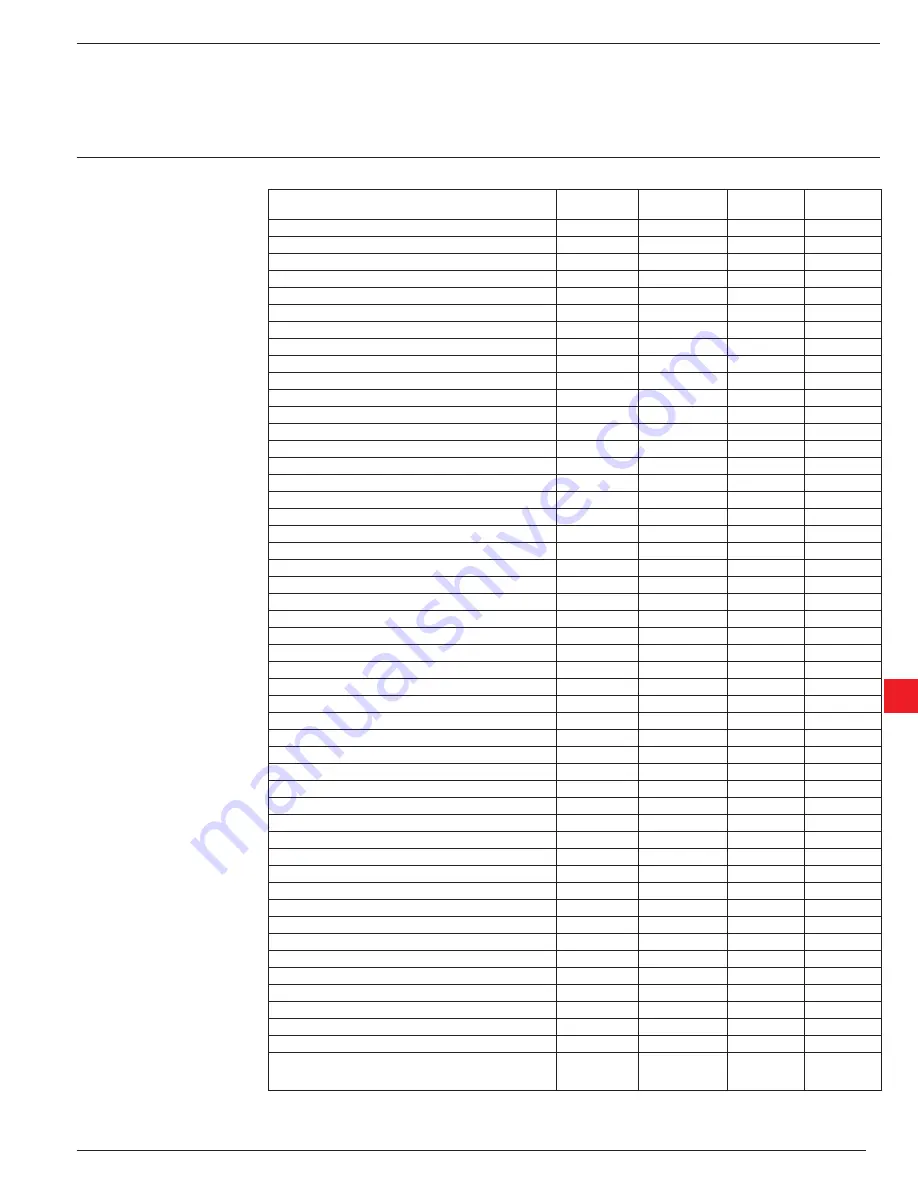
7:1.1 Overview of all accessible settings (different menus) cont.
