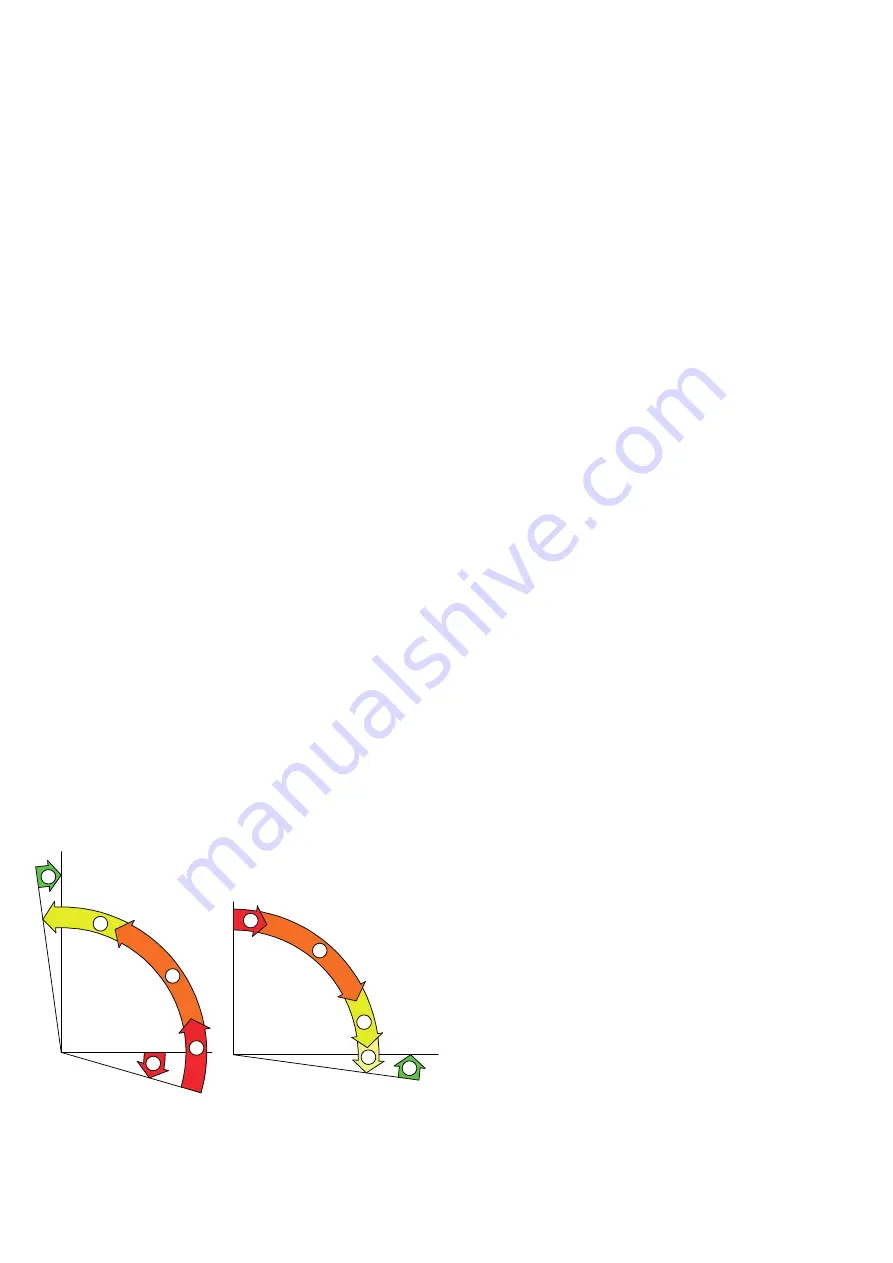
C1
C5
C4
C3
C2
A2
A1
A3
A4
A5
OPENING
CLOSING
OTHER PARAMETERS USED DURING THE MOVEMENT
OF MENU-MODIFIED MOTORS:
PHASES OF MANEUVER IN OPENING:
A1 = REVERSE STROKE (before the opening movement, at
full power)
A2 = INITIAL START (selectable by ramp or step at full power)
A3 = QUICK MOVEMENT (adjustable speed acting on RAPID
PWM)
A4 = SLOW MOVEMENT (adjustable speed acting on SLOW
PWM)
A5 = BACKJUMP (backward leap) at the opening at the end of
the maneuver.
