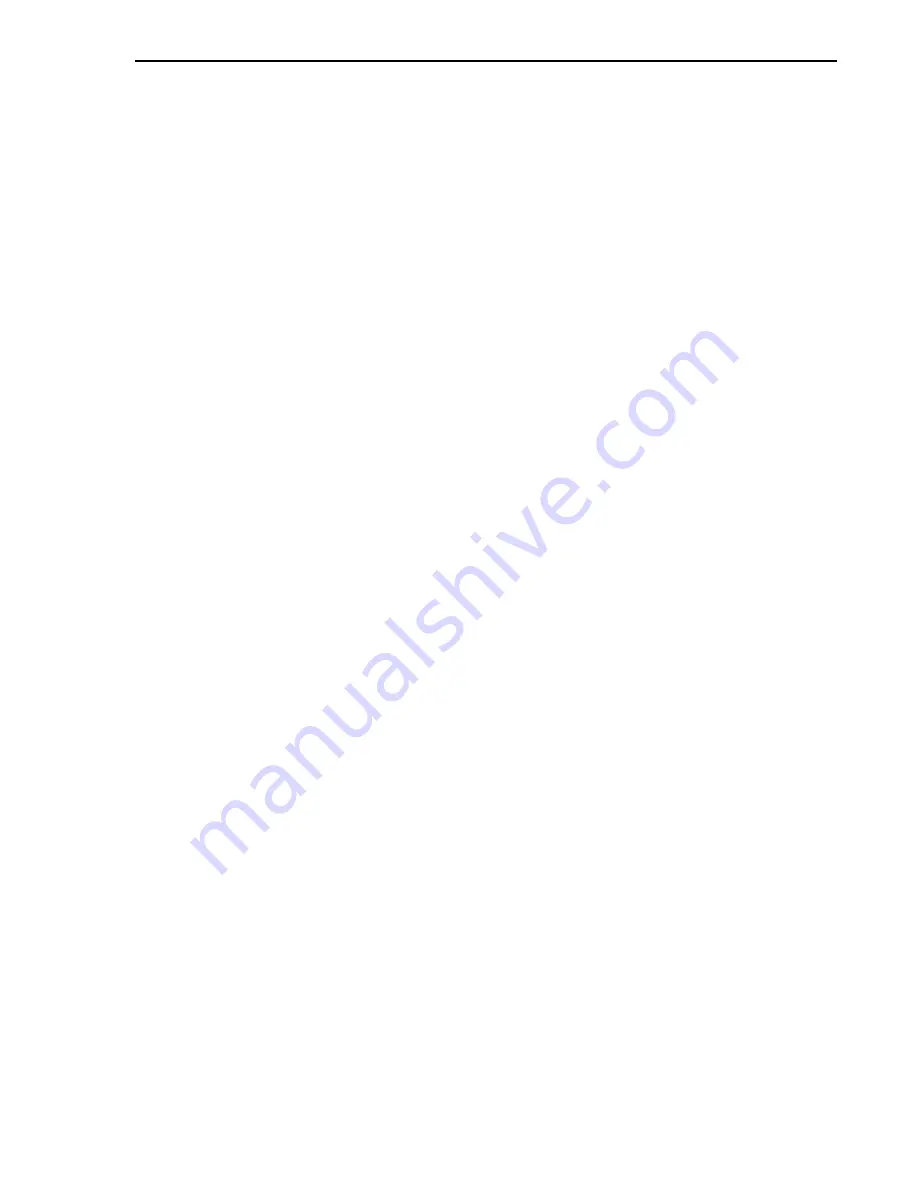
4.2.1.2 Liquid Temperature
Having established the minimum liquid conductivity requirements for a given application, any liquid
which exhibits equal or higher conductivity may be metered without concern for any system compen-
sating adjustments. However, the effect of the liquid conductivity versus temperature should be
considered.
Most liquids exhibit a positive temperature coefficient of conductivity. It is possible for certain
marginal liquids to become sufficiently non-conductive at lower temperatures so as to hamper
accurate metering; whereas, the same liquid at higher or normal environmental temperatures may be
metered with optimum results. The possibility of an adverse temperature conductivity characteristic
should be investigated before attempting to meter such a liquid. Process or ambient temperatures
are limited by the meter materials specification.
Other normal effects of temperature, such as influence upon liquid viscosity and density, the size of
the metering area, and the flux density of the magnetic field, have negligible or no effect upon
metering accuracy.
4.2.1.3 Other Liquid Variables
Other liquid variables such as viscosity, density and liquid pressure have no direct influence on
metering accuracy. Liquid density has no effect on volumetric flow rate since only the area of the
meter pipe and liquid velocity are required to determine the rate of flow. Viscosity and metering
pressure are restricted to physical limitations alone, such as the pressure limits of the meter pipe
flange connections.
4.2.2 Metering Characteristics
The metering pipe must be completely filled at all times for accurate measurement. Where there is a
possibility of operation with a partially filled horizontal pipeline, it is recommended that the meter be
installed in a vertical position so that the process flows upward. A vertical installation offers the
advantage of an even distribution of wear on the meter liner in the event that abrasives are present
in the process stream.
The meter will measure the total amount of material passing in the process stream. The meter will not
differentiate between the amount of liquid and the amount of entrained gases. Also, in the case of a
slurry, the meter will not differentiate between the amount of liquid and solids. If the liquid to mixant
ratio is important for process control, then separate measurements of the concentration of the
medium must be made and appropriate correction factors applied to the meter output.
In applications involving variable quantities of uniformly dispersed, non-conductive mixing agents, it
must be determined that the higher concentrations of mixant will not drive the average conductivity of
the liquid mixture below the minimum conductivity level for the given installation.
10DS3111E INSTRUCTION MANUAL
4-5