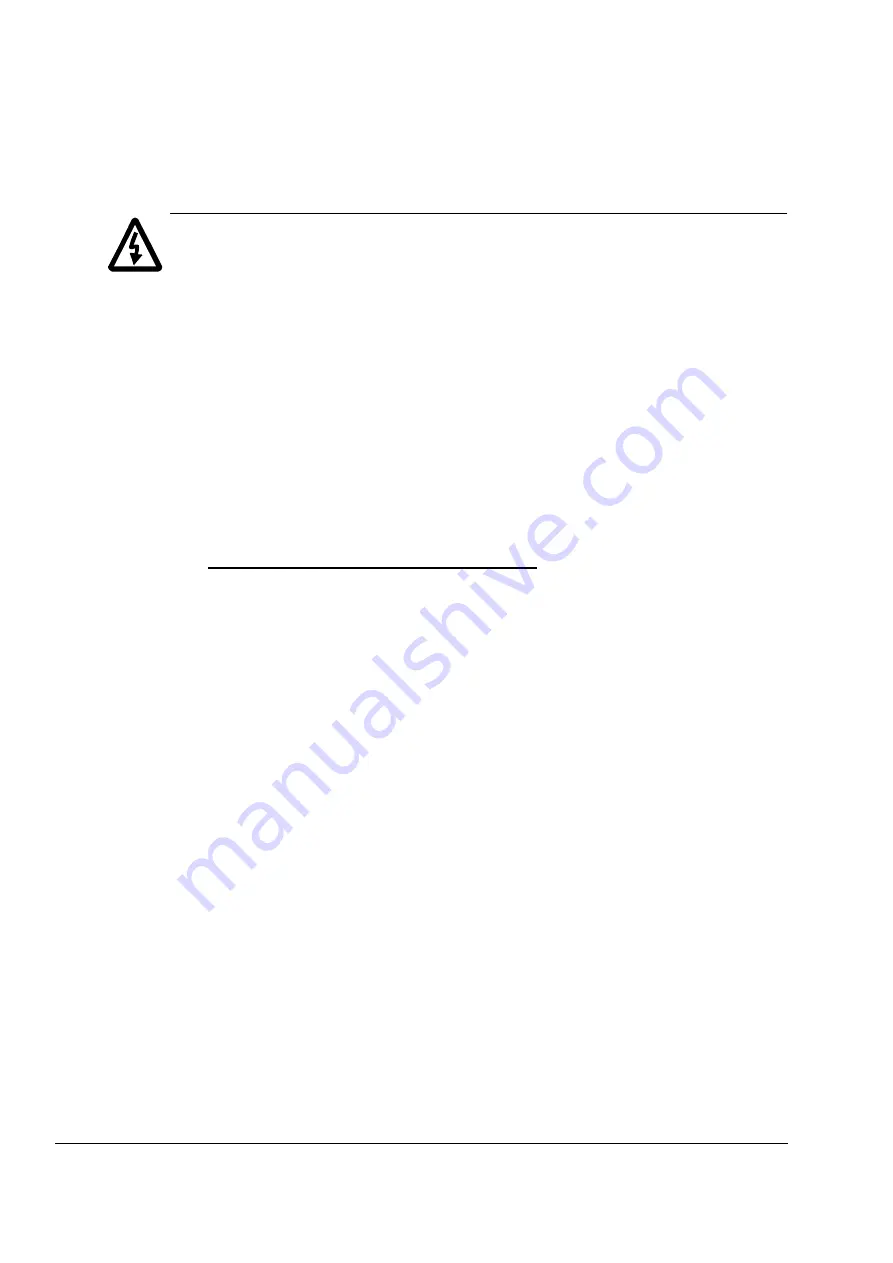
Safety instructions
6
Installation and
maintenance work
These warnings are intended for all who work on the drive, motor cable or motor.
WARNING!
Ignoring the following instructions can cause physical injury or death, or
damage to the equipment.
Only qualified electricians are allowed to install and maintain the drive.
•
Never work on the drive, the motor cable or the motor when input power is
applied. After disconnecting the input power, always wait for 5 minutes to let the
intermediate circuit capacitors discharge before you start working on the drive,
the motor or the motor cable.
Always ensure by measuring with a multimeter (impedance at least 1 Mohm)
that:
1. There is no voltage between the drive input phases U1, V1 and W1 and the
ground.
2. There is no voltage between terminals UDC+ and UDC– and the ground.
3. There is no voltage between terminals R+ and R– and the ground.
•
Drives controlling a permanent magnet motor: A rotating permanent magnet
motor feeds power to the drive causing the drive to become live even when it is
stopped and the supply power switched off. Before maintenance work on the
drive,
– disconnect the motor from the drive by using a safety switch
– prevent the start-up of any other motors in the same mechanical system
– lock the motor shaft
– measure that the motor is in fact de-energised, then connect the U2, V2 and
W2 terminals of the drive to each other and to the PE.
•
Do not work on the control cables when power is applied to the drive or to the
external control circuits. Externally supplied control circuits may carry
dangerous voltages even when the input power of the drive is switched off.
•
Do not make any insulation or voltage withstand tests on the drive.
•
If a drive whose varistors or internal EMC filters are not disconnected is
installed on an IT power system (an ungrounded power system or a high
resistance grounded [over 30 ohms] power system), the drive will be connected
to earth potential through the varistors/filters. This may cause danger or
damage the drive.
•
If a drive whose varistors or internal EMC filter are not disconnected is installed
on a corner-grounded TN system, the drive will be damaged.
Notes:
•
Even when the motor is stopped, dangerous voltages are present at the power
circuit terminals U1, V1, W1 and U2, V2, W2, and UDC+, UDC–, R+, R–.
Summary of Contents for ACS850 series
Page 1: ...ACS850 Hardware Manual ACS850 04 Drive Modules 1 1 to 45 kW...
Page 2: ......
Page 4: ......
Page 14: ...Table of contents 14...
Page 20: ...About this manual 20...
Page 32: ...Planning the cabinet assembly 32...
Page 38: ...Mechanical installation 38...
Page 48: ...Planning the electrical installation 48...
Page 50: ...Electrical installation 50 1 2 3 4 5...
Page 68: ...Electrical installation 68...
Page 76: ...Maintenance 76...
Page 102: ...du dt and common mode filtering 102...
Page 108: ...Dimension drawings 108 Frame size A...
Page 109: ...Dimension drawings 109 Frame size B...
Page 110: ...Dimension drawings 110 Frame size C...
Page 111: ...Dimension drawings 111 Frame size D...
Page 113: ...Dimension drawings 113 EMC filters type JFI x1 JFI A1...
Page 114: ...Dimension drawings 114 JFI B1...
Page 115: ...Dimension drawings 115 EMC filters type JFI 0x...
Page 117: ...Dimension drawings 117 Braking resistors type JBR xx...