C1 = KICKSTART (selectable by ramp or step at full power)
C2 = QUICK MOVEMENT (adjustable speed acting on RAPID
PWM)
C3 = SLOW MOVEMENT (adjustable speed acting on SLOW
PWM)
C4 = EXTRA MOVEMENT
C5 = BACKJUMP (backward jump) in closing at the end of the
maneuver
TIPS ON HOW TO SET THE PARAMETERS:
- Adjust the rapid POWER according to the speed and thrust
you want on the door in fast movement
- Adjust the slow POWER according to the slowdown speed
you want
- Adjust the automation as "VERTICAL" if you want to set
g
n
i
s
o
l
c
d
n
a
g
n
i
n
e
p
o
r
o
f
s
e
u
l
a
v
R
E
W
O
P
t
n
e
r
e
ff
i
d
- Set a few seconds of EXTRA MOVEMENT if the automation
requires that the motor be powered for a few seconds more at
the end of the closing maneuver.
- Set a backjump of a few tenths of a second if you want the
leaf to move away from the closing bar at the end of the
movement.
- Use the REVERSE STROKE if a lock is installed on the door.
- Adjust the type and duration of the KICKSTART (by ramp for
a smooth and regular movement of the leaf or in step at full
power if the motor has difficulty moving the leaf in the initial
phase of the movement).
During travel programming, the control unit calculates the correct
t
h
g
i
e
w
e
h
t
d
n
a
d
e
s
u
r
o
t
o
m
c
ir
t
c
e
l
e
f
o
e
p
y
t
e
h
t
n
o
d
e
s
a
b
s
e
u
l
a
v
and inertia of the barrier.
It is however possible to enter the OBSTACLES menu to modify
the parameters with which the control unit recognizes the
presence of obstacles.
It is possible to use the MONITOR menu to check the encoder
current and frequency during opening and closing e
then select appropriate threshold values.
The obstacle is detected by the control unit only if the current rises
beyond a certain threshold value for a time T greater than the time
of hysteresis.
By raising and lowering the threshold value (differentiated for slow
and fast for motor 1 and motor 2) it is possible to make the
automation more or less sensitive to obstacles.
By raising the hysteresis time it is possible to set the control unit
so that it ignores small obstacles, by lowering the hysteresis value
on the contrary it is possible to speed up the recognition of
obstacles.
Obstacles menu
Inputs Menu
Icommands START1 and START2 can be set as:
- START / OPEN: the ST1 input sends a START command, ST2
an OPEN command
- START / CLOSE: the ST1 input sends a START command, ST2
a CLOSE command
- START / PEDESTRIAN: input ST1 sends a START command,
ST2 a PEDESTRIAN opening command
- CLOSE / OPEN: the ST1 input sends a CLOSE command, ST2
an OPEN command
- CLOSE UP / OPEN: the ST1 input sends a CLOSE command to
dead-man, ST2 an OPEN command
-> TRAFFIC LIGHT <: the ST1 input activates the LAMP output
for a time equal to the COURTESY TIME, blocking the ST2 input
for the entire power-up time, the ST2 input activates the AUX
output for a time equal to the TIME OF COURTESY blocking for
all
switch-on time the ST1 input.
The ST1 and ST2 inputs no longer operate the automation that
remains controllable by radio control, see ADDENDUM A2
-> PARKING <: input ST1 and ST2 are used to detect entry and
exit from the parking lot, see ADDENDUM A3
DEACTIVATE FT1: deactivates the photocell FT1
DEACTIVATE FT2: deactivates the FT2 photocell
DEACTIVATE STOP: disable the STOP input
DEACTIVATE ST1: deactivates the START1 input
DEACTIVATE ST2: deactivates the START2 input
FT1 SECTIONAL DOORS: deactivates the FT1 photocell only
during the slowing down phase in closing
PARTIAL OPENING: allows you to select the partial opening
percentage (winter or summer automatic door opening)
PANIC OPENING: allows automatic opening in the event of a
power failure (not yet available!)
ENCODER SQUARE: select [YES] if you want to connect the 2
signals of a two-channel encoder to inputs FC1 and FA1
in quadrature, select [NO] in all other cases.
AUTOMATIC DOOR KEYPAD ENABLE: select YES to enable the
reception of codes for remote control of the
automatic door, see ADDENDUM A1
PANIC: it is possible to set a minimum supply voltage (V. MIN)
below which an opening command is sent to the automation.
7