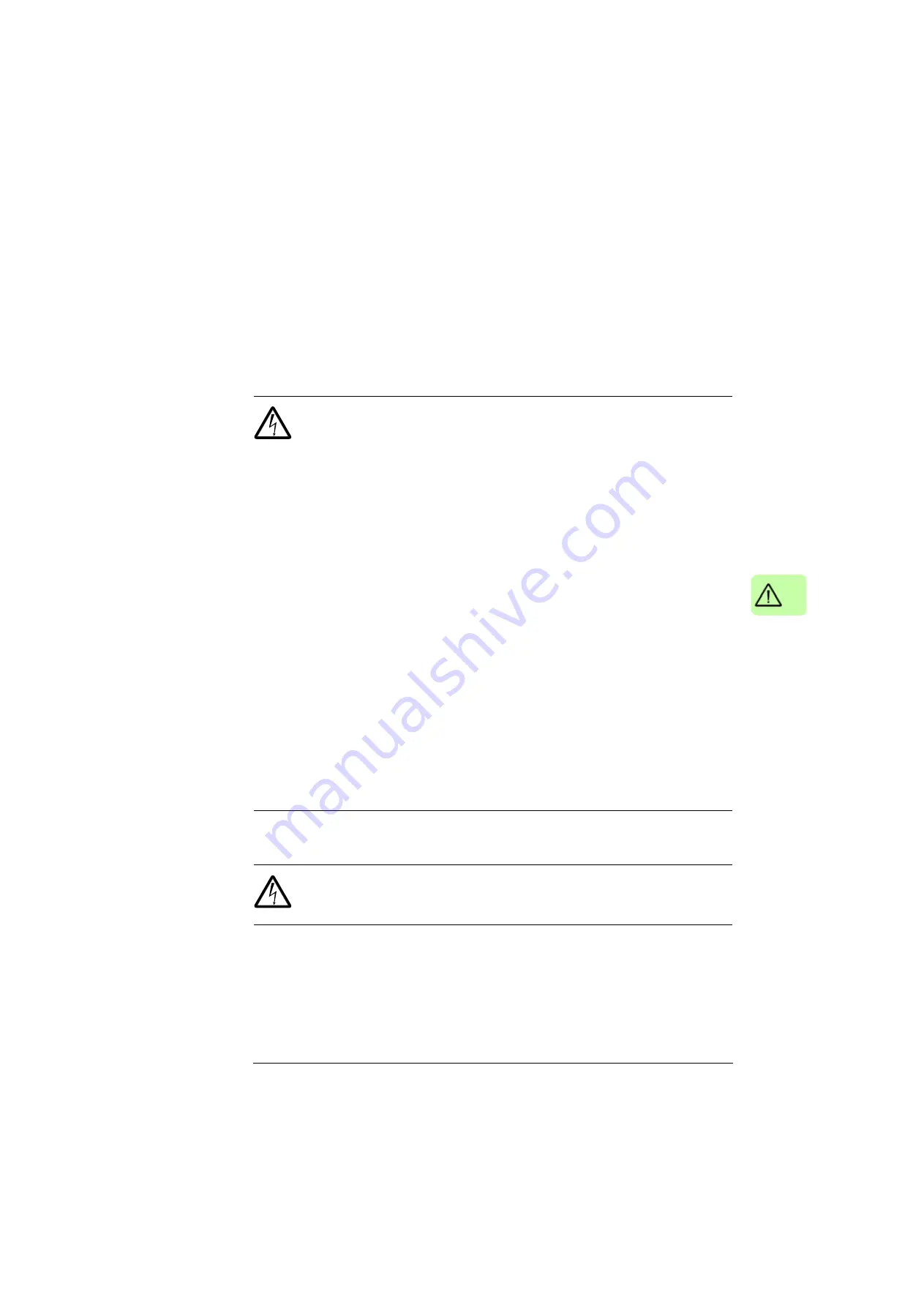
Safety instructions 21
Additional instructions for permanent magnet motor
drives
Safety in installation, start-up and maintenance
These are additional warnings concerning permanent magnet motor drives. The other
safety instructions in this chapter are also valid.
WARNING!
Obey these
instructions. If you ignore them, injury or death and
equipment malfunction can occur.
•
Do not do work on the drive when the permanent magnet motor is rotating. A rotating
permanent magnet motor energizes the drive including its input power terminals.
Before installation, start-up and maintenance work on the drive:
•
Stop the motor.
•
Disconnect the motor from the drive with a safety switch or by other means.
•
If you cannot disconnect the motor, make sure that the motor cannot rotate during
work. Make sure that no other system, like hydraulic crawling drives, can rotate the
motor directly or through any mechanical connection like felt, nip, rope, etc.
•
Measure that the installation is de-energized.
•
Use a multimeter with an impedance of at least 1 Mohm.
•
Make sure that the voltage between the drive output terminals (T1/U2, T2/V2,
T3/W2) and the grounding (PE) busbar is close to 0 V.
•
Make sure that the voltage between the drive input power terminals (L1/U1,
L2/V1, L3/W1) and the grounding (PE) busbar is close to 0 V.
•
Make sure that the voltage between the drive module UDC+ and UDC- terminals
and the grounding (PE) busbar is close to 0 V.
•
Install temporary grounding to the drive output terminals (T1/U2, T2/V2, T3/W2).
Connect the output terminals together as well as to the PE.
•
Make sure that the operator cannot run the motor over the rated speed. Motor
overspeed causes overvoltage can damage or explode the capacitors in the
intermediate circuit of the drive.
Additional instruction for DC connection
WARNING!
The UDC+ and UDC- terminals of the drive module must not be used
for any other than optional external brake chopper connection. Drives connected
to a common DC system will get damaged.
Summary of Contents for ACS880-34
Page 1: ... ABB INDUSTRIAL DRIVES ACS880 34 drive modules 132 to 400 kW 200 to 450 hp Hardware manual ...
Page 4: ......
Page 14: ...14 ...
Page 22: ...22 Safety instructions ...
Page 28: ...28 Introduction to the manual ...
Page 42: ...42 Operation principle and hardware description ...
Page 118: ...118 External control unit ...
Page 140: ...140 Installation example with full cabling panels option H381 M8 16 Hex 2 5 4 3 1 1 1 1 2 6 7 ...
Page 152: ...152 Installation checklist ...
Page 156: ...156 Start up ...
Page 158: ...158 Fault tracing ...
Page 174: ...174 Maintenance ...
Page 202: ...202 Technical data EU Declaration of Conformity Machinery Directive ...
Page 204: ...204 Technical data ...
Page 206: ...206 Dimension drawings Standard configuration 3AXD50000038012 ...
Page 208: ...208 Dimension drawings Drive module with options 0B051 H356 0H371 3AXD50000038012 ...
Page 209: ...Dimension drawings 209 Configuration with option H381 3AXD50000323210 ...
Page 210: ...210 Dimension drawings LCL filter module 3AXD50000206162 ...
Page 214: ...214 Dimension drawings External control unit 3axd50000011687 ...
Page 238: ...238 Resistor braking ...
Page 242: ...242 du dt and sine filters ...
Page 256: ...Contact us www abb com drives www abb com drivespartners 3AXD50000035191 Rev B EN 2018 09 28 ...