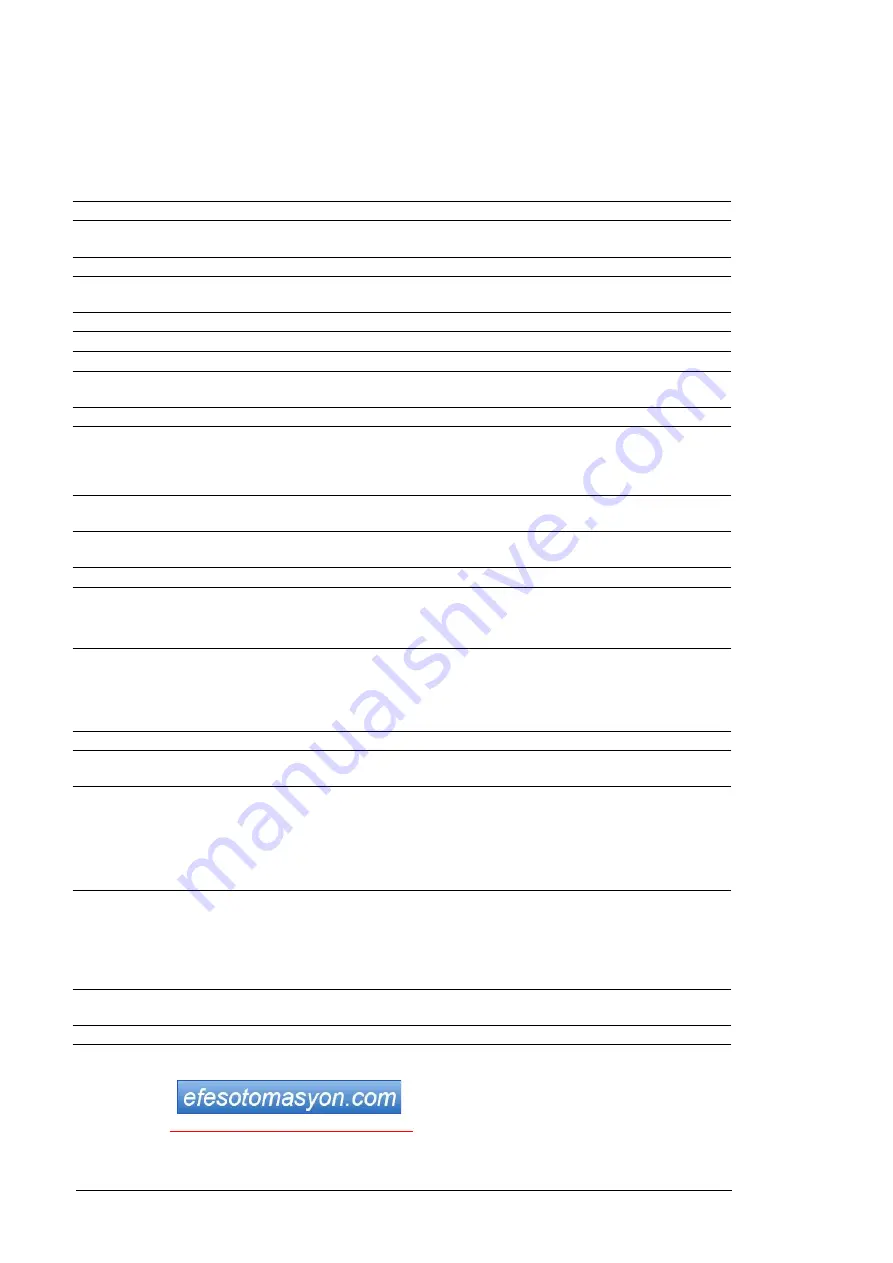
90 Installation checklist
Instrumentation, busbars and cabling
Checks for instrumentation, busbars, cabling, clearances and creepage distances are
listed below. For more information, see chapter
Planning the electrical installation
2
Instrumentation
2.1
Type and number of option modules and other equipment is correct. Option modules and other
equipment are not damaged.
2.2
Option modules and terminals are labelled correctly.
2.3
The placement of option modules and other equipment inside the cabinet and on the cabinet door is
correct.
2.4
The mounting of option modules and other equipment is correct.
3
Busbars
3.1
The types (Al/Cu) and cross-sections of busbars are correct.
3.2
Busbars are intact and joint surfaces are clean. There are no metal scraps on the busbars that could
cause a short-circuit.
3.3
The placement and mounting of busbars is correct.
3.4
The electrical connection of busbars.
Check that the surfaces in electrical connections of aluminium
and uncoated busbars are rubbed. Check that anti-oxidant joint compound is used in electrical
connections of aluminium busbars. Check that the number of washers and the sizes of bolts are
correct.
3.5
Busbar supports and lead-in insulators are visually intact and degreased, and placed and mounted
correctly.
3.6
The electrical connections on the main circuit are tightened to required torque and marked with a
green marking.
4
Cabling and wiring
4.1
Wiring of the main circuit. Check
• AC supply input
• AC output
4.2
Wiring of the drive module control circuit. Check
• JCU Control Unit connections
• control cable connections
• control panel cable connections.
4.3
Cable types, cross-sections, colors and optional markings are correct.
4.4
Check the cabling for circuits susceptible to interference. Check the twisting of cables and cable
routes.
4.5
Check that cables without short-circuit protection
• can carry the load current
• are shorter than 3 m (10 ft)
• are assembled separate to other cables
• are protected by an enclosure or duct.
4.6
Connection of cables to devices and terminal blocks. Check that
• cables are connected to terminals tight enough by pulling the cable
• cable termination on terminals chaining is done correctly
• bare conductors are not too far outside the terminal causing an insufficient clearance or loss of
shielding against contact.
4.7
Cables are not lying against sharp edges or bare live parts. Bending radius of fiber optic cables at least
3.5 cm (1.38 in.).
4.8
The type, markings, insulation plates and cross connections of terminal blocks are correct.
Summary of Contents for ACQ810
Page 1: ...ABB industrial drives Hardware manual ACQ810 drive modules 200 to 400 kW 250 to 600 hp...
Page 4: ......
Page 16: ...16 Safety instructions...
Page 30: ...30 Operation principle and hardware description...
Page 69: ...Planning the electrical installation 69 Example circuit diagram See page 129...
Page 70: ...70 Planning the electrical installation...
Page 88: ...88 Electrical installation...
Page 94: ...94 Start up...
Page 96: ...96 Fault tracing...
Page 122: ...122 Dimension drawings Frame without pedestal mm 64801082_3 6 E Center of gravity...
Page 123: ...Dimension drawings 123 Frame with busbars on the left side mm 64801082_5 6 E...
Page 125: ...Dimension drawings 125 Package...
Page 128: ...128 Dimension drawings...
Page 132: ...132 du dt filters and sine filters Sine filters Contact your local ABB representative...