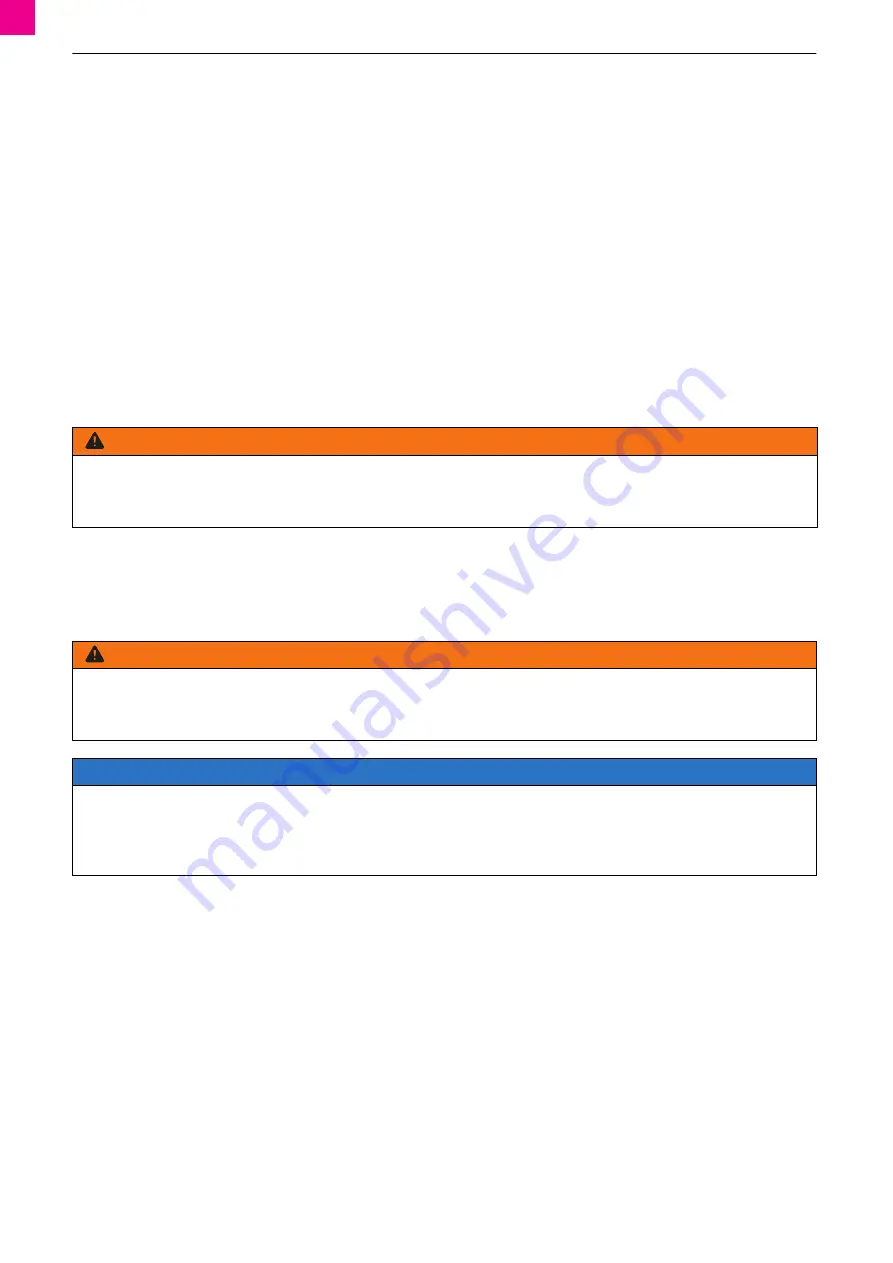
EN
-
8
5 Operation
ABITIG
®
GRIP, ABITIG
®
GRIP AT/WT
4.7
Connecting the coolant hoses
1
Connect the coolant supply (blue) and coolant return (red).
2
Check the coolant’s minimum fill level.
► Recommendation: use ABICOR BINZEL coolants from the BTC range.
► To prevent damage to the welding device, do not use deionised or
demineralised water.
