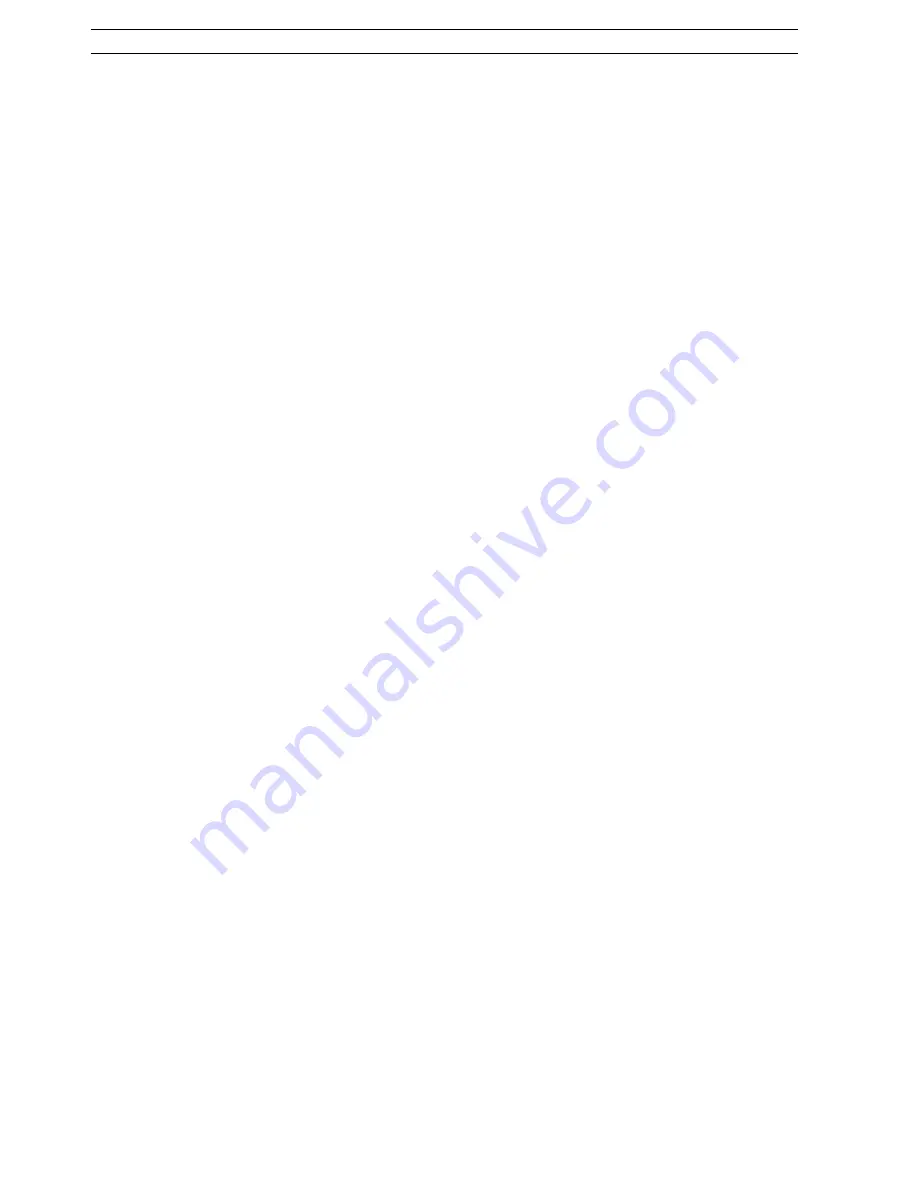
130
Mnemonic
Number
LEVdd
.00
S.CFG
d.01
LEV9, SEt.P
9.00
L.Sr.1
9.08
L.Sr.2
9.09
L.Sr.3
9.10
L.Sr.4
9.11
dF.SP
9.07
SPt.H
9.02
SPt.L
9.03
trCK
9.01
S.PAS
b.10
SSP.H
9.04
SSPL
9.05
S.AdJ
b.04
t.APP
6.01
t.CLK
b.15
t1Sr
A.19
t2Sr
A..20
t3Sr
A.21
t4Sr
A.22
…Configuration Frames
Frame Title
L
Level Heading
Local Set Point Source
Local/Remote Enable
Local/Remote Set Point Source
M
Mains Rejection
Man/Auto Selection Source
Manual 1 Selection Source
Manual 2 Selection Source
Minute Setting (Clock)
MV Calibration selection
MV Feedback – closed
MV Feedback – open
Modbus Address
Modbus Parity
O
O/P Low Limit
O/P High Limit
OP 1 High Limit
OP 2 High Limit
OP 2 Low Limit
Operator Configuration
Output Assignment
Output Slew Rate
Output Slew Rate Disable
Output Type
P
Power Fail Recovery Mode
Power Fail Recovery Time
Process Variable Fail Action
PV Fail Default Output
Profile Operator Password
Profile Configurator Password
R
Ramp/Soak enable
Ratio Display Enable
Regulator Travel Time
Relay 1 Polarity
Relay 1 Source
Relay 2 Polarity
Relay 2 Source
Relay 3 Polarity
Relay 3 Source
Relay 4 Polarity
Relay 4 Source
Remote Set Point Source
RSPT Fault Action
Frame Title
S
Serial Communications
Serial Configuration
Set Point Configuration
Set Point 1 Source
Set Point 2 Source
Set Point 3 Source
Set Point 4 Source
Set Point Default Value
Set Point High Limit
Set Point Low Limit
Set Point Tracking
Set up Password
Slave Set Point High Limit
Slave Set Point Low Limit
Set Point Adjust Disable
T
Template Applications
Time Display
Tune Select Source 1
Tune Select Source 2
Tune Select Source 3
Tune Select Source 4
…FRAMES INDEX
Mnemonic
Number
LEV7
7.00
LC.Sr
9.13
FPLr
b.02
Lr.Sr
9.12
F.rEJ
6.06
AM.Sr
A.16
M.Sr1
A.12
M.Sr2
A.14
MIN
b.14
FCAL
E.07
C.CAL
E.09
O.CAL
E.10
Addr
d.03
PrtY
d.02
OP.LO
A.06
OP.HI
A.05
OP1H
A.07
OP2H
A.08
OP2L
A.09
LEVb, OPEr
b.00
LEVC, ASSn
C.00
OP.Sr
A.10
SrdS
A.11
O.tYP
6.02
P.rEC
A.01
rEC.t
A.02
PVFA
A.03
dF.OP
A.04
O.PAS
b.08
P.PAS
b.09
rP.SK
9.15
r.dIS
b.05
r.trV
E.08
rL1P
C.18
rL1A
C.17
rL2P
C.20
rL2A
C.19
rL3P
C.22
rL3A
C.21
rL4P
C.24
rL4A
C.23
r.SrC
9.14
SP.FA
9.06