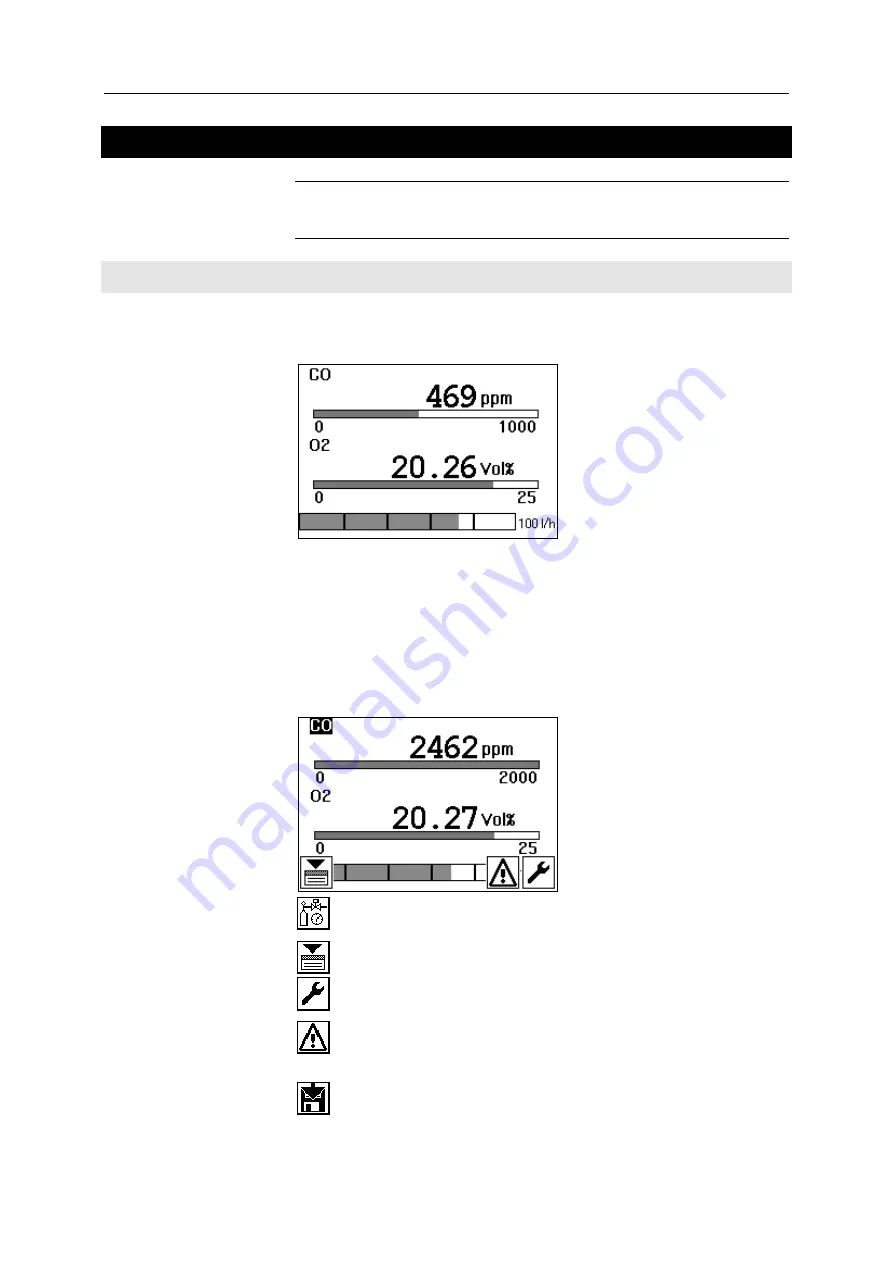
100
EasyLine EL3000 Series Commissioning Instructions
Operating the Gas Analyzer
NOTE
All the illustrations of the displays in this operator's manual are examples.
The displays on the instrument will normally differ from these.
Display - Measuring Mode
Display in Measuring Mode
In measuring mode, the screen displays the name, the measured value in
numerals and the physical unit of the measured value for each sample
component.
If the display of the name of the sample components flashes alternately
with the inverted display, this signals that the measured value exceeds
the measuring range limits.
Status Icons
An automatic calibration is executed. The icon also appears in
the menu title line in menu mode (see page 102).
A status message (see page 122) is active.
The status signal "Maintenance request" is active. The icon also
appears in the menu title line in menu mode (see page 102).
The status signal "Error" is active or the maintenance switch
has been set to "On". The icon is blinking. The icon also
appears in the menu title line in menu mode (see page 102).
The configuration is being saved. The icon is blinking.
Do not switch off the power supply of the gas analyzer when the
icon is displayed!