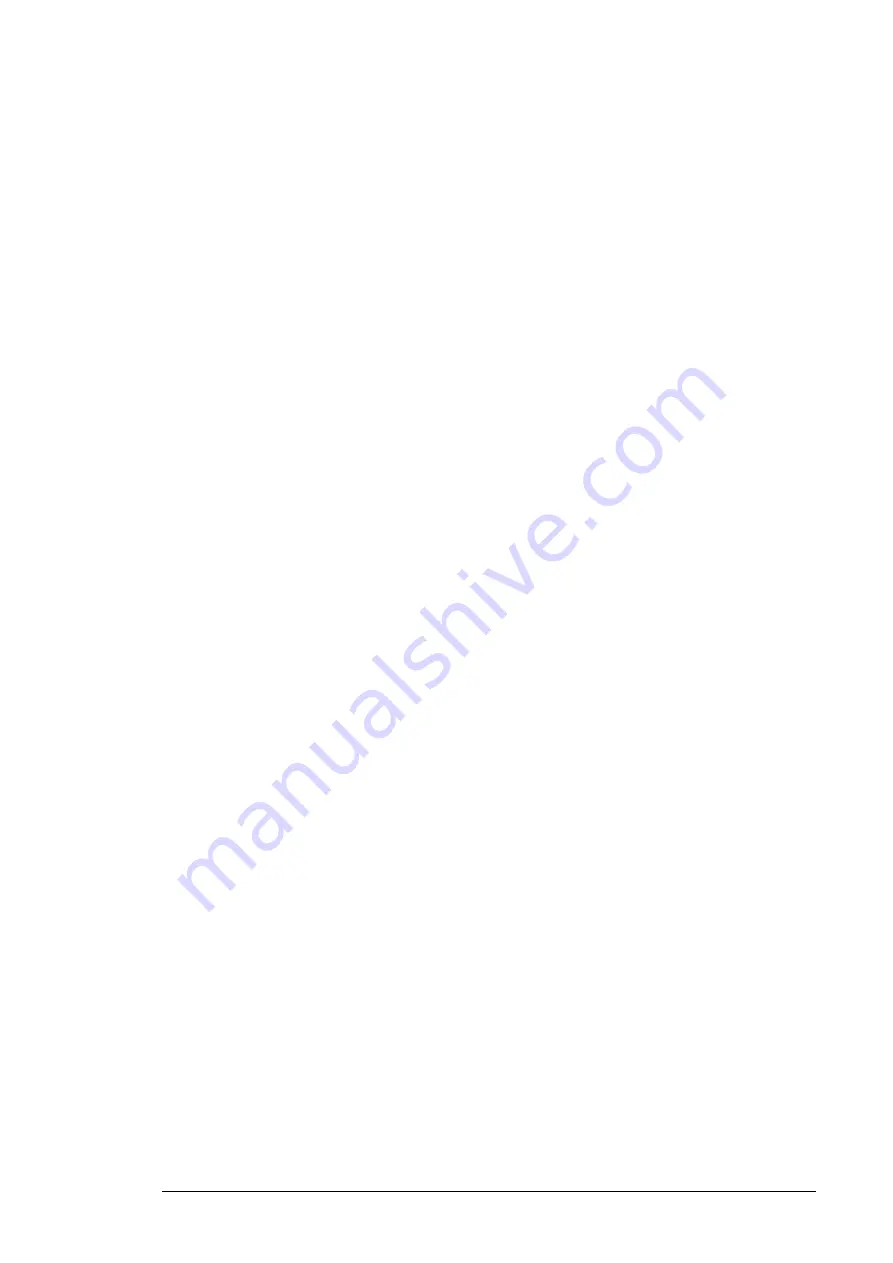
Wiring
For the electrical specifications of the STO connection, see the technical data of the control
unit.
■
Activation switch
In the wiring diagrams, the activation switch has the designation [K]. This represents a
component such as a manually operated switch, an emergency stop push button switch, or
the contacts of a safety relay or safety PLC.
•
In case a manually operated activation switch is used, the switch must be of a type that
can be locked out to the open position.
•
The contacts of the switch or relay must open/close within 200 ms of each other.
•
An FSO safety functions module, an FSPS safety functions module or an FPTC
thermistor protection module can also be used. For more information, see the module
documentation.
■
Cable types and lengths
•
Double-shielded twisted-pair cable is recommended.
•
Maximum cable lengths:
•
300 m (1000 ft) between activation switch [K] and drive control unit
•
60 m (200 ft) between multiple drives
•
60 m (200 ft) between external power supply and first control unit
•
30 m (100 ft) between BCU control unit and last inverter module in the chain.
Note:
A short-circuit in the wiring between the switch and an STO terminal causes a
dangerous fault. Therefore, it is recommended to use a safety relay (including wiring
diagnostics) or a wiring method (shield grounding, channel separation) which reduces or
eliminates the risk caused by the short-circuit.
Note:
The voltage at the STO input terminals of the control unit (or frame R8i inverter module)
must be at least 17 V DC to be interpreted as “1”.
The pulse tolerance of the input channels is 1 ms.
■
Grounding of protective shields
•
Ground the shield in the cabling between the activation switch and the control unit at
the control unit only.
•
Ground the shield in the cabling between two control units at one control unit only.
•
Do not ground the shield in the cabling between BCU and R8i module, or between R8i
modules.
The Safe torque off function 219
Summary of Contents for ACS880-37LC-0390A-7
Page 1: ... ABB INDUSTRIAL DRIVES ACS880 37LC drives Hardware manual ...
Page 2: ......
Page 4: ......
Page 13: ...16 Resistor braking Further information Table of contents 13 ...
Page 14: ...14 ...
Page 24: ...24 ...
Page 28: ...28 ...
Page 50: ...50 ...
Page 70: ...70 Mechanical installation ...
Page 110: ...10 110 Electrical installation ...
Page 113: ...With FDPI 02 modules OPEN TERMINATED 1 1 2 2 OPEN TERMINATED 3 Electrical installation 113 11 ...
Page 134: ...134 ...
Page 140: ...140 ...
Page 148: ...a b c 148 Maintenance ...
Page 151: ...4 5 6 Maintenance 151 ...
Page 164: ...164 ...
Page 174: ...174 ...
Page 196: ...196 ...
Page 199: ... Dimension drawing examples ACS880 37LC 0390A 7 with main contactor Dimensions 199 ...
Page 201: ...ACS880 37LC 1270A 7 with common motor terminal cubicle Dimensions 201 ...
Page 202: ...ACS880 37LC 1940A 7 with common motor terminal cubicle 202 Dimensions ...
Page 205: ...Location and size of input terminals Contact ABB for details Dimensions 205 ...
Page 206: ... 100 kA input cubicle option F274 206 Dimensions ...
Page 208: ...Inverter module cubicle with two R8i modules bottom cable exit 208 Dimensions ...
Page 209: ...Inverter module cubicle with three R8i modules bottom cable exit Dimensions 209 ...
Page 210: ...Brake chopper cubicle 210 Dimensions ...
Page 212: ...Cubicle width 300 mm top cable exit 212 Dimensions ...
Page 213: ...Cubicle width 400 mm bottom cable exit Dimensions 213 ...
Page 214: ...Cubicle width 400 mm top cable exit 214 Dimensions ...
Page 215: ...Cubicle width 600 mm bottom cable exit Dimensions 215 ...
Page 216: ...Cubicle width 600 mm top cable exit 216 Dimensions ...
Page 238: ...238 ...
Page 240: ...240 ...