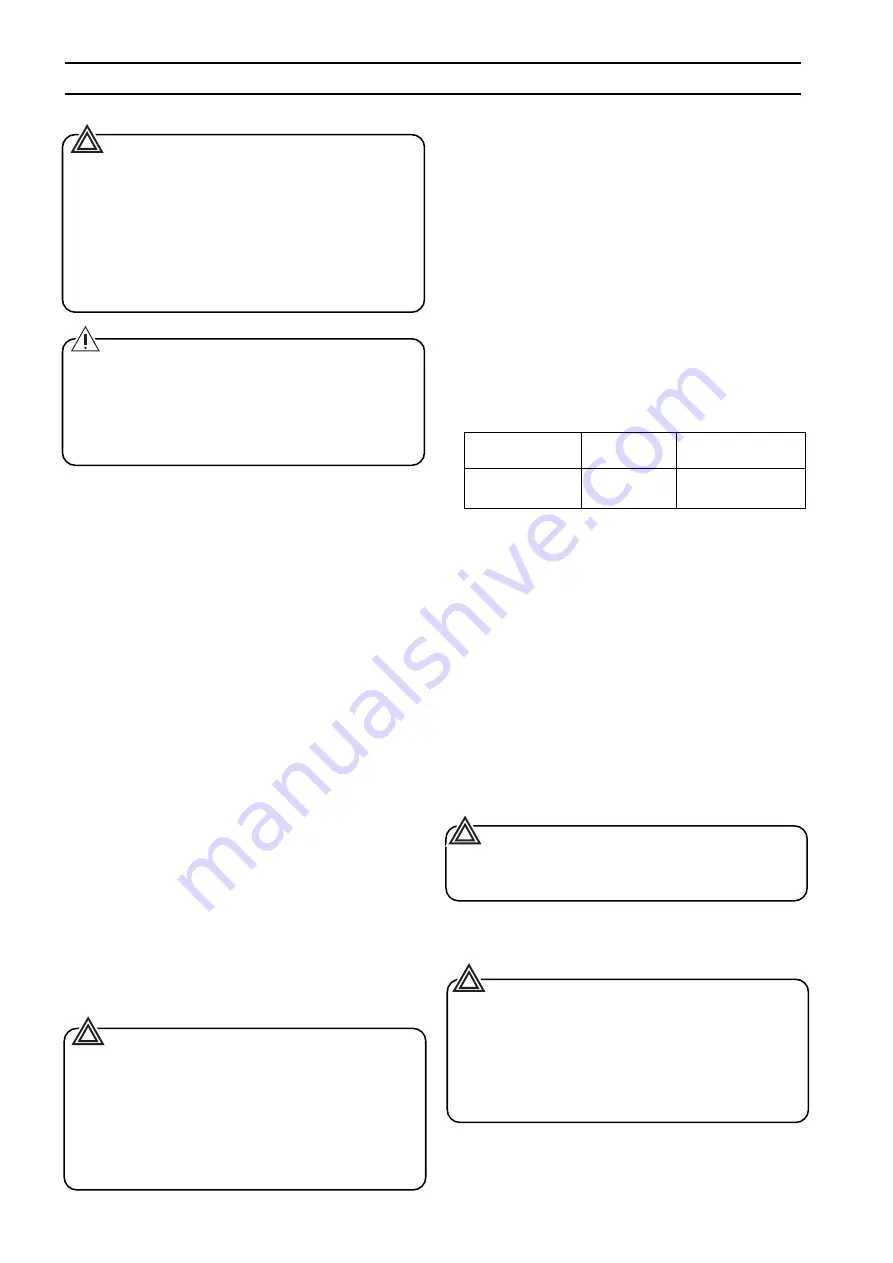
- 14 -
. . . DISMANTLING AND REASSEMBLY
WARNING - Process fluids and/or pressure retained
in the transmitter primary unit can cause severe injury and
death or damage to the equipment. It is the user
responsibility to make sure that no pressure is applied
before removing the instrument from service or when
draining or venting.
Dangerous fluids
In case of toxic or otherwise dangerous process fluid, take
any precautions as recommended in the relevant Material
Safety Data Sheet.
CAUTION - Dismantling and reassembly should not
be carried out on site because of the risk of damage to
components and printed circuits as a result of adverse
environmental conditions such as humidity,dust,etc. The
dismantling and reassembly procedures given below
should be carried out in the listed order to avoid instrument
damage.
