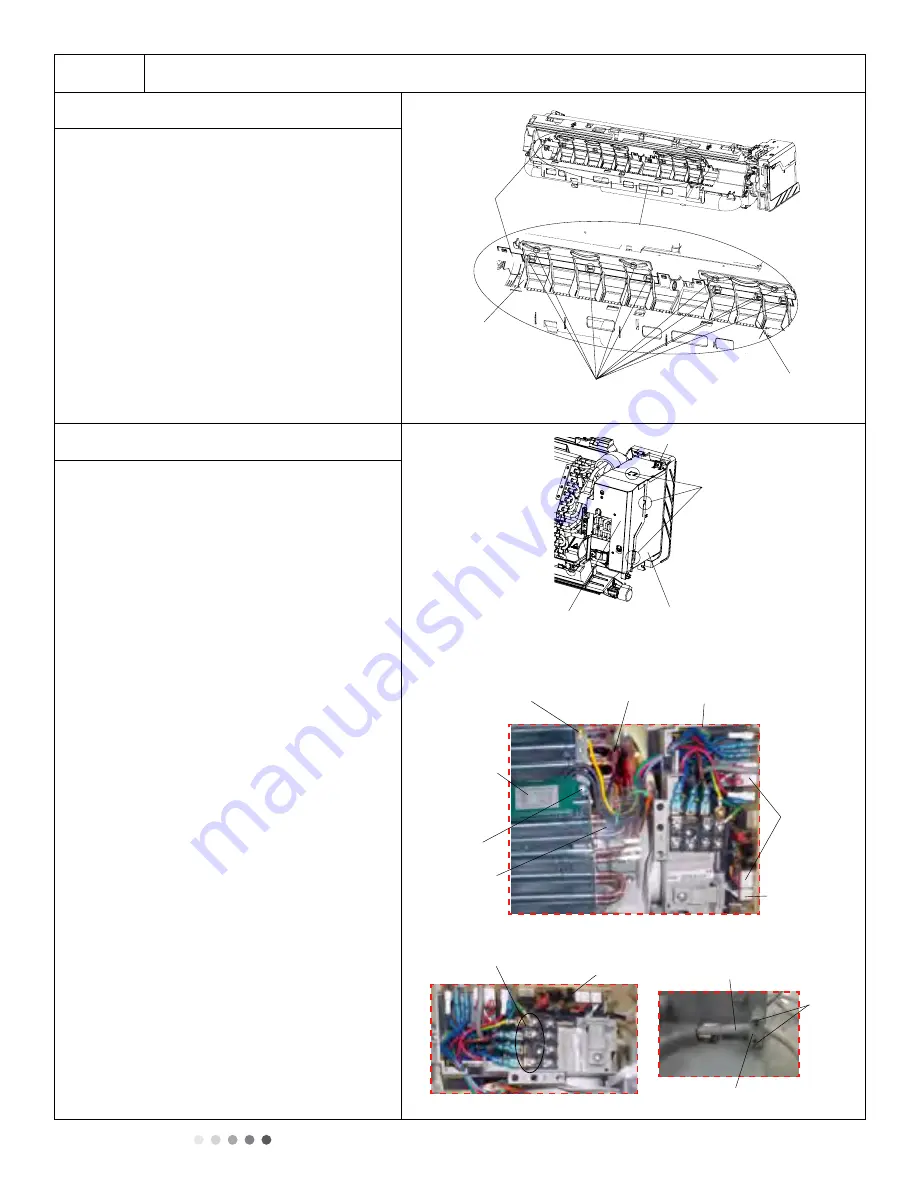
34
Technical Information
Step
Procedure
7. Remove vertical louver
Loosen connection clasps between vertical
louver and bottom case to remove vertical
louver.
8. Remove electric box assy
a. Loosen connection clasps between shield
cover of electric box sub-assy and electric
box, then remove shield cover of electric
box sub-assy. Remove screw fixing
electric box assy .
b. Take off water retaining sheet.
i. Remove cold plasma generator by
unscrewing locking screw on generator.
ii. Take off indoor tube temperature sensor.
iii. Remove grounding screw.
iv. Remove wiring terminals of motor and
stepping motor.
v. Remove electric box assy.
c. Twist off screws that are locking each lead
wire and rotate the electric box assy.
Twist off screws that are locking the wire
clip. Loosen power cord and remove its
wiring terminal. Lift up the main board
and remove it.
93
Installation and Maintenance
Service Manual
a
b
c
Procedure
Steps
Loosen the connection clasps between
shield cover of electric box sub-assy and
electric box, and then remove the shield
cover of electric box sub-assy.
Remove the screw fixing electric box assy .
①
Take off the water retaining sheet.
Remove the cold plasma generator by
screwing off the locking screw on the
generator.
②
Take off the indoor tube temperature
sensor.
③
Screw off 1 grounding screw.
④
Remove the wiring terminals of motor and
stepping motor.
⑤
Remove the electric box assy.
Twist off the screws that are locking
each lead wire and rotate the electric
box assy.
Twist off the screws that are locking the
wire clip. Loosen the power cord and
remove its wiring terminal. Lift up the
main board and take it off.
8. Remove electric box assy
Electric box
Electric box assy
Clasps
S
hield cover of electric
box sub-assy
Cold plasma
generator
Water retaining
sheet
Grounding screw
Screw
Power cord
Wire clip
Screws
Main board
Screw
Indoor tube
temperature
sensor
Wiring
terminal
of motor
Wiring
terminal
of stepping
motor
Screw
Vertical
louver
Vertical
louver
Clasps
Bottom
case
Loosen the connection clasps between
vertical louver and bottom case to remove
vertical louver.
7. Remove vertical louver
93
Installation and Maintenance
Service Manual
a
b
c
Procedure
Steps
Loosen the connection clasps between
shield cover of electric box sub-assy and
electric box, and then remove the shield
cover of electric box sub-assy.
Remove the screw fixing electric box assy .
①
Take off the water retaining sheet.
Remove the cold plasma generator by
screwing off the locking screw on the
generator.
②
Take off the indoor tube temperature
sensor.
③
Screw off 1 grounding screw.
④
Remove the wiring terminals of motor and
stepping motor.
⑤
Remove the electric box assy.
Twist off the screws that are locking
each lead wire and rotate the electric
box assy.
Twist off the screws that are locking the
wire clip. Loosen the power cord and
remove its wiring terminal. Lift up the
main board and take it off.
8. Remove electric box assy
Electric box
Electric box assy
Clasps
S
hield cover of electric
box sub-assy
Cold plasma
generator
Water retaining
sheet
Grounding screw
Screw
Power cord
Wire clip
Screws
Main board
Screw
Indoor tube
temperature
sensor
Wiring
terminal
of motor
Wiring
terminal
of stepping
motor
Screw
Vertical
louver
Vertical
louver
Clasps
Bottom
case
Loosen the connection clasps between
vertical louver and bottom case to remove
vertical louver.
7. Remove vertical louver