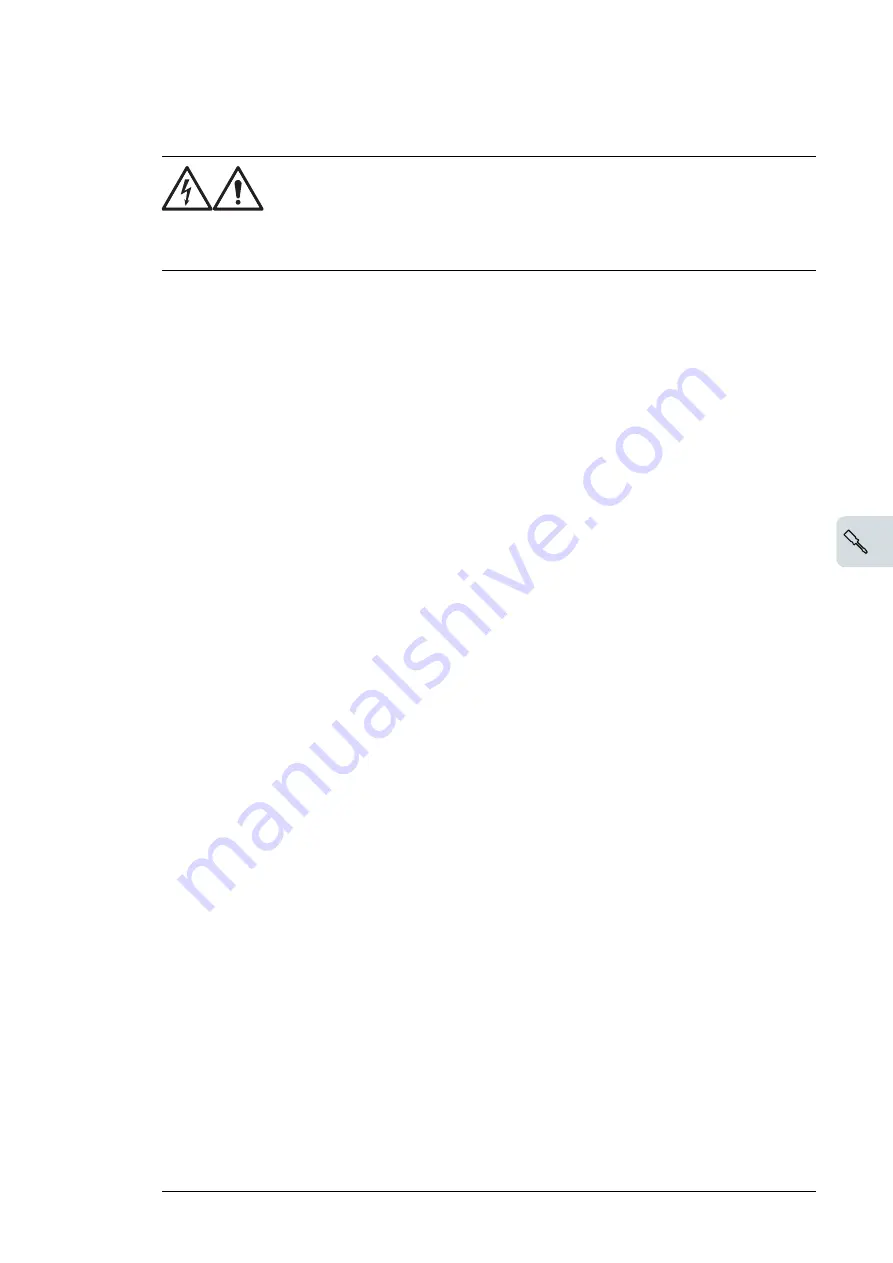
■
Motor cable connection procedure
WARNING!
Read and follow the instructions given in
Safety instructions for ACS880
multidrive cabinets and modules
(3AUA0000102301 [English]). Ignoring
the instructions can cause physical injury or death, or damage to the
equipment.