Description
Display
text
Setting
range
Default
value
Actual
setting
Setting current
Setting Ie
9.0...1207A
Individual
Time for start ramp
Start Ramp
1...30s, 1...120s
10s
Time for stop ramp
Stop Ramp
0...30s, 0...120s
0s
Initial voltage for start ramp
Init Volt
30...70%
30%
End voltage for stop ramp
End Volt
30...70%
30%
Step down voltage
Step down
30...100%
100%
Level of the current limit
Current Lim
2.0...7.0xle
4.0xle
Selection of kick start
Kick Start
Yes, No
No
Level of kick start
Kick Level
50...100%
50%
Time for kick start
Kick Time
0.1...1.5s
0.2s
Range for start ramp
Start Range
1-30s, 1-120s
1-30s
Range for stop ramp
Stop Range
0-30s, 0-120s
0-30s
Overload protection
Overload
No, Normal, Dual
Normal
Overload class
OL Class
10A, 10, 20, 30
10
Overload class, Dual type, Start class
OL Class S
10A, 10, 20, 30
10
Overload class, Dual type, Run class
OL Class R
10A, 10, 20, 30
10
Type of operation for overload protection
OL Op
Stop-M, Stop-A, Ind
Stop-M
Locked rotor protection
Locked Rotor
Yes, No
No
Trip level for locked rotor protection
Lock R Lev
0.5...8.0xle
4.0xle
Trip time for locked rotor protection
Lock R Time
0.2...10s
1.0s
Type of operation for locked rotor protection
Lock R Op
Stop-M, Stop-A, Ind
Stop-M
Underload protection
Underload
Yes, No
No
Trip level for underload protection
Underl Lev
0.4...0.8xle
0.5xle
Trip time for underload protection
Underl Time
1...30s
10s
Type of operation for underload protection
Underl Op
Stop-M, Stop-A, Ind
Stop-M
Phase imbalance protection
Phase Imb
Yes, No
No
Trip level for phase imbalance protection
Ph Imb Lev
10...80%
80%
Type of operation for imbalance protection
Ph Imb Op
Stop-M, Stop-A, Ind
Stop-M
High current protection
High I
Yes, No
No
Type of operation for high current protection
High I Op
Stop-M, Stop-A, Ind
Stop-M
Phase reversal protection
Phase Rev
Yes, No
No
Type of operation for phase reversal protection
Ph Rev Op
Stop-M, Stop-A, Ind
Stop-M
PTC protection
PTC
Yes, No
No
Type of operation for PTC protection
PTC Op
Stop-M, Stop-A, Ind
Stop-M
Use of external by-pass contactor
Ext ByPass
Yes, No
No
Type of operation, by-pass doesn’t open
BP Closed Op
Stop-M, Stop A
Stop-M
Type of operation, by-pass doesn’t close
BP Open Op
Stop-M, Stop A
Stop-M
High current warning
Warn I=High
Yes, No
No
Trip level for high current warning
Wa I=H Lev
0.5...5.0xle
1.2xle
Low current warning
Warn I=Low
Yes, No
No
Trip level for low current warning
Wa I=L Lev
0.4...1.0xle
0.8xle
Motor overload warning
Warn OL
Yes, No
No
Trip level for motor overload warning
Wa OL Lev
40...99%
90%
Thyristor overload warning
Warn SCR OL
Yes, No
No
Type of operation for phase loss fault
Ph Loss Op
Stop-M, Stop-A
Stop-M
Type of operation for fieldbus fault
FB Fault Op
Stop-M, Stop-A
Stop-M
Type of operation for frequency fault
Freq F Op
Stop-M, Stop-A
Stop-M
Type of operation for heatsink overtemp fault
HS Temp Op
Stop-M, Stop-A
Stop-M
Type of operation for shorted thyristor fault
SCR SC Op
Stop-M, Stop-A
Stop-M
Function of programmable input In0
In0
None, Reset,
Enable Jog, DOL,
Start 2, FB-Dis
Reset
Chapter 7
Settings and configuration
Low Voltage Products & Systems
7.5
ABB nc. • 888-385-1221 • www.abb-control.com
1SXU 132 021 M0201
7