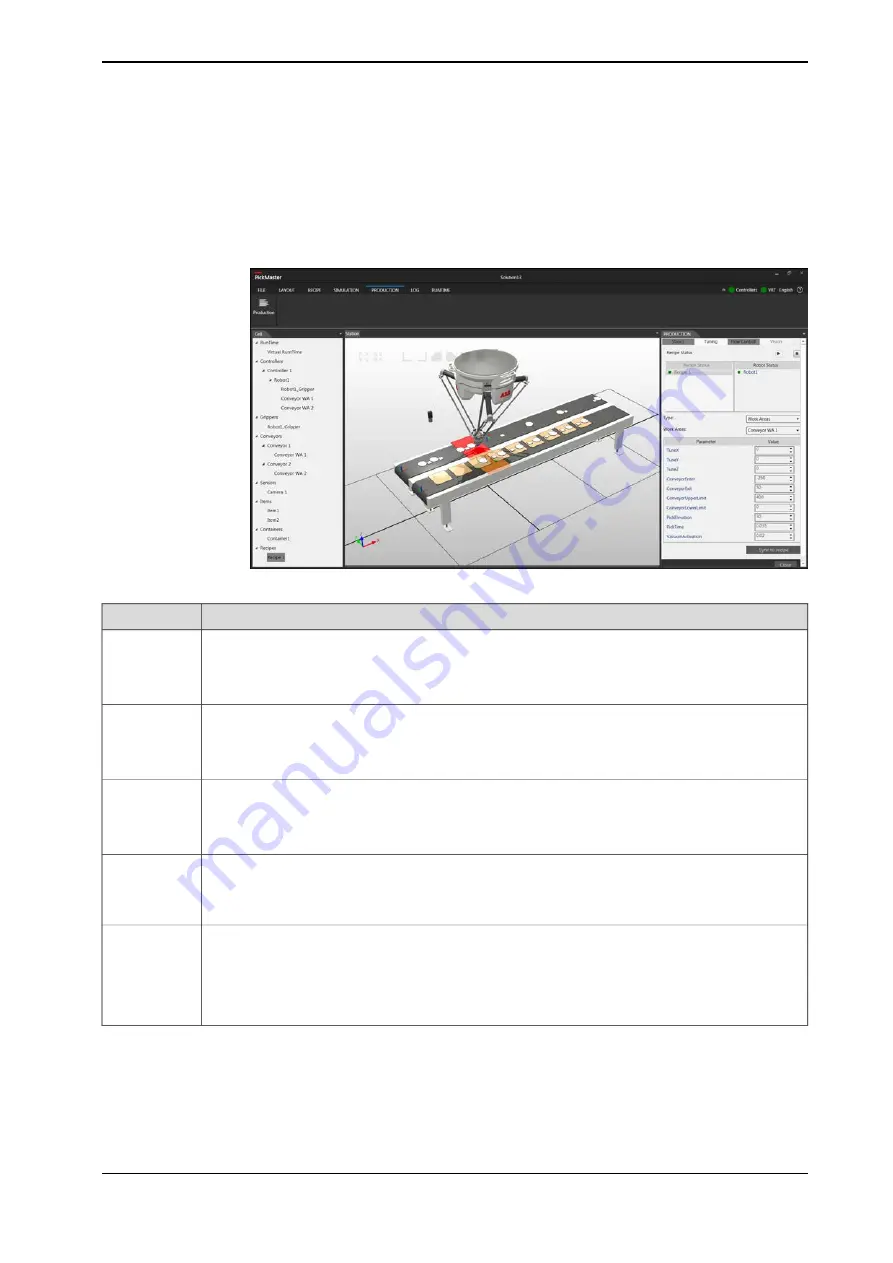
It is important to define a correct calibration tool when calibrating the base
frame of the conveyor, so the orientation in relation to the items grip point
(place/pick) will be correct. It is also important to do the camera calibration
at the same height as the item’s grip point, that is vision model grip point.
Tuning the work area
xx1900000595
Description
Allows you to tune the position of the work area along the X direction when running simulation or
production.
TuneX
Tuning the position of the work area along the X direction is equivalent to offsetting the conveyor
base frame along the X direction.
Allows you to tune the position of the work area along the Y direction when running simulation or
production.
TuneY
Tuning the position of the work area along the Y direction is equivalent to offsetting the conveyor
base frame along the Y direction.
Allows you to tune the position of the work area along the Z direction when running simulation or
production.
TuneZ
Tuning the position of the work area along the Z direction is equivalent to offsetting the conveyor
base frame along the Z direction.
Enter
is the limit from where the robot starts to execute item targets on the work area. The distance
is calculated in millimeters from the center of the robot. The range is positive if the limit is beyond
the center of the robot, relative to the moving direction of the conveyor. Make sure that the enter
limit can be reached by the robot.
ConveyorEnter
Exit
is the limit from where the robot considers an item target as lost on the work area. The distance
is calculated in millimeters from the center of the robot. The range is positive if the limit is beyond
the center of the robot, relative to the moving direction of the conveyor. When the tracked item
passes beyond this limit it will be dropped. This limit must be chosen well within the maximum
reach of the robot. The robot must be able to reach this position from an arbitrary position in the
robot’s working area before the position is out of reach.
ConveyorExit
Continues on next page
Application manual - PickMaster® Twin - PowerPac
163
3HAC064218-001 Revision: B
© Copyright 2021 ABB. All rights reserved.
4 Working with PickMaster PowerPac
4.2.12 Simulation
Continued
Summary of Contents for PickMaster Twin - PowerPac
Page 1: ...ROBOTICS Application manual PickMaster Twin PowerPac ...
Page 8: ...This page is intentionally left blank ...
Page 12: ...This page is intentionally left blank ...
Page 16: ...This page is intentionally left blank ...
Page 420: ...This page is intentionally left blank ...
Page 444: ...This page is intentionally left blank ...
Page 446: ...This page is intentionally left blank ...
Page 448: ...This page is intentionally left blank ...
Page 452: ......
Page 453: ......