relay LED turns
ON (see Table 3). In this mode, the unit is ready to accept
an input setpoint level for the alarm. If you do not wish to
change the setpoint, skip to step 15.
Note:
The setpoint can be set to any value within the input
range selected regardless of the zero/full-scale settings.
For example, you can have a setpoint of 300
C with a
TC Type J transmitter calibrated for 0-200
C as its nominal
range is from -200
C to 760
C.
13. Adjust the input source to the High or Low alarm setpoint
level.
14. Press the
“SET”
push button to accept the setpoint. Note
that every time the “SET” button is pressed, the yellow
status LED will flash once and the value at the input will be
captured.
15. Press the
“MODE”
push button one time and the yellow
relay LED should start flashing (see Table 3). This means
that the unit is ready to accept the dropout level for the
alarm relay. If you do not wish to change the dropout, skip
to step 18.
16. Adjust the input source to the desired dropout level.
17. Press the
“SET”
push button to accept the input dropout
level. Note that every time the “SET” button is pressed, the
yellow status LED will flash once and the value at the input
will be captured. The module will use the difference
between the setpoint and dropout values to calculate relative
deadband.
18. Press the
“MODE”
push button one time to complete the
program sequence and return to run mode. The green
“RUN” LED will turn ON, the yellow “Zero/Full-Scale” LED
will be OFF, and the yellow alarm LED will be on or off
according to the alarm status. The module will now assume
a transfer function based on the zero and full-scale values
just set. The setpoint and dropout of 801T-1500 units is
used to determine the alarm deadband.
Note:
If no push-
buttons are depressed for a period greater than 3 minutes,
then the module will automatically revert to run mode (green
“Run” LED will light) and no changes will be made to the
original zero, full-scale, and optional setpoint & dropout
settings.
4.0 THEORY OF OPERATION
Refer to Simplified Schematic 4501-680 and Functional Block
Diagram 4501-689 to gain a better understanding of the circuit.
Note that these transmitters will accept a thermocouple, an RTD
sensor, or a voltage input, and condition it to a voltage signal for
the A/D converter. The A/D converter stage then applies
appropriate gain to the signal, performs analog-to-digital
conversion, and digitally filters the signal. The digitized signal is
then transmitted serially to a microcontroller. The microcontroller
completes the transfer function according to the transmitter type
and its embedded function, and sends a corresponding output
signal to an optically isolated Digital-to-Analog Converter (DAC).
The DAC then updates its current or voltage outputs in response.
The microcontroller also compares the signal value to the limit
value according to the alarm type and completes all necessary
alarm functions per its embedded program (801T-1500 units
only). The embedded configuration and calibration parameters
are stored in non-volatile memory integrated within the micro-
controller. Only the functions required by an application are
actually stored in memory
—new functionality can be downloaded
via the IntelliPack Configuration Program and Serial Port Adapter.
A wide input switching regulator (isolated flyback mode) provides
is5V power to the circuit, plus an is15V output
circuit supply. Refer to Functional Block Diagram 4501-689 for
an overview of how the software/push-button configuration
variables are arranged.
5.0 SERVICE AND REPAIR
CAUTION:
Risk of Electric Shock - More than one
disconnect switch may be required to de-energize the
equipment before servicing.
SERVICE AND REPAIR ASSISTANCE
This module contains solid-state components and requires no
maintenance, except for periodic cleaning and transmitter
configuration parameter (zero, full-scale, setpoint, deadband, etc)
verification. Since Surface Mounted Technology (SMT) boards
are generally difficult to repair, it is highly recommended that a
non-functioning module be returned to Acromag for repair. The
board can be damaged unless special SMT repair and service
tools are used. Further, Acromag has automated test equipment
that thoroughly checks and calibrates the performance of each
module. Please refer to Acromag’s Service Policy Bulletin or
contact Acromag for complete details on how to obtain service
parts and repair.
PRELIMINARY SERVICE PROCEDURE
Before beginning repair, be sure that all installation and
configuration procedures have been followed. The unit routinely
performs internal diagnostics following power-up or reset. During
this period, all LED’s will turn ON momentarily, and the green
“Run” LED flashes. If the diagnostics complete successfully, the
“Run” LED will stop flashing after approximately one second and
remain ON. This indicates that the unit is operating normally. If
the “Run” LED continues to flash, then this is indicative of a
problem.