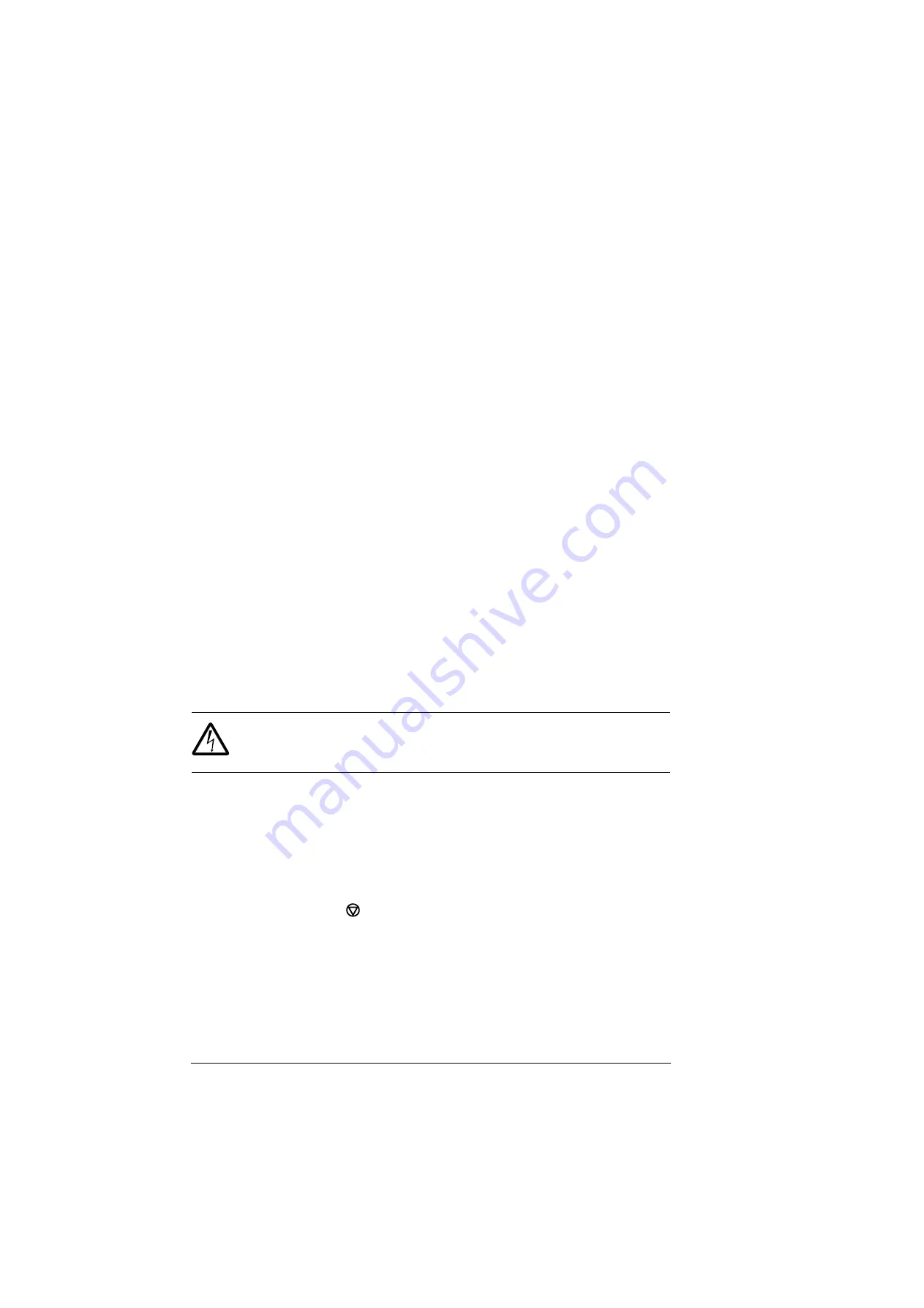
70 Guidelines for planning the electrical installation
indication given by motor temperature sensors. The user can tune the thermal model
further by feeding in additional motor and load data.
The most common temperature sensors are:
•
motor sizes IEC 180…225: thermal switch, eg, Klixon
•
motor sizes IEC 200…250 and larger: PTC or Pt100.
See the firmware manual for more information on the motor thermal protection, and the
connection and use of the temperature sensors.
Protecting the drive against ground faults
The drive is equipped with an internal ground fault protective function to protect the drive
against ground faults in the motor and motor cable in TN (grounded) networks. This is not
a personal safety or a fire protection feature. The ground fault protective function can be
disabled with a parameter, refer to the firmware manual.
Measures for protection in case of direct or indirect contact, such as separation from the
environment by double or reinforced insulation or isolation from the supply system by a
transformer, can be applied.
Residual current device compatibility
The drive is suitable to be used with residual current devices of Type B.
Note:
The EMC filter of the drive includes capacitors connected between the main circuit
and the frame. These capacitors and long motor cables increase the ground leakage
current and can cause fault current circuit breakers to function.
Connecting drive modules to a common DC system
Do not connect the drive module to a common DC system.
WARNING!
The UDC+ and UDC- terminals of the drive module must not be used
for any other than optional external brake chopper connection. Drives connected
to a common DC system will get damaged.
Implementing the Emergency stop function
For safety reasons, install the emergency stop devices at each operator control station
and at other operating stations where emergency stop may be needed. You can implement
the emergency stop function using the Safe torque off function of the drive module (see
chapter
on page
). Design the emergency stop according to
relevant standards.
Note:
Pressing the stop key
on the control panel of the drive does not generate an
emergency stop of the motor or separate the drive from dangerous potential.
Implementing the Safe torque off function
Summary of Contents for ACS880-34
Page 1: ... ABB INDUSTRIAL DRIVES ACS880 34 drive modules 132 to 400 kW 200 to 450 hp Hardware manual ...
Page 4: ......
Page 14: ...14 ...
Page 22: ...22 Safety instructions ...
Page 28: ...28 Introduction to the manual ...
Page 42: ...42 Operation principle and hardware description ...
Page 118: ...118 External control unit ...
Page 140: ...140 Installation example with full cabling panels option H381 M8 16 Hex 2 5 4 3 1 1 1 1 2 6 7 ...
Page 152: ...152 Installation checklist ...
Page 156: ...156 Start up ...
Page 158: ...158 Fault tracing ...
Page 174: ...174 Maintenance ...
Page 202: ...202 Technical data EU Declaration of Conformity Machinery Directive ...
Page 204: ...204 Technical data ...
Page 206: ...206 Dimension drawings Standard configuration 3AXD50000038012 ...
Page 208: ...208 Dimension drawings Drive module with options 0B051 H356 0H371 3AXD50000038012 ...
Page 209: ...Dimension drawings 209 Configuration with option H381 3AXD50000323210 ...
Page 210: ...210 Dimension drawings LCL filter module 3AXD50000206162 ...
Page 214: ...214 Dimension drawings External control unit 3axd50000011687 ...
Page 238: ...238 Resistor braking ...
Page 242: ...242 du dt and sine filters ...
Page 256: ...Contact us www abb com drives www abb com drivespartners 3AXD50000035191 Rev B EN 2018 09 28 ...