Required tools
2 mm Allen key
3 mm Allen key
Small Phillips screwdriver
Small flat-bladed screwdriver
17 mm spanner
17 mm torque wrench - (Range > 52 Nm - 39 foot lbs)
Dismantling
a) Screw down completely the cover locking screw, electronics
side, using the 3 mm Allen key
b) Unscrew and remove the covers
c) Unscrew the two fixing screws and remove the
secondary electronic assembly
d) Unplug the sensor cable
e) Remove the tang grub screw using the 2 mm Allen key
f)
Unscrew the housing taking care not to damage the
sensor cable or the connector.
Dismantling the process flanges
If remote seals are fitted do not dismantle the flanges!
1. Unscrew the process flange screws diagonally opposite
each other (13mm Allen key for hexagon screw).
2. Carefully remove the flanges so as not to damage the
isolating diaphragms.
3. Using a soft brush and a suitable solvent thoroughly clean
the isolating diaphragms and, if necessary, the process
flanges. Do not use sharp or pointed tools.
Reassembly
Check that the "O" rings are not damaged: otherwise replace.
WARNING - Assembling flanges with incorrect
fixing bolts and nuts and improper "O rings" can cause
fracture or overstressing of bolts and release of pressurized
process material. Use only official spare parts (*) included
in the supplementary documentation, follow the
reassembly procedure herebelow described and do not
exceed the specified torque limits. DO NOT REMOVE the
"O ring" fitted in the sensor neck: it provides the housing
a degree of protection.
a) Renew the process flange O-rings.
(Spare Parts Data Sheet 15-9.01 EN).
b) Fit the process flanges onto the measuring cell. Take care
not to damage the isolating diaphragms.
Note: The flange faces of the 2 process flanges must be in
one plane and at right angles to the electronic enclosure.
c) Check that the process flange screw thread moves easily:
Tighten the nut by hand as far as the screw head.
If this is not possible, use new screws and nuts (Spare
Parts Data Sheet 15-9.01 EN).
d) Lubricate the screw threads and contact faces of the
screwed joint with, for instance "Anti-Seize AS 040 P"
(Supplier: P.W. Weidling & Sohn GmbH & Co. KG, An der
Kleimannbrücke 49, D 48157 Münster).
With cleanliness stages, the corresponding regulations
must be observed, e.g. DIN 25410!
e) Firstly tighten the diagonally opposite flange screws or
nuts to the initial torque specified in the table 3 below using
a torque wrench.
Then tighten fully by continuing to turn each diagonally
opposite screw or nut gradually, as specified in the table 3,
through the specified tightening angle.
f)
Check for leaks. Apply pressure with max. 1.3 x SWP for
the model 262/264 BS where the pressure has to be
applied simultaneously to both sides of the sensor.
g) Insert the sensor cable in its recess at the bottom of the
housing.
h) Screw the housing down completely until the nesting of
housing/sensor assy is reached, then unscrew by one
complete turn maximum. Rotate the topwork in the
desired position and lock it with the tang grub screw
previously removed.
i)
Plug the sensor cable to the secondary electronics. Fix
the electronic circuit by its screws.
j)
Refit the covers and tighten securely.
WARNING - For Hazardous Location installations, at
least eight (8) threads on the cover must be engaged in
order to meet the flameproof (explosion-proof)
requirements.
k) Unscrew the cover locking screw to secure the covers. This
is mandatory to meet "Flameproof requirements" for
Hazardous Areas installation.
PRESSURE TEST WARNING
Once reassembled the process flanges and the transducer,
a pressure test is required. At this purpose, apply a
hydrostatic pressure of the maximum overrange pressure
rating to both process connections simultaneously. Wait
for one minute, then verify that no leakages occurred,
otherwise repeat the assembly procedure and the pressure
test.
(*) The spare parts list is available at: www.abb.com
- searching for: SL262_4D.pdf
or from local ABB representatives.
FOR MODEL 264BS (Fig. 13b)
Process flange-
O-ring material
Perbunan
Viton EPDM
Initial torque Tightening angle
10 Nm
180
°
devided into
two steps of 90
°
Table 3: Initial torque / Tightening angle
Summary of Contents for 264B
Page 53: ... 53 ...
Page 54: ... 54 ...