► Bleed the coolant circuit upon commissioning and when replacing the
cable assembly.
4.8
Bleeding the coolant circuit
1
Place the collection receptacle under the connection for the coolant
return (red).
2
Disconnect the coolant return hose from the cooling unit and hold it over
collection receptacle.
3
Seal the coolant return hose’s opening.
4
Abruptly open then seal the coolant return hose’s opening several times
until the coolant flows into the collection receptacle continuously and
without air bubbles.
5
Reconnect the coolant return hose to the cooling unit.
4.9
Connecting the shielding gas and setting the gas volume
The type and amount of shielding gas used depend on the welding task and
the gas nozzle geometry.
1
Select the appropriate shielding gas for the welding task.
2
Briefly open the valve on the gas supply then close it again to air-blast
away any dirt on the connector.
3
Connect the shielding gas to the welding device as per the
manufacturer’s instructions.
4
Adjust the shielding gas volume to the gas nozzle used and the welding
task and save the setting.
5 Operation
5.1
Handle operating elements
The trigger’s two-step operating mode can be activated when using a
standard welding torch.
Further operating modes and handle modules depend on the welding power
source and must be ordered separately.
5.2
Replacing the torch neck, Fig. 5
1
Switch off the welding power source.
2
Close the shielding gas cylinder.
3
Hold the liquid-cooled welding torch pointing downwards to prevent
the penetration of coolant.
4
Have a cloth ready to catch any coolant that escapes.
5
To loosen the torch neck, twist the nut 1.5 rotations to the left.
Do not twist the torch neck as this may damage it.
6
Remove the torch neck.
7
Insert another torch neck.
8
To tighten the torch neck, twist the nut 1.5 rotations to the right.
9
Check that the torch neck is secure.
5.2.1
Inserting a plug to block residual coolant and dirt, Fig. 6
► If the welding torch is not required, insert the plug provided into
the handle.
5.3
Welding
1
Open the shielding gas cylinder.
2
Switch on the welding power source.
3
Switch on the cooling unit.
4
Rinse the shielding gas lines.
5
Set the welding parameters.
6
Press and hold the trigger on the handle = start welding.
7
After ignition, hold the welding arc over the workpieces to be welded
without any longitudinal movement until a molten pool is formed.
8
Move the welding torch uniformly over the entire seam length.
9
Release the trigger on the handle = stop welding.
10
After switching off the welding torch, hold it over the end position for
a few seconds. The residual gas flow allows the molten pool to solidify
without external interference.
WARNING
Risk of injury due to electromagnetic fields
The device can produce electromagnetic fields that could impact the proper function of cardiac pacemakers and implanted defibrillators.
► Do not use the device if you have a pacemaker or an implanted defibrillator.
► Only use the device in industrial zones in accordance with DIN EN 61000
-
6
-
3.
WARNING
Risk of burns from hot surface
Welding torches become very hot during welding. This may result in serious burns.
► Allow welding torches to cool down after welding.
► Wear the correct protective gloves.
NOTICE
Material damage due to residual coolant and dirt
Residual coolant and dirt in the gas hole can cause the formation of pores, entrapped air and dirt in the welding seam.
► Ensure that no residual coolant enters the gas hole.
► To prevent the penetration of residual coolant, hold the welding torch handle pointing downwards when unscrewing the torch neck.
► To prevent coolant from escaping and dirt from getting into the device, use a sealing plug to seal the welding torch handle when not in use.
Summary of Contents for ABITIG GRIP
Page 2: ...2 ABITIG GRIP ABITIG GRIP AT WT 1 1 2 3 2 1 1 2 2 3 4 A B C D E 5 1 2 6 F...
Page 11: ...ABITIG GRIP ABITIG GRIP AT WT 9 Gew hrleistung DE 11...
Page 19: ...ABITIG GRIP ABITIG GRIP AT WT 9 Warranty EN 11...
Page 27: ...ABITIG GRIP ABITIG GRIP AT WT 9 Garantie FR 11...
Page 35: ...ABITIG GRIP ABITIG GRIP AT WT 9 Garant a ES 11...