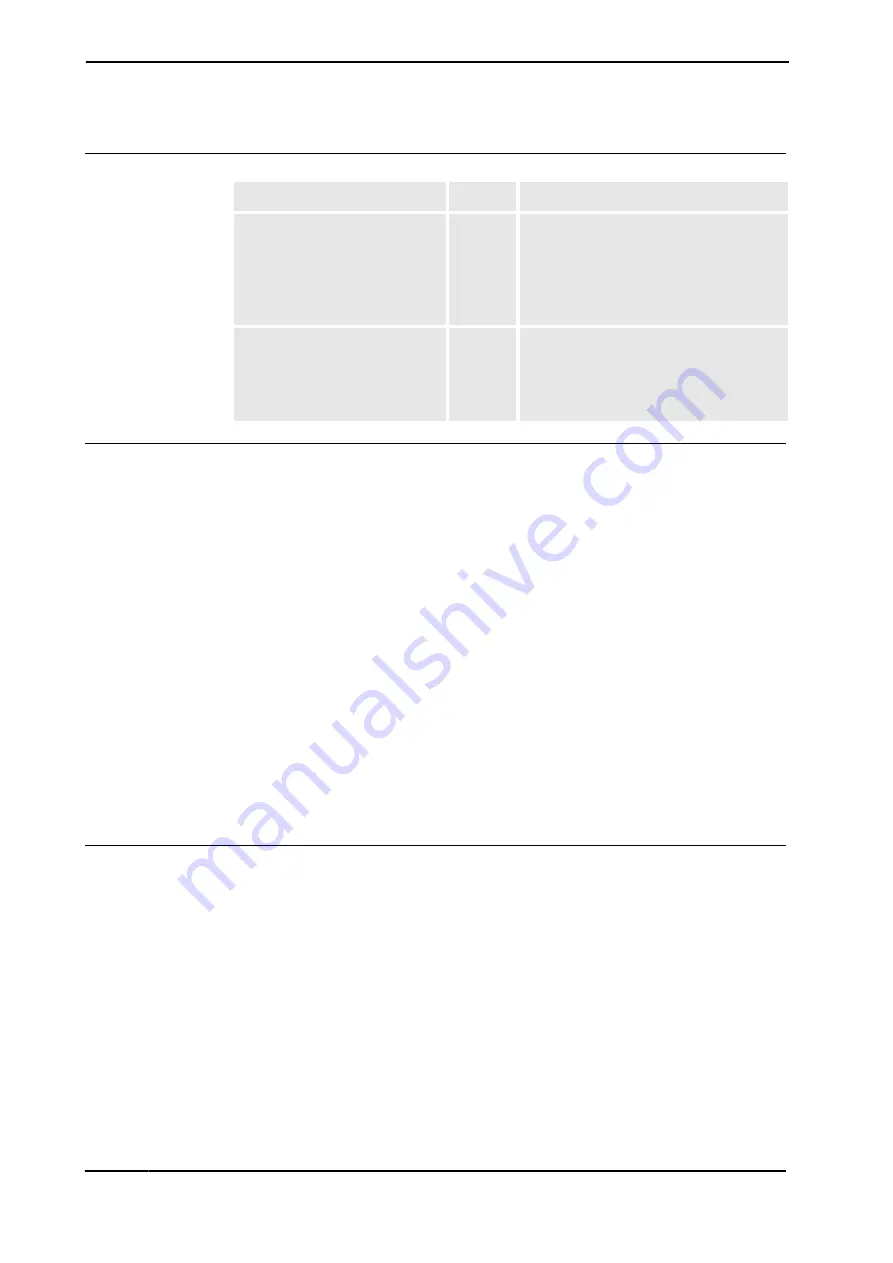
3 Maintenance
3.6.1. Cleaning, robot
3HAC026876-001 Revision: C
186
© Copyri
ght
200
6-2008 ABB.
All rights reserved.
Required equipment
Do's and don'ts!
The section below specifies some special considerations when cleaning the robot.
Always!
•
Always use cleaning equipment as specified above! Any other cleaning equipment
may shorten the life of paintwork, rust inhibitors, signs, or labels!
•
Always check that all protective covers are fitted to the robot before cleaning!
Never!
•
Never point the water jet at bearing seals, contacts, and other seals!
•
Never spray from a distance closer than 0.4 m!
•
Never remove any covers or other protective devices before cleaning the robot!
•
Never use any cleaning agents, for example compressed air or solvents, other than
those specified above!
•
Never spray with a high pressure cleaner onto the sealing cup at the bottom of the
motor 6 spiral cable (item A in the figure Special points)!
•
Although the robot is watertight, avoid spraying connectors and similar items with a
high pressure cleaner!
Foundry Plus versions
In working environments, for example foundries, where the robot may be exposed to fluids
that dry to make a crusty surface, for example release agents, clean the cable harnesses to
prevent the crust damaging the cables:
•
Clean the spiral wound cables to motor 6 (item A in the figure
) with water and a cloth!
•
Clean the remaining sections of the cable harnesses as detailed above!
Equipment, etc.
Art. no.
Note
Steam cleaner
-
•
Water pressure at nozzle: max.
2,500 kN/m
2
(25 bar)
•
Type of nozzle: fan jet, min. 45°
spread
•
Flow: max. 100 litres/min.
•
Water temperature: max. 80° C
High pressure water cleaner
-
•
Max. water pressure on enclosures:
50 kN/m
2
(0.5 bar)
•
Fan jet nozzle should be used, min.
45° spread
•
Flow: max. 100 litres/min.
Continued