Refer to the illustrations below.
1.
Do the steps in section
Electrical safety precautions (page 57)
before you start the work.
2.
Remove the shroud covering the lower part of the cubicle.
3.
Run the cable into the cubicle through the cable cable entries provided. In case a
grounding cable gland is available, remove the outer jacket of the cable where it passes
through the cable gland (a).
4.
Cut the cable to suitable length and strip the ends of the individual conductors. Twist
the shield strands together to form a separate conductor and wrap it with tape.
5.
Crimp suitable lug terminals onto the phase conductors and the ground conductor. The
dimensions of the output busbars are shown in the technical data.
6.
Connect the shield (and any grounding conductors) of the cable to the PE busbar close
to the cable entries.
7.
Connect the phase conductors of the motor cable to the U2, V2 and W2 terminals.
8.
Secure the cable mechanically. It is recommended to arrange for 360° grounding of the
shield at the cable entry; an example is shown in the detail drawing (b).
9.
Connect the control cables as described in section Connecting the control cables.
10. Refit the shroud.
11. At the motor, connect the cables according to instructions from the motor manufacturer.
Pay special attention to the phase order. For minimum radio-frequency interference,
ground the cable shield 360 degrees at the cable entry of the motor terminal box, or
ground the cable by twisting the shield so that the flattened shield is wider than 1/5 of
its length.
Electrical installation 63
11
Summary of Contents for ACS880-107
Page 1: ... ABB INDUSTRIAL DRIVES ACS880 107 inverter units Hardware manual ...
Page 2: ......
Page 4: ......
Page 10: ...10 ...
Page 64: ...2 4 5 6 7 8 11 10 3 a b a b b 1 5 a 64 Electrical installation ...
Page 69: ...Electrical installation 109 5 6 4 3 Electrical installation 69 11 ...
Page 70: ...7 a b d c 110 Electrical installation 7 8 8 8 9 9 70 Electrical installation ...
Page 75: ...2 11 b PE 10 7 5 6 8 a 360 grounding detail Electrical installation 75 11 ...
Page 89: ...With FDPI 02 modules OPEN TERMIN ATED 1 1 2 2 OPEN TERMINATED 3 Electrical installation 89 11 ...
Page 90: ...90 ...
Page 96: ...96 ...
Page 110: ...4 5 6 7 8 6 10 10 110 Maintenance ...
Page 118: ...2 3 7 9 a a c c c 6 8 b b d d 11 e e 118 Maintenance ...
Page 121: ...7 a b d c 110 Electrical installation 7 8 8 8 9 9 Maintenance 121 ...
Page 130: ...130 ...
Page 154: ...154 ...
Page 155: ...Circuit diagrams Refer to the circuit diagrams delivered with the unit 9 Circuit diagrams 155 ...
Page 156: ...156 ...
Page 159: ... Dimension drawing 400 mm wide cubicle R1i R4i 400 mm R6i R7i Dimensions and weights 159 ...
Page 161: ... Dimension drawing R8i without C128 or H353 bottom cable exit Dimensions and weights 161 ...
Page 162: ... Dimension drawing R8i without C128 or H353 top cable exit 162 Dimensions and weights ...
Page 163: ... Dimension drawing 2 R8i without C128 or H353 bottom cable exit Dimensions and weights 163 ...
Page 164: ... Dimension drawing 2 R8i without C128 or H353 top cable exit 164 Dimensions and weights ...
Page 165: ... Dimension drawing 3 R8i without C128 or H353 bottom cable exit Dimensions and weights 165 ...
Page 166: ... Dimension drawing 3 R8i without C128 or H353 top cable exit 166 Dimensions and weights ...
Page 167: ... Dimension drawing drive control unit DCU 300 mm Dimensions and weights 167 ...
Page 169: ...Inverter module cubicle with one R8i module top cable exit Dimensions and weights 169 ...
Page 182: ...182 ...
Page 200: ...200 ...