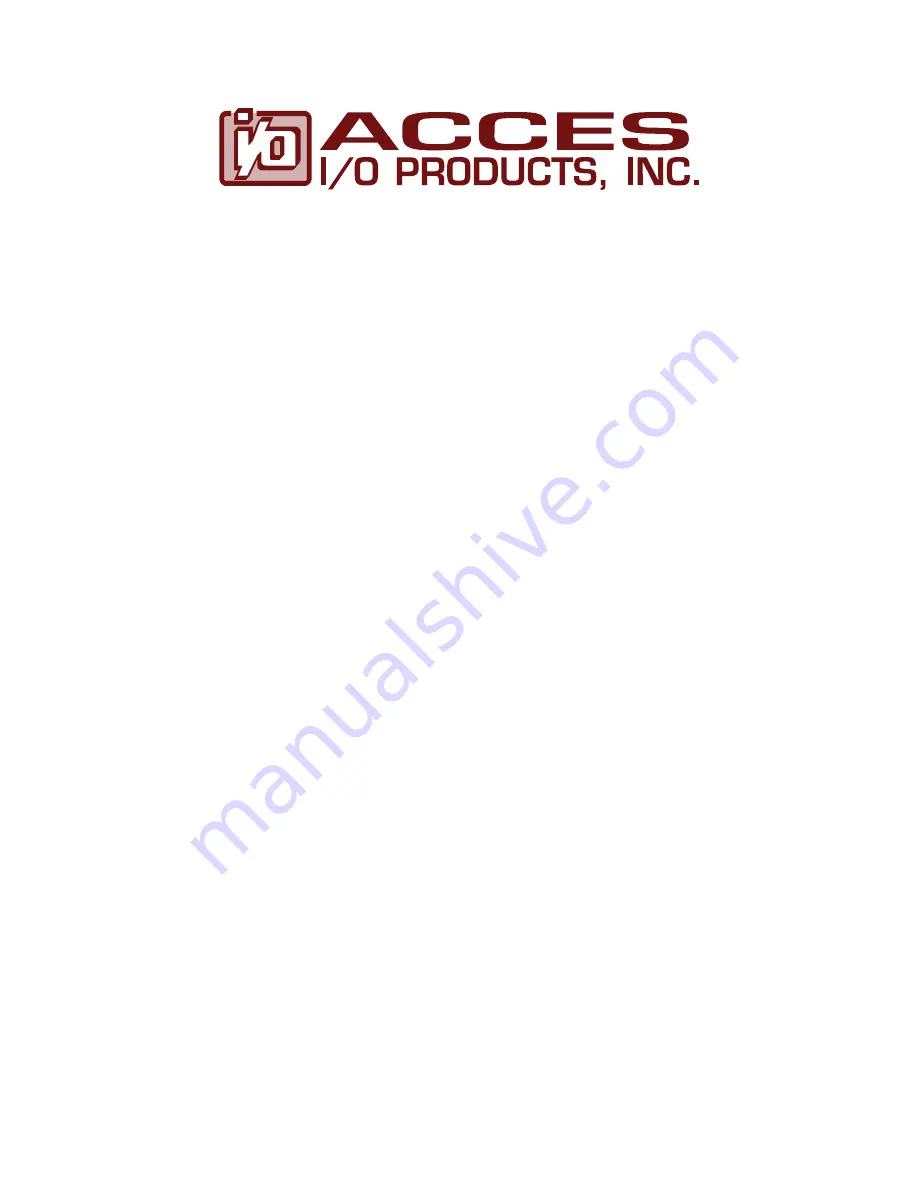
10623 Roselle Street, San Diego, CA 92121 (858) 550-9559 Fax (858) 550-7322
[email protected] www.accesio.com
104-AIO16A and 104-AIO16E
PC/104 HIGH-PERFORMANCE ANALOG
I/O BOARDs
USER MANUAL
M104-AIO16A.A1k